
Sign In
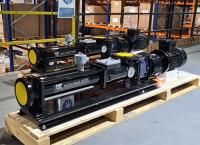
Low Shear ATEX Pumps for Produced Water Improve Oily Water Separator Efficiency – A Client Case Study
Onshore production of Oil and Gas is the process of extracting Oil and Gas from reserves deep below ground. Responsible for approximately 2% of the total UK supply, it is still a vital source of Oil, producing approximately 14000-15000 barrels per day.
To achieve maximum recovery of oil from wells, water is injected into underground wells, flooding the area, and as oil is less dense than the water, oil is brought to the surface and recovered using Oily water separators.
The water used to undertake this process is known as produced water, where after recovery it is recycled and reinjected back into wells. Often Saline or Brackish in nature, it can contain dissolved solids, silt and other particles present within a well’s environment.
An Oil Extraction company contacted us who were looking for two pumps for their processing facility, to feed an Oily Water Separator, as well as inject produced water into a well.
They required a flow ranging from 50 to 200 Litres a minute with a constant pressure of 8 bar. They were unsure of the best technology to handle the emulsion, as viscosity could vary, solids were present, and the pumps needed to be certified to ATEX Zone1 where gas was present.
Initially, when discussing their requirements, they were interested in utilising a high-pressure Centrifugal pump, however, on review of the project requirements, we felt another solution would not only achieve their desired flow and pressure requirements but also improve the efficiency of their Oily Water Separators.
Improving the Efficiency of Oily Water Separators
Oily Water Separators separate water and oil firstly by pumping the fluid through filters to capture droplets, but also by using the liquids natural characteristics -its specific gravity to separate oil, with oil rising above the water and sludge settling at the bottom of tanks.
As oil and water do not mix, when it is pumped it forms an emulsion. If this mixture is pumped with high amounts of shear - produced by some pump types such as centrifugal, the droplets can split forming multiple smaller droplets making separation more difficult.
The efficiency of Oily water separators is improved by utilising progressing cavity pumps, as its design affects oil particles the least due to its low shear movement, meaning separation equipment captures a greater amount of undamaged oil droplets.
Progressing Cavity pumps were rated by the SPE (Society of Petroleum Engineers) in Paper SPE18204 as the preferred pump to use for oil droplets which were found to be disturbed the least during handling against a comparison of lobe, vane and screw technology.
Progressing cavity pumps were chosen as the ideal technology for this project as not only do they handle the oil droplets gently but they produce a constant volume of flow at varying pressures, are affected very little by changes in viscosity and can handle solids without issue.
This is important due to the changing nature of the application. When oil is extracted, initially the produced water content of a well will be kept as low as possible to reduce the amount of oily water treatment required, with volumes increasing as it becomes inevitable due to the lowering level of oil within a well as it is extracted. The amount of water present within a well is often referred to as oily water cut.
What is oily water cut?
Oily water cut is the amount of water produced in a well compared to the amount of oil or solids present which is often expressed as a percentage, with a 30% water cut meaning 30% of the extracted volume contains 30% water.
We specified and supplied two Horizontal Progressing Cavity pumps perfect for the low shear transfer of Oil / Water Mix, capable of a flow range of 50-200 L/min with performance and hydrostatic test to 18 bar. Due to the presence of solids, the Stainless-Steel Rotor was hard chrome plated to protect it from abrasion, prolonging its lifespan.
The units were fitted with PT100 Dry run protection sensors, to ensure pumps could not be run dry, and IP65 ATEX variable speed motors due to the site's exposed location.
If you have an ATEX application and are unsure of the correct solution, contact North Ridge Pumps on 01773 302 660 or submit an online enquiry to see how we can help.
For more information on Low Shear ATEX Pumps for Produced Water Improve Oily Water Separator Efficiency – A Client Case Study talk to North Ridge Pumps Ltd
Enquire Now
List your company on FindTheNeedle.