
Sign In
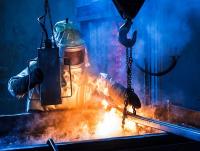
As any Design Engineer involved in the design for cast metal components will know, the selection of the metal alloy and casting process they will specify can be a complex process. Ultimately, for the Design Engineer, the specification must take account of parameters such as weight, yield strength, toughness, ductility, weldability, elasticity, shear, and thermal expansion, as well as physical dimensions, complexity of the casting geometry, cost, etc. Adding to this complexity, however, is the fact that the selection of casting process and the metal alloy selected can influence each other, and in turn, affect the other parameters in the design process.
Perhaps one of the more obvious decisions relates to the selection of ferrous or non-ferrous alloy. The characteristics and attributes that each category of alloy possess tends to over-ride the fact that alloys from each category can deliver comparable performance. Aluminium, for example, can match many of the performance characteristics as Stainless Steel but, in the absence of other contrary factors, is more expensive. Aluminium, however, would always be selected in preference to Stainless Steel where weight is a deciding factor, such as in the aerospace industry.
A brief explanation of the terms used:
Metals and alloys have several properties which have specific meanings, but which are often understood in colloquial language to mean the same thing, these include: hardness, toughness, yield strength, tensile strength, ductility, fatigue strength, plasticity, malleability, and creep:
Hardness is the material’s ability to withstand friction and abrasion.
Toughness is difficult to define but generally is the ability to absorb energy without fracturing or rupturing. It is also defined as a material’s resistance to fracture when stressed. It is usually measured in foot lbs. per sq. in or Joules per sq. centimetre. It is important to distinguish this from hardness as a material that severely deforms without breaking, could be considered extremely tough, but not hard.
Yield strength is a measurement of the force required to start the deformation of the material (i.e. bending or warping).
Tensile strength is a measurement of the force required to break the material.
Ductility is the “Degree” to which the material can be stretched or compressed before it breaks. It is expressed as a percent of the length being tested and is between the tensile strength and yield strength (i.e. what percent does the material bend before breaking).
Plasticity also known as plastic deformation, is the ability of a solid material to undergo permanent deformation; a non-reversible change of shape in response to applied forces.
Fatigue strength is the ability of a material to resist fatigue failure.
Malleability is the property of a metal that allows it to deform under compression.
Creep (sometimes called cold flow) is the tendency of a solid material to move slowly or deform permanently under the influence of persistent mechanical stresses.
So, what are the main differentiating factors between ferrous and non-ferrous alloys, and how do these affect the casting processes involved?
Ferrous Metals
Ferrous metals are any metals or alloys that contain Iron. By volume, ferrous metals, such as Iron and Steel, make up over 90% of worldwide production of metals.
Much of the reason for this popularity relates to its inherent characteristics. Iron is freely available and, therefore, relatively inexpensive. It is easy to refine, magnetic, dense and has good compressive properties. It does, however, rust readily and can be brittle. Over the years many alloys of Iron have been created, with alloying elements added in different ratios which modify, mitigate, or eliminate these negative characteristics.
Cast Iron
Cast Irons are a category of Iron alloys and have a Carbon content greater than 2% and have the benefit of high “flowability” at temperatures that are higher than typically found in non-ferrous alloys but lower than Steel. This makes them well suited to complex castings where there is a need to flow molten metal into intricate moulds. They also have the benefit that they shrink considerably less that Steel when cooling. Although Cast Irons have good compressive strength, they are brittle and will readily fracture rather than bend.
Gray Iron, which has Graphite as the Carbon additive, is the most common type of Cast Iron. Its Carbon content is between 2.5 and 4% and it also contains between 1 and 3% Silicon, which stabilises the Graphite. Graphite is used as the Carbon additive because it makes the Cast Iron somewhat less brittle and makes machining easier.
If higher impact resistance and tensile strength are required while maintaining the other attributes of a Cast Iron, then Ductile Iron would be a better choice. The Iron is alloyed with 3.2 to 3.6% by weight of Carbon plus Silicon and other elements. In this case, however, the Carbon is in the form of spheroidal Graphite, which is the element that delivers the improved strength and impact resistance.
Steel
Steel is primarily an alloy of Iron and Carbon, together with a range of other elements that give alloy variants specific properties, such as the addition of Chromium to create corrosion-resistant Stainless Steel. The main difference between cast Irons and cast Steels is that cast Steel will generally have a Carbon content of less than 2.14% by weight. During production, Steel is quenched rapidly, which traps Carbon atoms within the Iron crystalline lattice. This distorts the lattice, and it is this distortion that hardens the Steel alloy.
Cast Steel alloys do, therefore, have stronger mechanical properties than cast Irons but this comes at the expense of ‘flowability’. Molten Steel needs to be much hotter than molten Iron to flow into detailed moulds. These higher working temperatures are much more difficult to manage, more labour-intensive, and therefore, more expensive. Despite these issues, the higher mechanical strength inherent in Steel castings can make this a clear choice.
Non-Ferrous Metals
Non-Ferrous metals and alloys are those that do not contain Iron. Common examples of non-ferrous metals include Aluminium, Copper, and its alloys (Bronze and Brass), Nickel, Palladium, Titanium, Tin, Lead, Zinc, and the precious metals, such as Gold, Silver and Platinum. These metals, and alloys of them, tend to be more expensive that Iron derivatives, so even though non-ferrous alloys can provide comparable mechanical properties to Iron and Steel, they would rarely be an option in the absence of other defining requirements, such as weight.
Aluminium
Aluminium is one of the most widely used non-ferrous metals. It has the advantage over many cast Irons and Steels in that it combines lightness with strength, it has a lower melting point, and it is corrosion resistant. This combination of factors makes Aluminium easier to cast than Steel, which brings down the foundry costs, but it is a more expensive metal that Iron. This can limit its applications compared to Iron and Steel unless its other attributes are significant.
Bronze and Brass Alloys
These are alloys of Copper and were the first metals cast by humans. Brasses are copper-based alloys that have zinc as the principal alloying element. In some cases, small amounts of Nickel, Aluminium, Iron, or Silicon may be also present. Bronze is an alloy consisting primarily of copper, commonly with about 12–12.5% tin and often with the addition of other metals (such as Aluminium, Manganese, Nickel or Zinc).
Their much lower melting point than ferrous metals, combined with ability to cast detail well and their inherent corrosion-resistance, even in salt water, make them valuable alloys to this day. They are softer than ferrous alloys but have natural resistance to ‘galling’ (wear of metal against itself). This combination of attributes makes them well suited to marine applications, such as deck fittings and propellors, for pump impellers, bearings, and zippers, and as fittings used in the water industry.
Specification of metals and alloys for casting
The selection of the most appropriate metal for any component will depend on a variety of considerations ranging from the mechanical requirements and weight to casting options, aesthetics, and cost. At NovaCast, we have a UK-based non-ferrous foundry together with partner ferrous and non-ferrous foundries in the Far East that we have worked with for many years. We have broad experience of working with design engineers to specify the most appropriate alloy selection for each project – whether the solution turns out to be ferrous or non-ferrous.
For help and advice or to discuss your requirements, call a member of NovaCast’s team on +44 (0) 1225 707466, send us a message here or email sales@novacast.co.uk.
For more information on NovaCast: A single-source solution for both ferrous and non-ferrous castings talk to Novacast Limited
Enquire Now
List your company on FindTheNeedle.