
Sign In
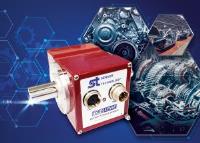
A UK company has committed to resetting the standards of accuracy for dynamometers, ahead of the increasing demand driven by the worldwide interest in improving engine efficiency and performance. Its technology is based on a new torque measuring technology, also of British origin.
RTEC Engineering Ltd is a contract engineering services company based near Mansfield in Nottinghamshire, specialising in metrology. Its Managing Director, engineering metrologist of 20+ years’ experience Rob Langton explains:
“Our sub-division, RTEC Powertrain, is working on a number of projects with B2B partners with a focus on metrology solutions for the automotive industry including ECM (engine control module) calibration and diagnostics.”
“A couple of years ago I found myself requiring a detailed performance profile of a particular engine, but could not find a dynamometer that was sufficiently accurate and reliable within a limited capital budget. With a wealth of engineering experience in various disciplines, I simply set about designing and manufacturing my own. With a focus on replicating the accuracy and reliability of an OEM or lab-grade system, at a market rate more suitable for small to medium sized enterprises.”
Torque measurement system used by RTEC Engineering on their dynamometer
Langton was keen to improve on the use of load cells and RPM sensors commonly found in traditional dynamometers, by introducing more advanced technology. A search of the specialist literature introduced him to Sensor Technology in Banbury and its non-contact TorqSense transducer.
Engineers from Sensor Technology assessed Langton’s brief and recommended the SGR510/520 series TorqSense. This uses a full four element strain gauge bridge, formed from four strain gauges glued onto the drive shaft of the engine under test in a square formation set at 45deg to the axis of rotation. When the shaft turns two gauges are stretched into tension and two go into compression.
A rotor mounted ultra-miniature microcontroller, powered by a non-contact inductive coil rather than through a cable, measures the difference in strain values in each gauge and transmits them back to the stator digitally, via a second, high frequency coil. The transducer then compares the four signals and calculates a high accuracy torque measurement.
“The inductive coils mean TorqSense does not require wires with slip ring connections to the shaft, thus giving the ease of use we want,” says Langton. “Crucially for our work, its 250% overrange capacity, allowed sudden spikes in load to be measured and recorded accurately. It is almost immune to noise and the signal corruption associated with slip ring set-ups, whiles it 4000/sec sampling rate meets our resolution requirements.”
With the help of Sensor Technology, RTEC soon had the ideal solution to manufacture a high performance dynamometer that met their design brief. Langton started wondering if other businesses could benefit from such a sensitive test rig too, and so he conducted some research to evaluate the market.
While elements of a dynamometer such as the load cell can be calibrated by a UKAS (the United Kingdom Accreditation Service) accredited laboratory or similar, outside of the larger organisations such as OEM’s and competitive race teams calibration is generally not mandatory.
RTEC saw this as a gap in the market and are working on a solution based on a scalable, modular design of dynamometer, with TorqSense at its heart. One of the significant advantages of TorqSense is that it comes calibrated from the factory to NPL (National Physics Laboratory) standards and as a self-contained unit. This in combination with the plug-and-play design intent means that it can be easily exchanged when calibration is due which limits down-time.
Future planned projects include designing and manufacturing bespoke test rigs that are customised to users exact requirements, along with the retrofitting of TorqSense into existing dynamometers and test rigs for precision instrument drives to heavy vehicle power trains.
For more information on Adaptable dynamometer system set to replace self-build test rigs talk to Sensor Technology Ltd
Enquire Now
List your company on FindTheNeedle.