
Sign In
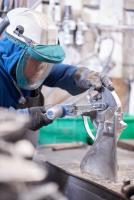
As part of our series of articles discussing various aspects of Gravity Die Casting, we are taking a look at the importance of parting line design. The parting line is where two or more sections of the Die split to release the casting. When deciding where to place the parting line, designers will need to consider many factors and calling on the expertise of foundry engineers at an early stage will help inform these decisions. As a general rule, however, the straighter the parting line is the lower the die tooling cost will be.
So, what are the factors that designers should be considering? The following are the most important:
Product specification: Different casting techniques produce different as-cast surface finishes. Although gravity die casting can deliver excellent and consistent surface finishes, the parting line surface is usually compromised – particularly as gates and vents are positioned along the line and these will be visible. Either further machining is required, or the customer must accept the existence of the visible line.
Machining: Machining may be required to improve the aesthetics of the cast component but designers should also be aware of the tolerances required in different areas of the casting. Where critical tolerances exist, these areas should be positioned away from the casting line where possible to reduce machining costs.
Metal flow: The positioning of the gate inlet, where molten metal is poured into the die, is critical in ensuring that metal flows through the die in a way that minimises potential casting defects. The gate inlet must be placed on the parting line, so the casting geometry and metal flow characteristics will be a factor in deciding where the parting line needs to be.
Internal Cores: Internal cores are placed within the die to create voids and internal cavities within the cast component. These can form critical internal structures or be used to reduce weight and manage metal flow characteristics, including solidification profiles. The positioning of these cores will influence the position of the parting line.
Ejector pins: With simple gravity die cast components, ejector pins may not be required. As the size and complexity of the casting geometry increases, however, ejector pins may be required to help in removing the casting from the die. The parting line location can have an impact on the force required and, therefore, the number and location of ejector pins required. Each of the ejector pins will leave a surface defect on the component so consideration should be given to their positioning from an aesthetic point-of-view.
Die costs: In most cases, a straight parting line design will lower the cost of tooling. This will not always be the case, however, as the component geometry may introduce other elements, such as side die pulls, that would make a broken parting line more economical.
As is usually the case with metal casting, many often conflicting factors must be considered when developing the optimum casting geometry design. When gravity die casting is the casting method selected, the tooling costs for producing the die can be a significant factor. So, working with your foundry engineers at an early stage can help optimise the balance between product specification, initial set-up costs and the ongoing production efficiencies that this casting process can deliver.
For advice, a competitive quote or just to discuss your requirements, call a member of NovaCast’s team on +44 (0) 1225 707466, send us a message here or email sales@novacast.co.uk.
For more information on The Importance of Parting Line Design in Gravity Die Cast Components talk to Novacast Limited
Enquire Now
List your company on FindTheNeedle.