
Sign In
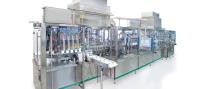
Besides precise filling and high speed the sterility and storage life are the major challenges when filling fresh, liquid dairy products into pouches. By integrating the ULTRA-CLEAN technology into the multi-station machines LMS 120 LP and LMS 124 LP SN tackles this challenge with German efficiency.
An automatic hydrogen-peroxide sterilization is integrated in the pouch making process which ensures sterility of the film and spouts. In combination with clean-room technology and a secured coldchain the filling goods last 40-60 days.
Furthermore, a camera system monitors the exact positioning of the spouts with a precision of 0,1 mm which makes further costly and personnel-intensive quality controls redundant.
Newly developed cutting tools allow for a smooth pouch without ridges reducing the risk of injury for the customer (children) to a minimum. At the same time damages during transport and storage caused by a pouch are eliminated.
All standard pouch formats and contents between 70 ml and 350 ml can be produced on the LMS 120 LP and LMS 124 LP machines. Both machines are CIP and SIP compatible. All machine parts, including the filling area, can be cleaned and sterilized without dismantling. The SN ULTRA-CLEAN technology meets all international requirements for clean filling of fresh, liquid dairy products into pouches and is acknowledged and certified by FDA, USDA and 3A Dairy. Format change overs are easily and quickly done by exchanging complete building groups and by using central adjustments
For more information on Ultra Clean Packaging of fresh liquid Dairy Products talk to Penn Packaging Limited
Enquire Now
More News
List your company on FindTheNeedle.