
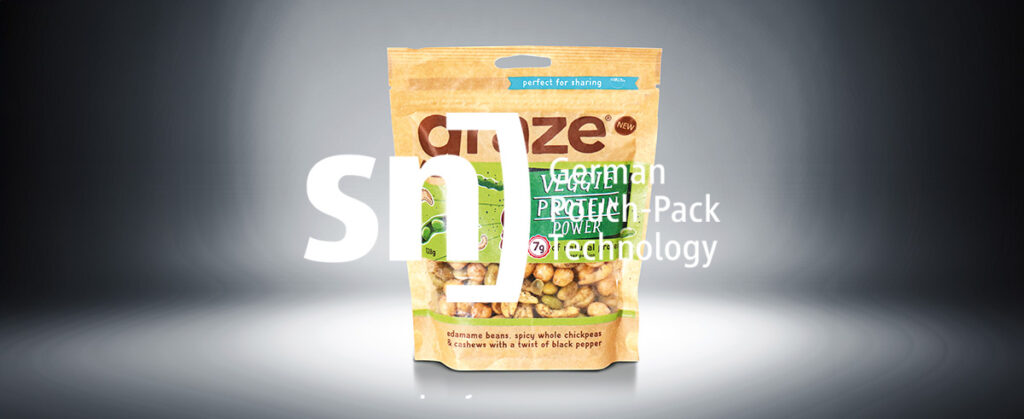
The task:
A UK market leader for nuts and dried fruits would like to bring out selected specialties to the best point-of-sale. The products are considered healthy snacks for in-between meals and should be sold in appealing stand-up pouches with resealable press-to-close zipper. Great fexibility regarding pouch sizes, product variety and quantity must be guaranteed as well as the inclusion of hygiene and special occupational safety and health regulations.
The SN solution:
The horizontal working FM 060 series form, fill and seal pouch machine is tailor designed and constructed for the customer. From the SN auto-splicer, via the thermal transfer printer used in the continuous part of the machine, the digital displays for side seal position and pressure, right through to the easy swivel top seal mechanism: all components are precisely aligned to the needs of the customers. These are quick and easy pouch size change and – as on all SN packaging machines – a very good cleaning possibility are incorporated.
Details:
The SN developed auto-splicer reduces the film change to a minimum and material usage. The new film roll is prepared on the cutting and gluing table of the splicer and automatically inserted into the machine as soon as the material of the current reel runs out. The pouch with the splice is detected on the Rotary turret and rejected. The machine continues to work when changing film thanks to the built-in film buffer at full speed, resulting in maximum effciency of the line. The space saving thermal transfer printer positioned at the folding plow transfers the required information (e.g. the expiry date of the product) in the gusset of the pouch. The zipper is inserted into the pouch and film further advanced to the seal stations.
The fine adjustment of the seal position can be done on the fly and can be visualized by means of a digital display. The sealing jaw pressure gauges are also equipped with digital displays and ensure the accurate reproduction of the seal pressure on the film at machine speed. The high performance heat sealing jaws, made of a special alloy, ensure the perfect temperature distribution across the entire seal surface via sophisticated electronics, even at maximum production speed. The side seal is immediately cooled after sealing and the euro hang hole, as well as the tear notches are punched out. The film is then cut into individual pouches and transferred into the 8 station rotary turret.
Special features of the rotary turret:
- Sensor for the correct position of the pouches in the gripper
- Electronically controlled flow meter for the nitrogen gas flushing (parameters can be saved in recipe management and easily recalled)
- Top seal monitoring for the detection of foreign objects in the top seal and rejection of the identifed pouch
- Exhaust unit on the top seal cleans the sealing jaws between each sealing
- Easy-swivel top seal unit for easy cleaning of the sealing jaws
- Automatic rejection of faulty pouches
Contact us on 01473 893990 or at email@penn-packaging.co.uk or click here for more information.
For more information on Penn Packaging > SN: Pouch project example: Snacks in stand-up pouches with zipper talk to Penn Packaging Limited