
Sign In
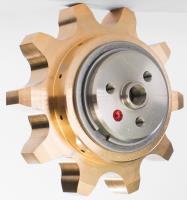
There are many challenges facing you as a baker: food safety,
reliable manufacturing processes, for example the cooling of
ovens, and – just as important – the reduction of operational and
maintenance costs.
When production is running non-stop, any breakdown due to
lubrication failures can be very expensive for you. Just imagine
the loss of production due to a lubrication failure in an oven
bearing or in the cooling tunnel of a freezer. Key components
requiring specialized lubrication in the bakery industry are
transport chains, as the environment can be challenging
due to elevated temperatures and high humidity. Improper
chain lubrication here can lead to residue build-up, wear and
eventually the loss of articulation in these chains. All the above
could ultimately result in a breakdown, bringing production and
output to a complete halt.
Increase food safety
The selection of the right lubricant can play a major role
in food safety. Product recalls can cost the manufacturer
enormous time and money – if not their reputation. Even a minor
contamination of a food product with lubricant, which cannot
always be technically avoided, can have severe consequences.
Innumerable regulations have to be observed in the production
of food: on hygiene, regarding the machines or the materials
used. Maintenance technicians, production and quality
managers have to take all these regulations into account for
the selection of lubricants. As a manufacturer of food products,
you will not be content just to have lubricants that comply with
legal regulations. You also expect them to be physiologically
safe, neutral in taste and odour; they should reduce friction and
wear, remove heat and seal components. As a global leader in
speciality lubricants, Klüber Lubrication offers a comprehensive
line of NSF H1 registered lubricants designed to meet the
extreme demands of the bakery industry.
Certifi ed hygiene for the entire process
ISO 21469 is the international hygienic standard for the
formulation, manufacture and use of H1 lubricants used in
the food-processing and pharmaceutical industries. The NSF
developed a certifi cation procedure on the basis of ISO 21469,
which includes annual inspection of the lubricants-producing
plant by an National Sanitation Foundation (NSF) auditor to
check strict adherence to hygiene requirements, preventing
contamination during the manufacture of H1 lubricants.
Product samples are taken on an annual basis and analysed for
contamination, and also lubricant packing, storage and use are
evaluated during the audit. In order to get a plant certifi ed under
ISO 21469:2006, it may be necessary to make some changes
in the manufacturing process calling for heavy investments to
enable compliance. Klüber Lubrication was amongst the fi rst
few companies to be certifi ed under the stringent requirements
of this standard.
What does this mean for you? It means that not only
our products are certifi ed, but the whole manufacturing
process of our H1 lubricants as well. This ensures complete
protection against contamination during lubricant
manufacturing
For more information on Kluber High temperature oils for the Bakery Industry being applied automatically whilst the Oven is operating talk to Rotalube Systems Limited
Enquire Now
More Case Studies
List your company on FindTheNeedle.