
Sign In
Cloud-based Cooling
09-04-2019
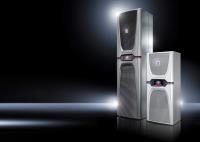
By Karl Lycett, Rittal’s Product Manager for Climate Control
Cooling units are playing an increasingly important role in Industry 4.0. Seamless communication between cooling units and associated cloud-based systems is opening up opportunities for new applications. Essential to these applications are IoT-capable devices such as the cooling units and chillers in the Rittal Blue e+ range.
During the lifetime of an enclosure cooling unit, the costs incurred for energy, maintenance and service are usually much higher than the initial investment in the unit itself.
Optimisations carried out during maintenance can help reduce workload and thus lower costs, for example through predictive or needs-based maintenance. Needs-based maintenance, however, always requires information about the individual cooling units and the surrounding conditions. A typical example is replacing a fan before a fault occurs, which otherwise – in the worst-case scenario – could cause not just the cooling unit, but the entire system to fail. If there is historic information available to plant operators about the fan’s running time, the difference between its expected and actual speeds, and its power consumption, then it’s possible to identify a gradually developing fault or an impending failure. This means that vital components can be replaced early on, increasing the overall system’s availability.
Other information, such as energy consumption, the condition of individual components, ambient conditions, or even the level of soiling on the filter mat, can also provide useful data, and practical opportunities to optimise maintenance and energy efficiency.
It’s not surprising, therefore, that seamless communication of information between systems is growing in importance. In a state-of-the-art factory, where data is easily available as and when required, the sight of maintenance technicians walking from one cooling unit to another, jotting down information with a clipboard and pen, is a thing of the past.
Networking is possible now
Rittal equips its climate control solutions with a comprehensive range of communication options.
Using the new IoT Interface, Rittal units can communicate directly with superordinate systems and network with customers’ in-house monitoring and energy management systems. As a result, data such as the internal/external temperature of enclosures, and the temperature of condensers and evaporators, can be continuously evaluated. Added to which, the run times of compressors and fans is easily accessible, as is information on capacity utilisation, messages and unit settings. Plant operators can therefore identify potential malfunctions early on, improving the reliability and availability of their systems.
Numerous industrial protocols are supported, allowing climate control solutions to be integrated into IoT applications, which paves the way for smart service solutions. Additionally, information from the units can be used in cloud-based systems for a wide range of analyses.
Predictive maintenance and data analytics
At last year’s Hannover Messe, Rittal demonstrated the future of Industry 4.0 applications such as predictive maintenance and data analytics together with Siemens MindSphere and IBM Watson IoT.
Industry 4.0-capable Rittal units were integrated into Siemens MindSphere. This cloud-based, open IoT operating system enables users to develop their own Industry 4.0 applications. Using Siemens MindSphere, the platform is scalable and can capture and analyse huge volumes of data – paving the way for smart-factory applications, for example, in predictive maintenance, energy data management and resource optimisation.
As I indicated at the beginning, needs-based maintenance is cheaper than carrying out maintenance work at fixed intervals, and raises system availability. Our solution also calculates the shortest routes between calls for service engineers, which eliminates wasted journeys at facilities with a large number of machines. And live data on each unit means staff can bring the right spare part with them straight away!
Rittal products also interoperate with the cloud-based data analytics system IBM Watson IoT. Watson’s architecture is designed to process information rapidly, and employs machine-learning algorithms to analyse ever-growing data volumes. Data analytics applications are used to make maintenance more efficient and achieve a high standard of operational reliability.
Again, customer benefits include improved machine availability and optimised maintenance costs. The solution’s new technologies also make new business models - such as smart maintenance contracts - possible.
Visualised data in the cockpit
With the introduction of the Blue e+ cooling unit series, Rittal has set new standards for the energy efficiency of electrical enclosures.
Thanks to diagnostic software, users can go a step further, and save more energy through the optimum operation of their cooling units. Comprehensive information is essential of course, and all the relevant data is provided by the new data cockpit in RiDiag III. All the information collected from the cooling unit’s numerous sensors is clearly displayed and evaluated, including temperatures, the input voltages and currents at the compressor.
The EER (Energy Efficiency Ratio) display is particularly useful, allowing users to track how energy efficient the cooling unit is under specific environmental conditions and with specific settings. By analysing the data, users can optimise parameters, achieve additional efficiency improvements and hence lower costs.
What we’ve wanted to show in this article is how how the IoT Interface can be used, providing an insight into future Industry 4.0 applications and their potential benefits. All this stems from the seamless transmission of data from sensors inside the cooling units and chillers to the cloud.
For more information on Cloud-based Cooling talk to Rittal Ltd
Enquire Now
More News And Press
List your company on FindTheNeedle.