
Sign In
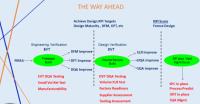
Holistic ‘is a belief that the parts of something are intimately interconnected and explicable only by reference to the whole’
The meaning of the term ‘Holistic’ is very appropriate in today’s complex Electronic and Electro Mechanical products as we cannot assume a one off Accelerated Life Test, a small sample HALT test or a suite of specified environmental tests will highlight all the major latent defects which will lead to failure at some point in the products lifetime.
There are many different methods to be employed to fully understand and predict the Quality and Reliability of a New Product, these are often interconnected and all have a part to play in planning how we can best understand and predict the product performance.
Research and Development engineers have for many years applied DFMEA techniques to try to minimise possible issues, then perform some form of product stress test or ALT to attempt to predict the expected failure level. These techniques are sound, but often produce very little meaningful output unless the design is fundamentally poor.
In fast moving consumer product manufacture there are a wide range of sources that contribute to defects which are not directly related to the original design such as;
Supply Chain Quality
Assembly Process capability
Design Quality issues
Engineering Changes after Design exit
Poor Test Coverage / Repeatability
The key to achieving High Reliability is therefore a multi factor solution with focus on measurement wherever possible. Individual measurements alone may not provide the direct correlation to failure rate in the field, but the Holistic combination of the correct measurements certainly will.
The key factors and measurements that contribute to minimising failures are highlighted below;
Design Quality measured as % Design Maturity from Design Quality Assurance (DQA testing)
Design for Manufacturing (DFM) scoring to measure ease of repetitive manufacture
Design for Test Scoring (DFT) to measure Design focus on Testability and Test Coverage
Factory Readiness Review scoring
Supplier Quality Rating and scoring
Supplier Quality monitoring with Early Life escape predictions from Yield measurement
Early Life Reliability Testing
Accelerated Life Test
Only if all are driven to achieve highest possible level can we then expect world class reliability with a new product which can be maintained throughout its production life cycle.
The final step is how we combine the measurements into a simple format that produces a single result, this is done with a comprehensive NPI matrix where each key item has a weighted score which reflects the effect on its ability to highlight potential issues (DFM, DFT, Supplier ,Rating, etc) or stimulate latent defects (Design Quality Testing, Early Life Reliability Test, ALT, etc)
Each element of the NPI matrix will have targets set and depending on the measurements made or defects found, the result of each measurement or test will receive a % rating which is MULTIPLIED by each weighted score to provide an overall Nett score foe each of the individual measured elements within the NPI matrix
The NPI model example shown below clearly shows how the nett scores are achieved and the overall NPI score calculated
It is also important to note the NPI model has a ‘memory’ as scoring is included from all activity throughout the development phase from EVT (Engineering Verification or Pilot test) , DVT (Design Verification Test) and finally PVT (Production Verification Test / Pilot Production Test) . In this way the success or failure of Engineering testing is included as the success level early on in the Design Cycle will have an impact on later stages unless the Design is scrapped and re-started when engineering testing is very poor and risk of going forward is high.
Once the overall NPI score is calculated the Project Team / Project Manager can review from the one document the risk of moving into full blown mass production. This is totally different from a quite normal approach where engineering groups argue over issues and commit to getting everything right before mass production.
Such an approach is always doomed to fail, hence the NPI model brings all the key measurements together for a professional and organised approach to monitoring a products performance from beginning to end.
The scoring approach adds clarity and enables senior management to simply as one question ‘Did we meet the target score?’
This model has worked very successfully with many of Reliability Solutions clients, if you would like to find out more contact us using the details below.
For more information on Holistic Reliability – The Modern Day Solution talk to Reliability Solutions
Enquire Now
List your company on FindTheNeedle.