
Sign In
Focus on Metal Surface Treatments
30-04-2019
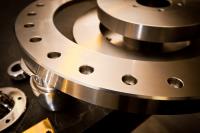
NovaCast routinely uses a wide range of metal surface treatments on its cast products to enhance their mechanical, electrical or aesthetic properties. Surface treatments and finishes are often applied following surface preparation, usually in the form of fettling, linishing or shot blasting, and any final machining.
Here, we focus on the surface treatments most commonly applied to components leaving NovaCast’s foundry.
Electroplating – This process is used to form a thin metallic coating on the component. A positively charged electrical current is passed through a solution containing dissolved metal ions while a negatively charged electrical current passes through the cast component. The result is a thin metallic coating on the surface of the component. Electroplating can be used to coat components with a variety of metals including cadmium, chromium, copper, gold, nickel, silver, tin, and zinc. In fact, almost any base metal that conducts electricity can be electroplated to enhance its performance.
Electroless Plating – This treatment, which is also known as chemical or auto-catalytic plating, achieves a similar result to electroplating although it does not involve the use of electricity. Instead, several simultaneous chemical reactions take place within the surrounding plating solution. This method of plating, which deposits an even coating regardless of component geometry, is used to protect against corrosion and wear.
Chemical Treatment – This process creates a thin film of sulphide and oxide by chemical reaction. Chemical treatment is often used for metal colouring, corrosion protection, and priming of surfaces to be painted. Passivation is a chemical process used to help prevent rusting of stainless steels by removing free iron from the surface of the component. This is typically done using nitric or citric acid which creates an inert, protective oxide layer that resists corrosion. Another process often to treat Aluminium is Alocrom, which is a chromate conversion coating. This provides corrosion protection and is also applied prior to painting or powder coating or when protection and/or electrical conductivity is required.
Anodic Oxidation – Often used to treat light metals such as aluminium and titanium, this electrochemical process produces an oxide film on metal surfaces that enhances corrosion and wear resistance. The oxide film is formed by electrolysis and is often used to add colour to metal components to improve their aesthetics. NovaCast can provide both chromic and sulfuric anodization.
Hot Dipping – This process requires the part to be dipped into dissolved tin, lead, zinc, aluminium, or solder to form a surface metallic film. One of the most commonly used corrosion resistance options for extreme environments is hot-dip galvanizing which is the process of dipping steel into a vessel containing molten zinc.
Vacuum Plating – Vacuum vapor deposition, sputtering, ion plating, ion nitriding and ion implantation are some of the more common metal surface finishing processes utilizing a high vacuum as part of the plating process. Ionized metals, oxides, and nitrides are created in a controlled environment. The part is transferred into the vacuum chamber and the metals are very accurately deposited onto the substrate. Titanium Nitride is a surface treatment that extends the life of high steel and carbide metal cutting tools.
Painting – Surface painting is commonly specified by engineers to enhance a part’s appearance and corrosion resistance. Spray painting, electrostatic painting, dipping, brushing and powder coating are some of the most common techniques used to apply paint to the surface of a component. There are many types of paint formulations to protect metal parts in a wide range of physical environments.
Thermal Spraying – This type of surface treatment involves melted or heated materials that are sprayed onto a cleaned and prepared surface where the small softened particles adhere to form a continuous coating. This primarily mechanical bonding process imparts virtually no heat to the substrate but can protect against wear, erosion, cavitation, corrosion, abrasion or heat. It is also used to provide electrical conductivity or insulation, lubricity, high or low friction, sacrificial wear, chemical resistance and many other desirable surface properties.
These are just some of the more common metal surface treatments and processes that NovaCast has used to improve or modify the characteristics of metallic parts. For more information or to discuss your particular requirements please contact our technical sales team on +44 (0) 1225 707466, send us a message or email sales@novacast.co.uk
For more information on Focus on Metal Surface Treatments talk to Novacast Limited
Enquire Now
List your company on FindTheNeedle.