
Sign In
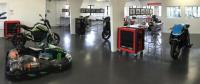
Saietta Group Ltd is a UK based research and development company which designs motors for light-weight electric vehicle (EV) propulsion. The company’s latest innovation is the ‘S-AC’ which is an ultra-efficient brushless axial-flux AC motor. It boasts extreme efficiency levels at high torques from low speed onwards.
S-AC is designed for mass manufacture and is optimised for light-weight electric vehicles such as scooters, motorbikes, quadbikes, rickshaws, small cars and marine applications. The primary target market is Asia where Governments are mandating the rapid transition for all forms of transport to electric propulsion to combat chronic pollution.
The unique motor architecture was designed by Saietta’s engineering team, based on Saietta’s DC axial-flux motor, which was originally developed by Cedric Lynch (Saietta’s Chief Scientist) who is internationally recognised as a pioneer in electric motor design. Saietta motors have been used to achieve multiple world-firsts on land, sea and air, including winning the first Isle of Man TT Zero all electric motorcycle race.
Saietta works with vehicle manufacturers to firstly understand in detail the specific motor requirements for individual EV applications and then engineers the S-AC technology to deliver tailored solutions. Saietta also provides engineering and integration consultancy for entire electric drivetrains.
Saietta’s Applications Engineering team is heavily reliant upon a set of test rigs that it has developed in conjunction with its Oxfordshire neighbour Sensor Technology Ltd.
A lot of Saietta’s work is based on constantly refining and testing motor designs, moving toward an optimum solution for each application field. As engineer Chris Lines explains: “The switch from DC motors to AC means we are able to improve efficiency still further and reduce maintenance requirements because there will be zero brush-wear.”
The test rigs at the heart of Saietta’s development work are based on the principle of running two motors back to back, adding power to counter the losses and measuring efficiency. For this the engineers selected a TorqSense transducer from Sensor Technology, which operates wirelessly so that setting up between test runs is minimal because there is no need to reset delicate slip rings.
The operating principle of TorqSense is based on bouncing a radio signal off the rotating shaft of the motor under test and measuring the distortion in the return wave. To do this two tiny piezo electric combs are glued onto the shaft at right angles to one another. These are pulled slightly out of shape as the shaft rotates and thus disrupt the radio waves as they are reflected back.
“The amount of twist in the shaft is proportional to the torque of the moment,” says Chris, “So we get a direct reading. The fact that we do not have to hardwire the transducer to the shaft through slip rings means we can set up a test very quickly and reset everything just as quickly. If we had to adjust slip rings every time, our test programme would take far, far, longer to complete.”
TorqSense offers CANbus output options for in-vehicle applications, so is popular with many organisations developing drive trains for electric vehicles and also in other low carbon developments such as wind turbines and tidal flow energy.
For more information on Mass market electric vehicles getting revved up for launch talk to Sensor Technology Ltd
Enquire Now
List your company on FindTheNeedle.