
Sign In
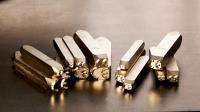
In July 2013, it became mandatory for construction products, under the Construction Products Regulation (CPR), to apply CE marking. The Directive required that CE marking should be affixed visibly, legibly and indelibly to the construction product or to a label attached to it. Where this is not possible, or not warranted on account of the nature of the product, it was required to be affixed to the packaging or to the accompanying documents. The downside of this is that once the packaging is discarded, there is no evidence that the product was CE marked.
Prior to 2013, CE marking had been a voluntary arrangement, so the EU Directive did present the construction industry with a significant challenge – that of how to integrate product marking into the manufacturing process. Some saw this as an opportunity to add further marks, such as logos and product codes, to reinforce the brand, which is possible as long as it does not interfere with the CE mark.
There are many different considerations to take into account when it comes to CE marking. Firstly, at what stage of the manufacturing process should the mark be added? For example, could it be done within one of the other manufacturing processes, such as moulding, which could save cost and time. Another consideration is where on the product the mark should be added. The guidance simply states that the mark should be clearly visible, but this is left to the discretion of the manufacturer.
As marks are expected to be of sufficient quality to last the lifetime of the product, the method of marking is extremely important. Take, for example, the window industry. PVC window manufacturers are required to mark the date and manufacturers’ name. After we carried out extensive tests with manufacturers, we found that laser marking worked best and it was suitable for use on a wide range of different PVC window products.
Other products, such as GRP doors or timber window frames, could be marked with hand stamps or type or logotypes applied by machine or hand. In the case of each different material, our technical team would carry out a test marking exercise to see if these methods were suitable.
Marking methods
There are various different marking methods that should be considered. Punch marking has the advantage of being quick, cost-effective and flexible. It is also popular as it can be used in most manufacturing environments. Another option that is worth considering is using concave roller dies for tube marking. The benefit here is that the method is very quick and relatively low cost. However, this process is suitable only for adding fixed information, as the mark is not easily changeable, so they are not suited to serialisation.
It is more cost efficient to incorporate new dies into existing machinery, as the capital outlay on the dies is significantly less than that of buying new machinery. Integrating roller dies provides consistency of depth and allows for continuous marking.
With custom built dies, they are usually used for marking fixed information, such as CE marks. However, there is the option of using composite dies, where some elements of the mark are fixed, but some are interchangeable. These are custom built to fit the requirements of an existing machine, which means there are no modifications required.
When it comes to products such as roof tiles that are made from moulds, custom-designed dies are often the best approach. Here the CE mark and identification code is added to the mould, which means that the mark does not add another manufacturing process. This is a very durable method of marking. Composite dies can be chosen and used within moulds, which require that some of the information will remain constant, but some of it can be made interchangeable, for instance, batch number/product code.
Dot marking is a popular method of marking with construction companies. The mark here is made up of a series of dots, which is a particularly ‘low stress’ method that does not have a major impact on the product surface or integrity. Dot marking is computer controlled to guarantee dot precision and we use bespoke software designed by our engineers. It is ideal not only for CE marking, but also for conveying variable information, such as batch or serialisation, as it can be set to increment after each mark or number of marks. The software also has features such as non-repetition, to ensure you cannot mark the same number twice.
If the marking technology is required for large, heavy or immobile parts, such as scaffolding, steel girders and frameworks, dot marking can be the best option as it works well as a portable unit, which can then be taken to the material to be marked. Dot marking is fully programmable, so the mark can change every time – this is ideal for use where there is serialisation or batch coding. Another popular method is scribe marking, which creates a smooth, aesthetically pleasing continuous line mark.
Laser marking is growing in popularity with building product manufacturers too, as it can be used to mark the widest range of materials. It offers great degrees of flexibility, such as varying depths and colours, making it highly suitable for logos.
With any construction product to be CE marked, or indeed with any mark, tests would need to be carried out by the marking company to ascertain the most appropriate method. With CE marking still being a relatively recent requirement, a lot of work is being done to ensure that manufacturers are able to meet the EU directive in the most effective way possible.
View the article in Building Products magazine.
- See more at: http://www.pryormarking.com/news/pryor-discusses-different-methods-of-meeting-ce-marking-requirements-in-construction#sthash.Ogk030mp.dpuf
For more information on Pryor discusses how to meet CE marking requirements in the construction industry talk to Pryor Marking Technology
Enquire Now
List your company on FindTheNeedle.