
Sign In
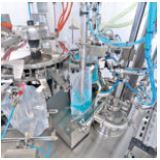
The task: A Scandinavian producer seeks to fill three liters of screen wash. The packaging shall be user-friendly
(light weight, easy handling, little waste) and inexpensive to produce. In addition, the easily inflammable content
must be packed securely and well presentable in store.
The solution: A pre-made pouch with corner spout and carrying handle is flled and sealed on our horizontal rotary
pouch fller FS 830 with servo-driven pump. The laminate has to withstand both the heavy weight and the ethanolcontaining
product.
For this project the FS 830 was equipped with a few new technical developments. The main focuses were:
safe production
high production rate
little foam generation
In order to meet these requirements SN developed the following solutions:
special pouch opening
double-filling
ideal size of the filling heads
removing foam remains by suction air
After entering the horizontal rotary pouch filler the pouch is pulled and held open completely by means of suction
cups on the upper and lower part of the pouch and two inserting, synchronized swivels.
In order to meet the requirements of this special product and output rate the filling process is divided between two
machine stations. A servo-driven filling head is inserted rapidly into the pouch, lifted up slowly during the filling
process (1,5 liters) and finally, when the pouch is filled to its half, removed again quickly. This process is repeated at
the next station where the pouch receives the second 1,5 liters in the same way.
The advantage of this technical development: the foam building of the product is reduced to a minimum.
Finally, the little remaining foam and air are sucked off (optimizing the pouch volume). The fawless seal is created by
a thermic double-seal during which the filled pouch is supported mechanically. At the final of the eight stations of this
rotary table the head-seal is cooled and the pouch transferred to the outlet conveyor belt.
In order to meet the requirements of a product containing ethanol, the machine was built in accordance to ATEX
guidelines and is TÜV certified. Prerequisites for this certifcation were, for example, the stainless steel execution
(wet cleaning) with circumferential gutter as well as an ethanol-exhaust and gas detectors which are placed above
and below the machine table.
The FS 830 is suitable for pouch sizes up to 300 x 420 mm. Thanks to tool-free format change-overs, product
change times below 15 minutes can be realized. The setting of the formats is furthermore simplifed by mounted
scales. Via integrated recipe control all format-depending parameters can be saved and recalled through the SN
Smart-Touch operator panel.
For more information on SN Innovative solutions: Product example – Screen wash talk to Penn Packaging Limited
Enquire Now
More News
List your company on FindTheNeedle.