
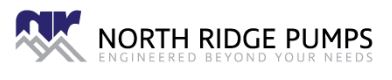
Solvents, Cleaning, and Machinery Today's case study comes from a request made by a pharmaceutical machinery manufacturer who wanted a pump that could handle a wide range of cleaning solvents used for cleaning-in-place (CIP) of mechanical equipment. The solvents used ranged in concentration and consisted of acetone, ethanol, methanol, n-heptane, toluene, and dichloromethane. These chemicals are known for their flammability, hazardous and carcinogenic nature making safety a priority. Additionally, they wanted this handled by a single self-priming pump. The pump had to be capable of drawing heated chemicals from a tank and transferring them at 6 bar via a spraying element. This process would allow for the cleaning of the equipment they desired. What is CIP? Before we get to the solution, let us understand what CIP means. Cleaning in Place (CIP) is an essential step in maintaining plant hygiene. CIP cleaning is mostly performed utilising caustic washes at high temperatures using a dedicated pump via dedicated ports. At times, due to the design of process equipment a spray ball may be required. Spray balls are a type of nozzle used for cleaning vessels or containers at pressure where cleaning fluids would otherwise have difficulty penetrating. Spray balls are designed with a series of holes around the periphery where high pressure fluid is pumped at low flows and high-pressure creating jets of fluid to clean difficult to access process equipment. The SolutionSaniboxer 100 Diaphragm Pump and Dampener Knowing all the specifications required we found the perfect match was our sanitary diaphragm pump, the Saniboxer 100. But why was this pump perfect? The Saniboxer 100 uses stainless steel and PTFE in its construction, this eliminates issues with the solvents. The pump can run dry too and is self-priming, meeting more of the specifications listed. Adding to that, the pump recently had its design improved. This enhanced 5 key features which made it the ideal solution for the client’s applications: Leakage Sensor Traditional diaphragm pumps do not have sensors checking diaphragms for ruptures or leaks. Our improved design contains an optical leakage sensor to immediately detect any leaks for any reason. Should a leak occur, the pump will stop immediately with full containment of any leaked process liquid. The leakage sensor guarantees safety standards when applications handle hazardous materials, limiting and preventing exposure both to humans and the environment. Also, as our design of pump works with non-lubricated air, should any liquid encounter the air side of a diaphragm, you can remain assured the liquid will remain free from contamination as it will not encounter any oils, lubricating media or other contaminating media used in compressed air systems. Easy Clean Internal components are polished to Ra<0.8. This allows for liquids to pass through the pump without sticking to components Should contamination occur, the pump is cleaned easily due to its polished internals.Manual cleaning of the pump is also quick and easy due to the design of the pump being held together via tri clamps allowing for fast disassembly. Additionally, the pump is mounted on a baseplate with swivel brackets. This design enables the pump to be rotated upside down for complete emptying. Fully Certified The Saniboxer 100 is certified for use with chemicals in flammable atmospheres and for hygienic applications. Certified to ATEX for explosive atmospheres, 3A, FDA and MOCA (EC1935/2004) and available with 3.1 material certification ensures it satisfies the most demanding of hygienic requirements. Solid Handling The internal design has been optimized for solid handling, with the internal ball valves being eccentric allowing the unit to handle large solids. A flap valve variant of this design enables solid handling without damage for materials up to 45mm in diameter, and 600mm in length. Fewer Parts than other designs Due to its efficient design each pump contains fewer than half the number of parts of other similar pumps. This means units can be overhauled up to 50% quicker than others. With a diaphragm lifespan of over 50,000,000 cycles and zero lubrication required, the pump guarantees reliability. For this partial application a hygienic pulsation dampener was supplied with the pump. This ensures consistent delivery of pressure to the spray ball. The dampener reduces pulsating flow by up to 98%, ensuring constant pressurised flow. Future Updates The pump was supplied in January 2023, the perfect start to a new year. We'll be keeping track of how things progress with our customer and hope to have an update in the future on their new pump. If you have a process requiring solvent transfer or hygienic applications and are unsure what you need, contact us for expert advice.
For more information on Pumping Solvents for Cleaning-in-Place (CIP) - Case Study talk to North Ridge Pumps Ltd