
What is Plastic Extrusion? A Complete Guide
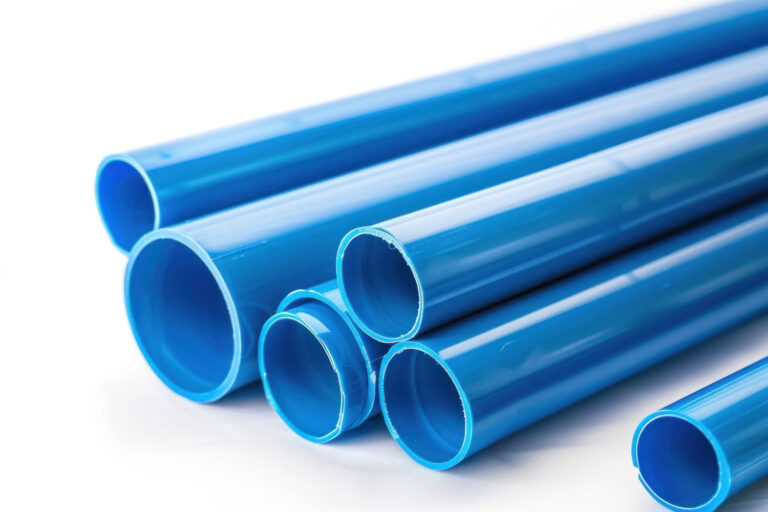
Overview
Plastic extrusion is a manufacturing process used to shape plastic materials into continuous profiles like pipes, tubes, films, and sheets. This versatile method is key in producing a wide range of products used across industries, from packaging to automotive. It’s popular because it allows for high-volume, cost-effective production with flexibility in design.
If you’re looking to find the best suppliers for plastic extrusion in the UK and Ireland, PlastikCity can help you compare quotes from trusted providers. Visit the PlastikCity plastic extrusion category to find and connect with the right partner for your project.
Let’s dive into how plastic extrusion works, the equipment used, different types of extrusion processes, and the advantages and limitations of this manufacturing method.
The Plastic Extrusion Process Explained
Plastic extrusion is a continuous, straightforward process involving several key stages, each ensuring that the raw plastic material is melted, shaped, and cooled into the desired form. Here’s a step-by-step breakdown:
Material Feeding – The extrusion process begins with raw plastic, usually in the form of small pellets or granules. These pellets are placed into a hopper, a funnel-like container on top of the extruder, which gradually releases the plastic into the machine. From the hopper, the plastic enters the feed throat and moves into the barrel, where it meets the screw.
Melting and Compression – Inside the barrel, the plastic is moved forward by a rotating screw. This screw is precisely designed to push the plastic along while gradually compressing it. Alongside this, heaters positioned at different points along the barrel raise the temperature, causing the plastic to melt smoothly as it progresses. The screw’s rotation, combined with the heat, ensures the plastic melts evenly without overheating. Each barrel section typically has separate heating controls, creating a “temperature profile” that steadily increases from the rear to the front, preventing any material degradation.
Filtration and Back Pressure – As the melted plastic nears the end of the barrel, it reaches a breaker plate and screen pack. This pack filters out any contaminants or unwanted particles from the molten material, keeping the plastic pure before it moves into the die. The breaker plate also generates “back pressure,” which improves the consistency of the melt and helps mix the plastic thoroughly for a uniform texture.
Shaping with the Die
Once filtered, the molten plastic moves into the die, a custom-made tool that gives the plastic its final shape. Dies can be tailored to create a wide range of profiles, from simple tubes to complex, multi-layered products. As the molten plastic flows through the die, it takes on the specific cross-sectional shape desired for the final product. Because the flow must be even, die design is carefully calibrated to prevent warping and uneven thickness, which could compromise the product.
Cooling and Solidification
After shaping, the extruded plastic is still hot and needs to be cooled quickly to retain its shape. This is often done by passing the extruded profile through a water bath, especially for products like pipes and tubes. In some cases, cooling rolls or fans may be used instead, particularly for thinner sheets or films. Cooling is a critical step, as plastics are slow to release heat. For certain products, a vacuum can be applied during cooling to prevent deformation.
Post-Processing (Optional)
Depending on the application, some extruded products undergo additional processing steps, such as cutting, coiling, or assembly. For example, tubing might be cut to specific lengths or wound onto reels for storage and transportation, while films could be printed or laminated for enhanced performance.
This multi-stage process is highly effective for creating a variety of products continuously. It’s particularly well-suited for high-volume production, allowing manufacturers to create everything from durable piping to flexible films without interruptions.
Components of a Plastic Extruder
Here are the main parts of an extruder and their roles:
Hopper and Feed Throat
The hopper funnels plastic pellets into the extruder. These pellets pass through the feed throat, entering the barrel to be heated and shaped.
Barrel and Screw
Inside the barrel, a rotating screw moves the plastic forward while heaters melt it. The screw helps compress and mix the plastic for a uniform melt.
Breaker Plate and Screen Pack
A screen pack filters out contaminants from the molten plastic before it reaches the die. The breaker plate supports the screens, ensuring even melting and back pressure.
Die and Cooling System
The die gives the extruded plastic its final shape. Once shaped, the plastic is cooled to harden it, usually in a water bath or with cooling rolls.
Types of Plastic Extrusion Processes
Plastic extrusion offers flexibility through various process types, each tailored to create specific products or profiles. Let’s look at the main types:
Tubing Extrusion
Tubing extrusion is used to create hollow products like pipes, tubes, and straws. In this process, a pin or mandrel is placed inside the die to shape the internal cavity of the extrudate. As the plastic flows through the die, the mandrel forms the hollow centre. Positive air pressure can be applied to prevent collapse and help form the desired wall thickness. After exiting the die, the tube is pulled into a cooling tank, often using a vacuum to maintain the shape and dimensions. Tubing extrusion is popular for products in plumbing, automotive, and medical applications, such as irrigation pipes and medical catheters.
Blow Film Extrusion
Blow film extrusion is commonly used to produce thin, flexible plastic films. In this process, a ring-shaped die is used to extrude the plastic into a tube. Compressed air is then blown into the centre of the tube, expanding it into a large “bubble.” The bubble stretches the plastic in both directions, producing a film with increased strength and flexibility. This film is then cooled and flattened by nip rollers before being wound onto rolls. Blow film extrusion is widely used to manufacture packaging materials, like shopping bags, food packaging, and shrink wraps.
Sheet and Film Extrusion
In sheet and film extrusion, a flat die is used to create broad sheets or thin films that are too thick to be formed by the blow film method. As the molten plastic exits the die, it passes through a series of cooling rollers to achieve the desired thickness and surface texture. These rollers can also control the sheet’s gloss level. Sheet extrusion is commonly used to produce plastic sheets for signage, packaging, and automotive applications, as well as films used in construction and food packaging. It’s an effective way to create uniform, flat plastic materials for a variety of applications.
Over-Jacketing Extrusion
Over-jacketing extrusion, also known as wire coating, is used to insulate and protect wires or cables. In this process, the plastic material is extruded around a wire or cable, which is pulled through the centre of the die. If adhesion between the plastic and the wire is required, pressure tooling is used to ensure a strong bond. For less critical applications, jacketing tooling is used, allowing the plastic to form around the wire without direct pressure. This type of extrusion is essential for manufacturing insulated cables used in telecommunications, power distribution, and automotive wiring.
Coextrusion
Coextrusion is a process that combines multiple layers of plastic into a single product, each layer providing different properties. Multiple extruders feed different materials into a single die, forming distinct layers within the final extrudate. Coextrusion is often used in applications requiring specific attributes, such as strength, flexibility, and barrier properties. For instance, in food packaging, a coextruded film may combine a moisture-resistant layer, a barrier layer to keep out oxygen, and a layer for structural integrity. This technique is common in packaging, tubing, and products needing enhanced durability or specialised features.
Types of Plastic Extruders
Extruders come in two main types, each suited to different production needs:
Single-Screw Extruder
Single-screw extruders are simple and cost-effective, with a single rotating screw that melts and pushes plastic through the die. They’re ideal for basic shapes like pipes, sheets, and films, offering:
Ease of Use: Simple design makes it easy to operate and maintain.
Moderate Mixing: Works well for uniform materials but less effective for complex mixing.
Consistent Output: Ideal for standard profiles where consistent cross-sections are needed.
Twin-Screw Extruder
Twin-screw extruders feature two interlocking screws, enhancing material blending and speed. They’re perfect for more complex applications like multi-layer films and reinforced plastics, offering:
Improved Mixing: Twin screws provide excellent blending, ideal for products with multiple materials.
Higher Throughput: Faster processing makes them suitable for high-volume production.
Versatility: They handle a wide range of plastics, especially for more customised shapes or layered products.
Each type brings unique strengths, allowing manufacturers to choose the right extruder based on product complexity and production volume.
Common Extrusion Materials
Plastic extrusion supports a wide range of thermoplastics, each offering unique properties to suit different applications. While these aren’t the only materials used in extrusion, here are some of the most popular options:
PVC: Strong and weather-resistant, ideal for pipes and frames.
Polyethylene (PE): Flexible, used for packaging and tubing.
Polypropylene (PP): Heat and chemical resistant, suitable for containers and medical products.
ABS: Durable and lightweight, often used in automotive parts.
Applications of Plastic Extrusion
Plastic extrusion supports various industries, including:
Pipes and Tubing: Commonly used for plumbing, electrical conduit, and automotive parts.
Packaging: Films for food packaging, pouches, and shrink wraps.
Insulation: Wire and cable coatings for electrical safety.
Construction: Profiles for window frames, weatherproofing, and structural components.
Advantages of Plastic Extrusion
Plastic extrusion offers several benefits:
High-Volume Production: Ideal for mass production of uniform products.
Cost-Effective: The continuous process keeps costs down.
Design Versatility: Custom shapes and profiles are easy to achieve.
Material Flexibility: Compatible with a variety of plastics.
Disadvantages of Plastic Extrusion
While effective, extrusion has some limitations:
Setup Costs: Equipment and tooling can be costly.
Shape Limitations: Best for consistent cross-sections, making it harder to create complex shapes.
Material Expansion: Plastic can expand during extrusion, affecting precise measurements.
Conclusion
Plastic extrusion is an efficient, high-volume production method, widely used across multiple industries. It’s a practical choice for creating durable, consistent profiles with relatively low material costs. From pipes and tubing to packaging and insulation, plastic extrusion meets a broad spectrum of manufacturing needs.
For anyone looking to source a plastic extrusion provider, PlastikCity’s plastic extrusion category offers an easy way to find and compare top suppliers in the UK and Ireland. Submit a quote request to get started on your project today!
For more information on What is Plastic Extrusion? A Complete Guide talk to PlastikCity Ltd