
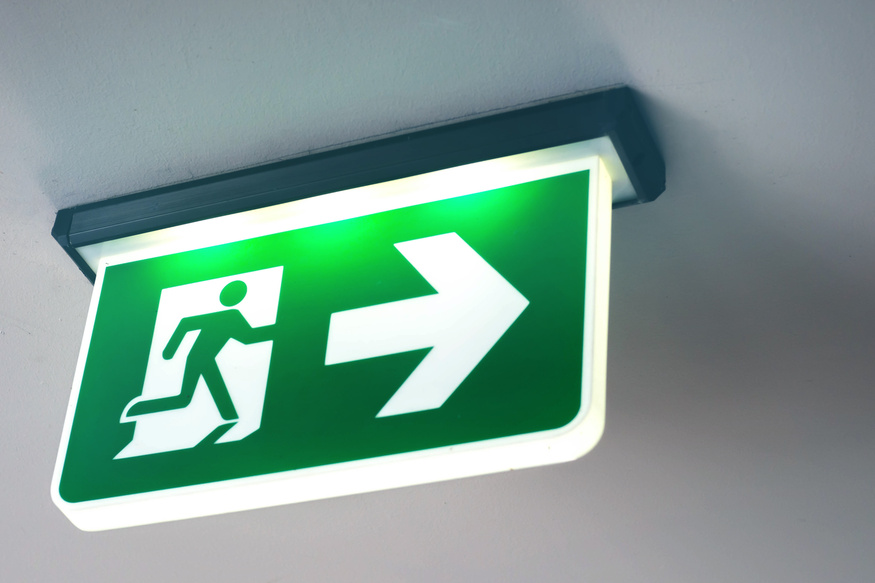
UK Regulations and the Importance of Regular Inspection
Emergency lighting plays a critical role in maintaining a safe working environment during unexpected power failures or emergencies. It provides illumination and guidance, enabling safe evacuation and reducing the risk of accidents. To ensure the effectiveness of emergency lighting systems, the United Kingdom has established comprehensive regulations and standards. This article explores the importance of emergency lighting health and safety, and the key regulations in the UK, and emphasises the significance of regular inspections as laid down in BS 5266 and other relevant regulations.
Importance of Health and Safety of Emergency Lighting in the Workplace
Emergency lighting is vital for the safety and well-being of employees, visitors, and occupants in the workplace. During power outages or emergencies such as fires, proper illumination ensures clear evacuation routes, enhances visibility, and minimises panic. Emergency lighting systems must be properly designed, installed, and maintained to guarantee their reliability in critical situations. Adhering to health and safety guidelines for emergency lighting helps create a secure environment and ensure legal compliance.
Regulations Governing Emergency Lighting Health and Safety in the UK
- The Regulatory Reform (Fire Safety) Order 2005: This primary legislation imposes obligations on the responsible person (usually the employer or business owner) to assess fire risks and implement appropriate measures, including emergency lighting. It requires the provision and maintenance of emergency lighting systems that align with British Standards and relevant regulations.
- British Standard BS 5266: This standard provides detailed guidelines for emergency lighting design, installation, and maintenance. It covers various aspects, including system types, minimum illumination levels, signage, testing, and periodic inspection. Compliance with BS 5266 is essential for ensuring the effectiveness and reliability of emergency lighting systems.
- The Health and Safety at Work Act 1974: This overarching legislation places a duty on employers to ensure the health, safety, and welfare of their employees and others affected by their work activities. It encompasses emergency lighting as part of general workplace safety provisions. Employers must provide suitable emergency lighting systems and conduct regular inspections to ensure their proper functioning.
Importance of Regular Inspection as per UK Regulations
Regular inspections are vital for the health and safety of emergency lighting systems in the workplace for the following reasons:
- Compliance with Standards: Regular inspections ensure compliance with the requirements outlined in BS 5266 and other relevant regulations. Inspections verify that emergency lighting systems meet the specified standards, including minimum illumination levels, adequate coverage, and proper signage.
- Functionality and Reliability: Inspections help verify the functionality and reliability of emergency lighting systems. They allow for the identification and rectification of any faults, damaged components, or ineffective backup power sources. Regular inspections ensure that emergency lighting systems will function as intended during power failures or emergencies.
- Emergency Preparedness: Regular inspections contribute to emergency preparedness by maintaining the readiness of emergency lighting systems. Inspections ensure that all components, including batteries, lamps, and control systems, are in proper working condition and can provide the necessary illumination for a sufficient duration during emergencies.
- Testing and Maintenance: Inspections provide opportunities for testing and maintenance of emergency lighting systems. They facilitate periodic functional tests, including full system tests and battery discharge tests, to validate the system’s performance. Maintenance activities, such as cleaning, lamp replacement, and battery checks, can be conducted during inspections to keep the system in optimal condition.
- Occupant Safety and Evacuation: Well-maintained and regularly inspected emergency lighting systems ensure the safety of occupants during evacuations. Proper illumination reduces panic, facilitates safe movement, and enables individuals to locate and access emergency exits quickly and efficiently.
In Conclusion
The health and safety of emergency lighting systems in the workplace are essential for protecting occupants and facilitating safe evacuation during emergencies. The UK regulations, including the Regulatory Reform (Fire Safety) Order 2005, British Standard BS 5266, and the Health and Safety at Work Act 1974, provide guidelines for the design, installation, and maintenance of these systems. Regular inspections, as emphasised in these regulations, play a crucial role in ensuring compliance, verifying functionality, and maintaining the reliability of emergency lighting systems. Employers must prioritise regular inspections to mitigate risks, ensure occupant safety, and comply with legal obligations.
You also need to ensure when carrying out a Emergency lighting inspection that the follwing requirements are meet and compliant, The Health and Safety (Safety Signs and Signals) Regulations 1996, failure to ensure this is correct can leave you and your company open to servere penalties, and this is often overlooked by the £100 -150 merchants in the industry who fail to realise there responsibilities and leave you businesses open to large fines and prosecution.
Far too often when I inspect the paperwork and the time on site for these inspections, I see the whole building done and dusted in less than 2 hours for a 3-hour annual drain down, but the companies were cheap, using this as the basis for your inspections will not stand up in a court of LAW and leave your companies open to massive fines, and potential prison sentences.
For more information on Ensuring Health and Safety of Emergency Lighting in the Workplace talk to Safe Electric Nationwide Ltd