
Sign In
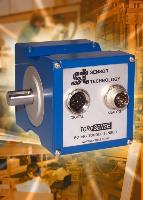
Measuring torque on rotating shafts on a test rig is one thing, but the environmental challenges of real world applications can quickly impact on the functionality and reliability of torque transducers, as Mark Ingham of Sensor Technology explains.
There are many approaches for measuring torque, from the simple to the more exotic, and under benchtop conditions or in less arduous applications they can all provide reliable results more or less out of the box. But out in the real world or on heavier duty systems, conditions are rarely ideal. So how do the different technologies fare, and what can the user do to mitigate the problems?
Consider, for example, heavy duty applications in marine, agricultural, renewable energy, offshore and materials handling industries, as well as more specialist or exotic sectors such as aerospace or Formula 1. The torque sensor may well have to deal with dust, dirt, condensation, extremes of temperature, vibration, and more. In addition, we always have to consider the effects of electrical noise and electromagnetic interference in the environment.
Any or all of these can quickly impact on the reliability and accuracy of the output torque data, as well as reducing the working life of the instrument. Let's consider, then, torque measurement instruments built on the most widely used principles - strain gauges, phase measurement, magnetism and surface acoustic waves - and see how they compare in these challenging environments.
A quick recap first on the different torque measurement principles. The strain gauge is a torque sensor that is bonded directly to the shaft, with connection to the signal conditioning unit using either slip rings inductive coupling. Where slip rings are used, contact is made via brushes. Where inductive coupling is used, either a rotary transformer or radio telemetry can be employed. In a rotary transformer arrangement, either the primary or secondary coils rotate with the shaft. In a radio telemetry system, a stationary antenna induces power in the loop antenna of the rotating shaft, powering the strain gauge transmitter. The strain gauge information is encoded as a frequency modulated signal. A stationary coil placed nearby picks up the signal and feeds a decoder.
Phase measurement techniques can be built around various different sensor technologies, including optical, proximity and displacement. The principle is similar for each: if sectioned or toothed discs are mounted at either end of the shaft, offset from one another, then the relative movement of the two discs is proportional to torque and can be detected.
Torque measurement systems built around optical sensors can also provide a useful solution. If sectioned discs are mounted at either end of the shaft, offset from one another, then the relative movement of the two discs changes the effective aperture in a way that is proportional to torque. With no susceptibility to electromagnetic interference and noise, the optical technique can provide a useful method of torque measurement. Capacitive sensors can also be used, in a device that measures the change in capacitance as the twisting shaft changes the gap between two charged plates.
Magnetic measurement techniques are built on the principle of changes in magnetic field of a material as it twists. The resulting changes in magnetic field are proportional to the applied torque, and can be measured by magnetic field sensors, enabling the torque value derived.
A relatively new technology for the measurement of torque in a rotating shaft is that using the properties of surface acoustic waves, measuring the resonant frequency change of surface acoustic wave (SAW) devices in a non-contact manner when strain is applied to a shaft to which SAWs are fixed. The applied torque causes a deformation of the quartz substrate of the SAW device, which in turn causes a change in its resonant frequency. Such devices have been pioneered by Sensor Technology in its TorqSense range of products. In these products, two SAWs made of ceramic piezoelectric materials containing frequency resonating combs are glued onto the shaft at 90 degrees to one another. As the torque increases, the combs expand or contract proportionally to the torque being applied. An adjacent RF pickup emits radio waves towards the SAWs, which are then reflected back. The change in frequency of the reflected waves identifies the torque. There is no need to supply power to the SAWs, so the sensor is non-contact and wireless.
So how these different technologies stand up to the problems of the most demanding environmental conditions?
For more information on Measuring Shaft Torque in Challenging Environments talk to Sensor Technology Ltd
Enquire Now
More News
List your company on FindTheNeedle.