
Sign In
ROBBI: Italian Grinding with Style
07-08-2013
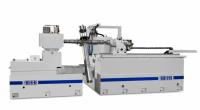
By Simon Rood - Wednesday 3rd October 2012
Erith-based RK International Machine Tools Ltd is working with ROBBI, the Italian specialist in cylindrical and internal grinding to meet the requirements for more challenging grinding solutions, particularly in aerospace and defence applications.
Dick Aldrich, RK sales director, explains that there has been a marked shift towards specialised cylindrical grinding applications in these sectors in the UK, demanding bespoke solutions for large, high value, more complex components in difficult and unusual materials. Projects such as these also require a greater emphasis on operational life expectancy and reliability of the machines, due the high cost in replacing or upgrading during the lifespan of the components being produced. They also often require the added flexibility of being able to adapt for the machining of different components as new developments are made to the production process.
Dick Aldrich points out: “The problem with grinding is that the process involves a whole host of variables, including the material being ground. Allowances have to be made for varying stock levels, the intricacies of wheel development and progressive in-cycle influence of wheel wear, the setting of feed variation points and dwell times and the consideration of coolant, filtration and thermal effects.
RK has worked with ROBBI for 12 years and the Italian company's experience in a variety of applications has enabled the creation of higher productivity solutions. In various UK aerospace applications, for example, RK and ROBBI have engineered solutions such as the grinding of stellite bearings, ceramic materials and demanding motor shafts for helicopters. Dick Aldrich explains: "We started with one machine which went to an MOD gearbox rotor shaft repair facility in Perth. The next few years were a learning curve with the need to find niche markets in the UK.
The 1500 and 2 metre machines are extremely competitive on price and with the boost in manufacturing over the past couple of years, we are selling four or five machines a year. "We're not selling a box, we're selling a specific solution. Grinding machines have longevity and can be in use for 25 years. During a recession people tend to keep hold of existing kit and don't invest."
Despite this challenge, 2011 was the most profitable year in the company's history. ROBBI GROUP s.r.l. is based in Veronella, near Verona and was founded by Italo Robbi, a skilled engineer and the inventor of precision engineering systems, in 1934.
In 1963, his son Angelo succeeded him as managing director and transferred the company to Cologna Veneta, where he increased the model range and introduced new machine tools.
In 1984, exactly 50 years after its foundation, Angelo's son Roberto began to make a significant contribution to the development of the company. The production line was further improved and the manufacturing equipment upgraded.
In 1990, a new facility was built in Veronella, a few miles from Cologna Veneta and all manufacturing moved to the new premises. Production was again improved with the introduction of new advanced technology manufacturing machines.
ROBBI now has a 110,000 square feet manufacturing facility where its 50 employees work alongside an impressive technical team to develop and manufacture equipment for export all round the world. This includes engine rebuilding equipment for automobiles, trucks and heavy equipment, universal grinding machines for external and internal grinding, and vertical precision honing machines for hydraulic cylinders.
In 2008, Riccardo, son of Roberto and grandson of Angelo Robbi, joined the company to concentrate on design, engineering and after sales service. Nearly every customer comes to the factory and talks to Riccardo. He describes how the company has moved towards larger bespoke solutions for customers:"We started with small conventional machines from 600 mm to 1 metre with a 160mm height of centre. We also manufactured medium-sized machines with 180 height of centre, 600, 1 metre, 1.5 metre, 2 metres and 3 metres. We then moved on to heavy duty 1 metre, 1.5 metre, 2 metre and 3 metres. The next step was to move up to 3 metre, 4 metre, 5 metre and 6 metre. For example, 2 years ago, we supplied a heavy duty 5 metre machine to Algeria for compressor manufacturing.
The market is moving to very big machines, We fulfilled a big order for eight 600 mm machines to Egypt last year but we now tend to focus on special projects and single design machines. We are currently working on a special application completely different from our design. It has a granite bed and is a prototype developed with an Italian customer for a year. It should be finished by the end of the year and will enable us to make another significant step forward.
"We have an internal design department developing machines to customers' specific needs and we are very flexible. We have 5 people in the design department. All mechanical design takes place inhouse, but
90% of software design outsourced. Our future is special applications. Last year we installed our first heavy duty 10 metre machine in Italy for rubber grinding designed from scratch at ROBBI. Design took 3 months and the machine build completed in 8-9 months with the last 5% at the customer's site. The addition of hydrostatics was a good opportunity to try out new technology. As well as the design department, we have
two operations in the factory: assembly and manufacturing. We outsource the painting and box making as we want to focus on machine building and new technology."
There are a number of big projects on the go including a current build at the Robbi factory of a 1500 machine for landing gear. The machine is due to be installed in October. The coolant tank is at the back of the machine and will be sunk into the ground in channels. The aim is to grind small and large pieces on the same machine. With a height of centres of 350mm and a 1500mm swing, the wheelhead moves on hydrostatic guides with a hydrostatic spindle and a 915mm diameter Norton grinding wheel.
Four machines have been supplied by ROBBI for a project in Saudi Arabia. These were a very large honing machines, a 3 metre grinder, two 1500 grinders. During trials massively improved cycle times have been achieved. Other projects have included a 2nd machine for wing generation gearbox in Finland, a 4 metre chocolate making machine with sub micron precision and a machine for the manufacture of landing gear in Israel.
Riccardo Robbi adds: "Our business is very wide. We produce machines from 600mm to 10 metres. One of our biggest automotive projects was a 6 metre machine for crankshaft grinding of diesel engines in Genoa. 2 years ago, a 6 metre machine and a 4 metre machine in Germany for compressor manufacturing. We also do a lot of special applications e.g. in Holland for small compressors in refrigerators."
ROBBI originally built vertical honing machines with a limited tube length of 2 metres. 10 years ago, the company developed its first horizontal honing machines up to 12 metres. There is a current project with an Italian customer that already has three ROBBI honing machines for a honing, rolling and boring machine for a special application on large cylinders. Robbi was the first to make honing machines with both workpiece and tool rotation to improve roundness and Dick Aldrich sees potential in the UK for these machines.
Roberto Robbi says: "Every machine we develop grows the company and we are working on standardising parts to mix and match on specific applications. Dick Aldrich adds: "We have started a project with ROBBI to develop a barrel shape grinding machine. This is a 4 metre machine with sophisticated measuring system and eccentric spindle giving an axial movement but operating radially. For making a concave profile on a roll. We have a lot of enquiries now for this shape."
The full range of ROBBI grinding machines can be viewed by visiting our website.
RK International Machine Tools Ltd
Tel: 01322 447611
Email: sales@rk-int.com
www.rk-int.com
Article first published in Grinding and Surface Finishing Magazine, Sept 2012. Courtesy of Roger Barber Publishing
For more information on ROBBI: Italian Grinding with Style talk to RK International Machine Tools
Enquire Now
More News
List your company on FindTheNeedle.