
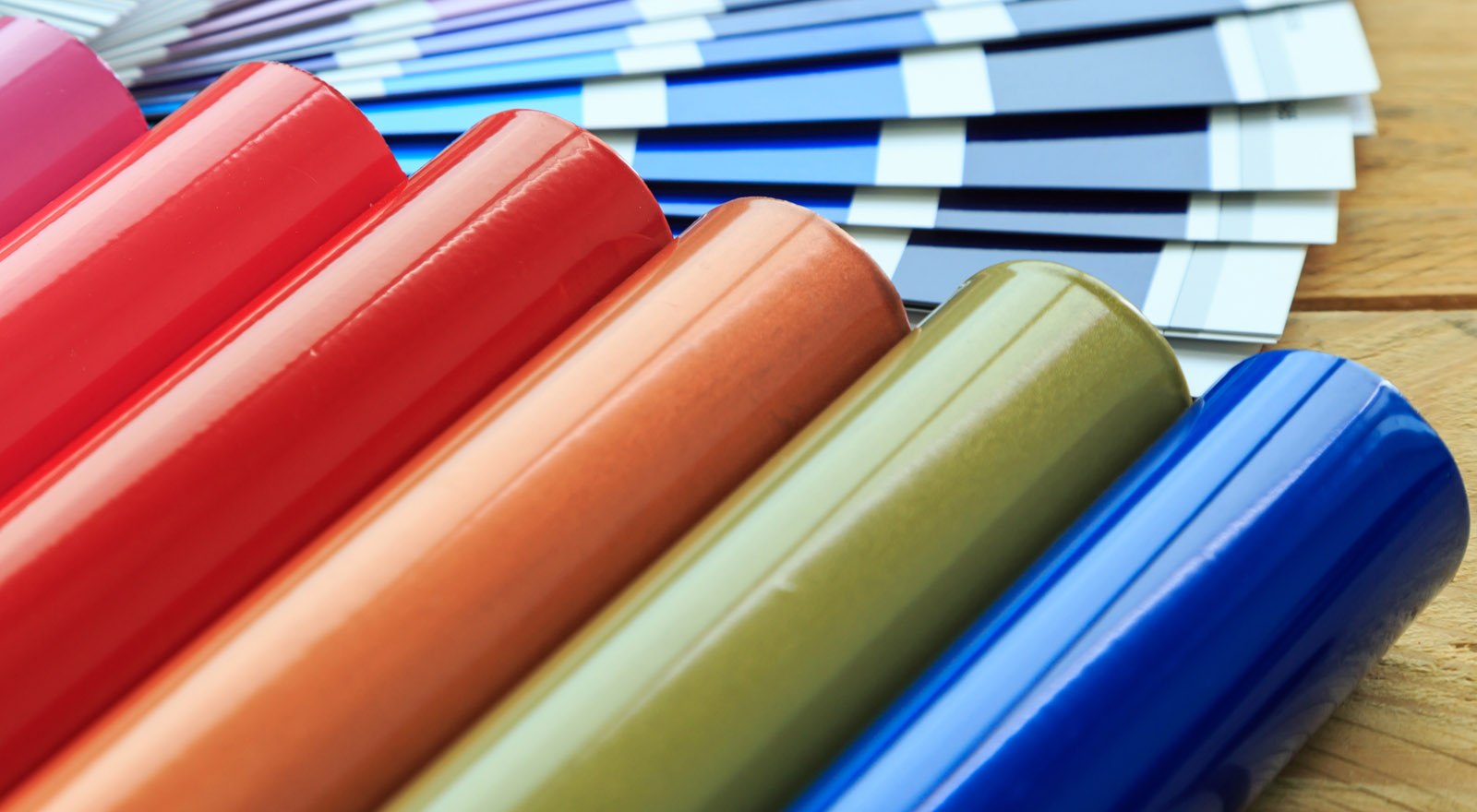
Is Bright Dip Anodising a Good Choice for Your Extrusions?
Extruded aluminium anodising is an important process that ensures the longevity of an extrusion. An anodised surface has a much more durable finish than bare metal, which means it will last longer. When considering an anodising solution for your extruded aluminium parts, you should consider Bright Dip Anodising. Read on to find out why this method may be best for you!
Bright dip anodising is one of many types of anodic finishes available in today’s market. It is particularly popular among manufacturers who make extruded aluminium products because it can accommodate large batches with minimal downtime and produce high-quality results every time.
The anodising process begins by submerging the aluminium parts in a tank of hot sulfuric acid. This etches the surface and opens up pores, which will then be filled with an anodic coating. The parts are then rinsed and placed in a tank of boiling water to set the coating. At this point, they are ready for the bright dip anodising process.
In a bright dip anodising tank, the parts are dipped in a vat of dye. The dye will adhere to the anodic coating and produce a vibrant finish. After the parts are removed from the vat, they are rinsed again and dried.
The benefits of using bright dip anodizing include:
– Increased durability – an anodised surface is much more durable than a bare metal surface and can withstand wear and tear better
– Vibrant colours – the dye will adhere to the anodic coating and produce a vibrant finish that is sure to stand out
– Minimal downtime – bright dip anodising can accommodate large batches with minimal downtime
– Consistent results – the process is highly repeatable and produces high-quality results every time.
If you are looking for an anodizing solution that will produce a vibrant, durable finish, then bright dip anodising may be right for you! Contact us at Orgbar today to learn more.
For more information on Dip Anodising talk to Orgbar Aluminium Limited