
Sign In
GAS MAIN INSTALLATION
27-08-2017
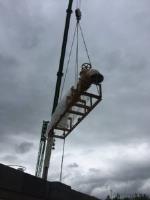
WE HAVE BEEN DESIGNING AND INSTALLING GAS MAIN AT PW MAINTENANCE FOR A NUMBER OF YEARS USING LOTS OF DIFFERENT MATERIALS SUCH AS COPPER, STAINLESS STEEL, IRON AND ALSO FULLY WELDED SOLUTIONS.
When an enquiry for a gas main lands we generally need to consider various factors before we can even begin to quote.
Fuel type – Natural Gas or LPG
How long will the gas main be
What load in Kw will be drawing from the main
Suitability of existing gas meter
Gas main run including direction changes
Connection types – Flanges, Screwed
Pressures involved within the final main
Late last year we were contracted to design and install a gas main to provide gas to a large CHP (Combined Heat And Power) Plant provided by Clarke Energy and two Gas Fired thermal oil boilers supplied by Wanson Babcock. The total combined gas use already equalled the amount of gas available on site, and all of that was being used. It quickly became apparent that a gas main upgrade was needed.
The CHP Engine alone required 645 m3/h at full operation and each oil boiler needed 325 m3/h, giving a new additional load of 1,295 m3/h of Natural Gas. Our first stop is normally to the Network where an application for additional gas is completed, then the wait begins. Almost immediately we get an independent energy company involved, Energy Assets who are able to lease with the Network on our behalf to try and speed up the paperwork and design side of things. Gas main upgrades wont happen overnight and often not in the same year.
Our worst nightmare came back for this job, where the Network wanted to run a feasibility study for 12 months, to see how this additional load might affect the existing network. A feasibility study is normally bad news, but that’s where Energy Assets comes in handy. Straight over to them and get them to work on the network. On this particular job we needed 650 m of IP (Intermediate Pressure) main installing, straight down the main road to the very end and into the IP main at the end of the estate. The final plan was to effectively parallel up the existing main to provide twice the amount of capacity to the single stream station on site. The LP network on site could already handle the demand. Energy Assets handled the network for us and designed and supplied the new gas meter. They also arranged the parallel IP main installation and the connections to the LP main on site.
We followed the proposed CAD drawings of the new plant and effectively designed the pipe run first, together with the necessary steelworks to hold the gas main in place.
The main was designed by simply working out the correct pipe size for the volume of gas then assessing pressure drop to be within 1 mBar for this particular job.
Energy Assets provided us a new gas meter with a 12″ take off and this was located in a purpose built meter room on site. The meter was craned in in sections and assembled and fixed in place. We added a 12″ cut off valve wired to the building fire alarm system, straight on the end of the meter.
The pipe continued through the wall in 12″ to a Tee, where a valve was installed and further 12″ pipework to support the CHP. You will see on the drawing how the pipe size reduces immediately on the connection flange at the CHP engine. During calculations it worked out better to increase the size of this small section of main to effectively reduce the pressure drop to almost nothing, giving a little more give for the other run to the Gas thermal oil boilers.
The feed around to the Gas thermal oil boilers worked out in 8″ with a half mBar drop. This was installed from another isolation valve on the 12″ Tee and installed around to a gas booster supplied by Wanson Babcock. Again the 8″ pipe was reduced to 4″ before connecting to the booster. Secondary pipe was completed in 4″ from the booster to each boiler.
The materials arrived on site and our coded welders fabricated most of the sections before they were installed using a crane, then bolted together when in place. Some final welds had to be completed in location with large fittings being installed using a Genie Super lift to hold them in position whilst welded. Our Gas Engineers then carried out the required Strength Test and Tightness Test before purging the main over to Gas using the appropriate equipment and handing over a bunch of certificates.
An operative then cleaned and painted the main in a coating of protective oxide then a standard coat of yellow ochre paint and finally some gas tape afterwards.
When the appliances were commissioned we had a much lower pressure drop than calculated and all the appliances functioned perfectly.
If you are looking to have a new gas main installed or need modifications carried out to an existing gas main, then please contact us to help you with your project.
We will consider any project using most material types from a small copper main all the way to a fully welded solution!
For more information on GAS MAIN INSTALLATION talk to PW Maintenance
Enquire Now
List your company on FindTheNeedle.