
Sign In
Unloading Marine Fuel – Case Study
18-11-2022
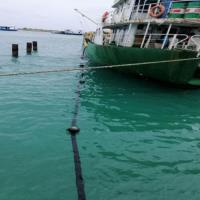
Unloading Marine Fuel – Case Study
Our Customers' Unloading Marine Fuel Woes30 meters of flexible pipe is laid temporarily every time to unload fuel from the boat
In this project, we take a look at an overseas electricity provider, who contacted us needing help diagnosing issues with their marine fuel pump.
They were currently experiencing issues unloading light fuel oil (LFO) from their vessel at the port, with their current marine pump and were struggling to troubleshoot problems and solve them.
The port would regularly receive shipments of fuel cargo by vessel, with vessels docking over fifty meters away from the pump due to the design of the dock.
The unit at the time would operate for approximately 16 hours a day, unloading marine fuel for transfer to various oil storage tanks with the tanks located over three hundred meters away, which were ten meters high.
What is Unloading Marine Fuel Pumps?
Unloading marine pumps are designed to transfer liquid cargo from vessels and tankers in the shortest possible time.
Oil and fuel cargo is typically transported by vessels as it is the most cost-effective form of transportation for bulk cargo, which is only surpassed by pipelines due to it reducing double handling.
Tell-Tale Signs of an Undersized Pump
After discussions with the customer, we identified several tell-tale signs that their marine pump was undersized:
· Their screw pump which tended to be quiet, was producing high levels of noise
· There seemed to be aeration of the pumped fluid which was detected by their Coriolis flow meter
· The Flow rate was less than what the unit was designed for which could not be improved by increasing the unit speed
· Flow was turbulent, meaning there was the potential for inconsistent metering of unloaded fuel
All symptoms of what happens when a pump is undersized. Furthermore, when the vessel used a pump onboard to boost flow, the issues disappeared.
A Typical Fuel Unloading ProcedureVessel moored in port unloading fuel
During fuel unloading, a vessel will pull alongside the pump house and is held in place by guide ropes against the dock and its anchor. The photos in this article show one of the vessels moored in port with ropes and the ship anchor securing the vessel in place, with a hose extending towards the pump house.
To enable offloading to begin, a large diameter flexible hose (typically 6") is connected from the vessel to the pump house, with the hose supported by buoys in the water to ensure it remains afloat. Using a flexible hose ensures pipework is not placed under strain, or likely to break as the vessel bobs in the ocean with waves, or tides.
The flexible hose is then connected to fixed pipework onshore ready for fuel transfer to begin, once the installation has been grounded to prevent the buildup of static.
Once the discharge line is connected from the vessel, the tank valve onboard and pump are opened. The unit is started up slowly, enabling it to prime and fill with liquid before speed is increased. There are usually controls in place to enable the filling of separate tanks as commonly one pump may be used to feed several tanks and in our customer's installation there were a total of four 800M³H LFO storage tanks.
Ships do not always dock to offload fuel cargo, alternatively, ships can offload to Offshore Mooring Buoys (CALM Buoys) or Single Point Mooring Systems (SPM’s) which enables a vessel to discharge liquid cargo without docking. The benefits of this are port congestion is reduced and pilots are not requireed to board to guide vessels. Furthermore, it allows deliveries to be undertaken to shallow draft ports by larger vessels which would otherwise be unable to be accommodated or in ports where ice formation may occur.
Unloading Marine Pump Design
Unloading pumps are typically designed to produce high flows at low to medium pressures which are usually self-priming to ensure they can completely empty and strip a vessel’s cargo. Also known as stripping pumps, they enable the complete discharging of fluid from tanks without manual intervention or residue remaining in holds.
They are designed to accommodate a wide variety of viscosities to ensure they can transfer a range of marine fuel oil derivatives from the light distillate, medium, and heavy fuel oils without issue.
Pumps handling hazardous flammable substances are ATEX rated to ensure any source of ignition is removed, and should the pump produce a spark it is self-contained within the unit. They may also have a motor suitable for inverter operation which allows operators to control oil transfer rates when oil viscosity and source tank levels change.
Units can often be heat traced as a way of maintaining a fluid’s viscosity and flow rate or to prevent solidification within the pump head, with similar pumps also used in fuel bunkering and debunking operations.
Our Solution
The customer wanted three key features:
· A flow rate of 100M³H to 150M³H when pumping oil derivatives
· To draw fluid from barges with the pump located over 50M away
· Completely strip tanks without manual intervention, whilst varying flow as required to pump to tanks located over 300M away
For this we selected the NRPZ Self Priming Horizontal Triple Screw Pump, complete with an ATEX-rated motor suitable for the operation via Variable Frequency Drive (VFD).
Although pumps can typically only prime a maximum of 9.8M (based on water), and even though the suction pipework extended to over 50M away, in this particular application it was well within the capability of the design.
That is because most of the pipework runs horizontally, rather than vertically but care still needs to be taken to ensure that with the fluids viscosity, pipework diameter, and any vertical pipework sections do not amount to a pressure loss high enough to stop the unit functioning as it should.
The pump will produce varying flows up to 116M³H and can be controlled via a Variable Frequency Drive and deliver pressures up to 8 Bar. Coupled to a 45KW ATEX WEG motor suitable for operation via VFD the unit was assembled with 6” inlet and Outlet matching the customers’ existing pipework.
The new unit will significantly speed up vessel unloading and enable the customer to have greater control over their process, with the issues experienced by the current unit, such as noise, and low flow rate also resolved.
If you are experiencing low flows, slow tanker offloading/loading or simply have a unit approaching the end of its useful life and want to see if process improvements can be made - speak to us to see how we can help.
For more information on Unloading Marine Fuel – Case Study talk to North Ridge Pumps Ltd
Enquire Now
List your company on FindTheNeedle.