
Sign In
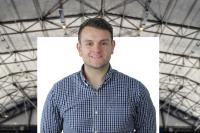
Founded in 1977, fabric-tensile building experts Rubb Buildings Ltd celebrated their 45th anniversary last year.
“You don’t make it that long in this industry without knowing what you’re doing,” says Ryan Clarke, Rubb’s Aviation Sales Specialist since 2018.
From deployable fighter jet hangars to wide body triple-span MRO facilities, Rubb has covered every corner of the aviation sector worldwide in its 45 years of business.
“Time served like that means we have an incredible amount of experience in our design, steel, and PVC production departments. Some of us have been here since the beginning.”
Although Rubb has been manufacturing its fabric-tensile buildings since the ‘70s, they still represent a relative niche in the aviation industry when compared to traditional steel-clad and concrete builds. Rubb’s buildings are designed to British Building Standards or Euro Codes regarding wind speeds and snow loadings, so they are placed directly within the same market as these traditional hangars.
“We offer an alternative solution, but we come with a track record only an industry leader could have. Just look at our previous projects.”
Seeing is believing
How can Rubb convince potential clients that their steel-framed, PVC-clad buildings are right for their multi-million-dollar MRO operations?
“All it takes is one visit,” Ryan explains. “One visit to see that, yes, this is a completely viable, cost-effective option for their operations. Some companies can’t do that.
“Our hangars are seriously impressive in person. Huge clear spans, amazing lighting. The hot-dip galvanized steel framework looks fantastic; you can feel the quality of it. When they visit, they see that these hangars are built to last.”
Rubb’s previous projects include MRO hangars for easyJet, British Airways, and Turkish Technic, but only one is Ryan’s go-to for client visits.
“It has to be Bro Tathan.” Completed in 2021 for the Welsh Government’s Bro Tathan Business Park in the Vale of Glamorgan, the 50m span by 50m long MRO hangar is capable of housing aircraft such as the Boeing B737-800 and Airbus A320-A321, and is complete with a 42m wide vertical lifting door.
“It’s quite a drive from our Gateshead HQ, but the journey is well worth it,” he continues. “The hangar has such a clean finish; it’s a great example of what Rubb can accomplish.
“It’s also a fantastic showcase of our Thermohall® insulation, as it’s clad with 150mm of it.”
Game-changing insulation
Thermohall® insulation is the card up Rubb’s sleeve when it comes to ensuring their competitiveness in the market. High-density, non-combustible glass wool is placed between Rubb’s PVC cladding to create a climate-controlled environment inside the hangar, maintained by state-of-the-art HVAC installs.
Comfortable working environments are ensured by keeping the heat out in hot climates and fostering warm ambient temperatures in colder climes. Rubb’s patented Thermohall® insulation also insulates sound, which is hugely beneficial to MRO operations due to their airside locations.
“Thermohall® is a game changer,” Ryan adds. “Our clients love it; the system is so efficient. It saves on heating and air conditioning costs while making sure their staff are comfortable all year round, no matter where the project is based. We even had a Thermohall® building in Greenland, where it drops below -70°C.
“The energy-efficiency of the system is a great bonus for our clients, who now more often than not have sustainability goals to meet.”
The green choice
Net Zero goals are becoming more and more prevalent across the aviation industry, and Rubb is uniquely positioned to meet these requirements.
“We’re green,” Ryan begins. “We always have been, it’s in the DNA of the product.
“Our steel frames can be recycled, so can our PVC cladding. It doesn’t often come to that, though. The hangars can be packed up, refurbished, then stored or sold. Clients can move them anywhere to meet changing logistical needs. If those needs change but the location doesn’t, the buildings are modular so we can extend them.”
Rubb did just this with their project for easyJet in London Gatwick Airport. The MRO hangar began as a 91.5m twin-span completed in 2016, but in 2020 operations needed to be expanded. They opted to extend the hangar with a third 47m span bay to meet this demand.
“There’s no waste,” he explained.
“A traditional build doesn’t have this flexibility. You’d be wasting time, materials, and funds.”
What’s next for Rubb?
“We have some exciting projects in the pipeline,” Ryan begins. “As well as some interesting product innovations that we’re not quite ready to talk about yet.”
Though tight-lipped when it comes to future plans, Ryan will be attending several aviation events throughout 2023.
“We’re going to be exhibiting at the MRO Middle East, Europe, and Asia Pacific events. Our colleagues in Rubb, Inc.—our USA-based sister company—will also be attending MRO Americas, so we have full coverage.”
Rubb Buildings Ltd spent last year celebrating its 45-year history, but now it’s time to look forward. The aviation sector is key to Rubb’s growth and will remain a core focus of its innovations going forward.
For more information on Talking MRO hangars with Aviation Specialist Ryan Clarke talk to Rubb Buildings Ltd
Enquire Now
List your company on FindTheNeedle.