
Sign In
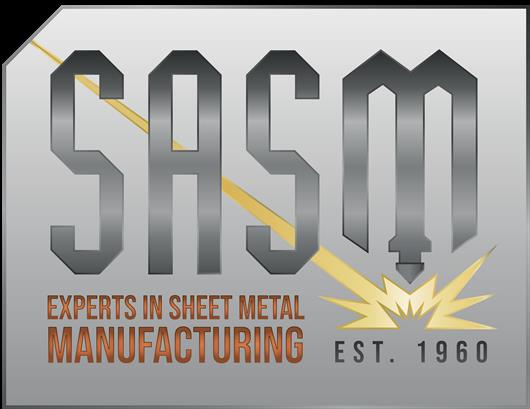
This is a form of bending, used for long and thin sheet metal parts. The machine that bends the metal is called a press brake. The lower part of the press contains a V shaped groove. This is called the die. The upper part of the press contains a punch that will press the sheet metal down into the v shaped die, causing it to bend. There are several techniques used here, but the most common modern method is "air bending". Here, the die has a sharper angle than the required bend (typically 85 degrees for a 90 degree bend) and the upper tool is precisely controlled in its stroke to push the metal down the required amount to bend it through 90 degrees. Typically, a general purpose machine has a bending force available of around 25 tonnes per metre of length. The opening width of the lower die is typically 8 to 10 times the thickness of the metal to be bent (for example, 5mm material could be bent in a 40mm die) the inner radius of the bend formed in the metal is determined not by the radius of the upper tool, but by the lower die width. Typically, the inner radius is equal to 1/6th of the V width used in the forming process.The press usually has some sort of back gauge to position depth of the bend along the workpiece. The backgauge can be computer controlled to allow the operator to make a series of bends in a component to a high degree of accuracy. Simple machines control only the backstop, more advanced machines control the position and angle of the stop, its height and the position of the two reference pegs used to locate the material. The machine can also record the exact position and pressure required for each bending operation to allow the operator to achieve a perfect 90 degree bend across a variety of operations on the part.
For more information on Press Brake Forming talk to Saint Anns Sheet Metal Co. Ltd
Enquire Now
More products
List your company on FindTheNeedle.