
Sign In
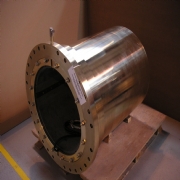
With the development of direct electric motor propulsion on naval and commercial vessels the selection of bearing materials is more critical
Conventional water lubricated bearing systems use composite, elastomeric polymer or elastomer bearings with machined grooves to allow water to flow through the bearing.
This is to remove the frictional heat generated when the shaft is rotating at a low velocity and to give sufficient water to allow the shaft to be separated on a water film at high velocities.
Most bearing materials will operate at high velocities if the bearings are designed with the correct clearance and alignment. This is from the hydrodynamic separation of shaft and bearing generated from the water wedge.
At low shaft velocities the shaft and bearing operate in the boundary conditions where the bearing material is in contact with the shaft allowing abrasive and adhesive wear to occur.
This condition requires a material with low wear properties and low abrasive wear on the shaft/shaft liner and which exhibits low friction.
In conjunction with the UK Ministry of Defence TRELLEBORG SEALING SOLUTIONS embarked on an extensive test programme to evaluate a combined composite material Orkot ®TXMM for this exacting application.
The requirements were velocities down to 5 Metres / Minute , Pressures to 6 Bar and water flows down to 2 litres per minute in the extreme case.
The seawater contained Silica flour at 250 PPM
Operating on an LG4 Bronze sleeve the 200mm diameter bearing was subjected to 2000 hours operation.
The overall wear equated to 0.027 mm / 1000 hours and the shaft wear was minimal with an improved shaft finish.
The tests were repeated with Inconel and Nickel Chrome Boron coated shafts
It is important to note that a water lubricated bearing requires bedding in to achieve the optimum running conditions; some bearing materials have stringent conditions for this. As this is not acceptable for Naval refits a bearing material must cope with this without damaging either the bearing or liner, Orkot® TXMM has a low friction, low wear surface which contains substantial friction reducing material contained within the surface structure to cope with this.
The material was selected for the shaft bearings for the Royal Navy T45 Destroyer and the new CVF Carrier as both of these vessels have electric propulsion.
An additional requirement for these vessels was the ability to remove the bearing segments without dry-docking the vessel, normally the shaft bearings require fitting into a removable bronze sleeve before assembly into the bearing housing.
This is not possible without dry-docking the vessel so an alternative design was required.
The solution was to fit a bronze housing into the strut housing which would not require removal on refit. The bearing segments were pre-fitted in our factory so that they could be fitted directly into the housing using a patented locking key.
The bearing water grooves are the two groove design with the grooves at 3 and 9 o’clock forming a 140° bearing support area to give optimum hydrodynamic operation.
Because of the shaft geometry it was necessary to calculate the shaft pressure on the bearing at the static and full speed conditions.
The bearing was machined with a small conical angle at the aft end to allow the bearing to deform elastically at the intersection angle to reduce the maximum pressure when moving from static to full speed conditions.
As the segments are factory fitted using an identical key no adjustment is necessary when re-fitting and a simple assembly tool is used to close the key. A further simplification was to fit the removable wear gauge in the bronze housing flange negating the requirement to drill the bearing in situ.
All these design features make Orkot® TXMM the natural choice for water lubricated stern shaft bearings for low speed running.
For more information on Developments in water lubricated bearings for low speed operation talk to Trelleborg
Enquire Now
List your company on FindTheNeedle.