
Sign In
New technology caps pharma bottling process
08-03-2022
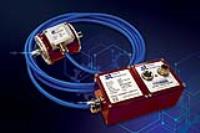
A regular customer of Sensor Technology Ltd has switched to its latest range of torque sensors.
The new TorqSense SGR530/540, being introduced throughout 2020 and 2021, measures torque using a full four element strain gauge bridge. With this, four separate strain gauges are fixed to the drive shaft of the plant or machinery being monitored. The gauges are aligned so that each measures shaft deflection in a different direction as it rotates under load. Electronics within the sensor collects readings from all four gauges and uses them to calculate the torque value in real time.
Sensor Technology has specialised in real time torque measurement for over 40 years, pioneering the use of wireless solutions based on radio frequency pick-ups that do away with the need for hard-wiring and unreliable slip rings.
Strict international rules apply to the manufacture and packaging of pharmaceutical products and require that the correct environment is maintained within the bottle or other packaging following capping. To this end, Regulation USP 671 provides a guide to the torque range to be used for screw type containers with varying closure diameters. By ensuring that bottle caps are successfully applied to the bottles within the required torque tolerances, the integrity of the product can be maintained.
Over the years Sensor Technology has worked with many OEMs to develop high precision, high speed machines for use in pharmaceutical plants and a range of other applications. One of these, an Oxfordshire neighbour of Sensor Technology, has for over 10 years incorporated TorqSense units into its capping machines.
Bottle capping is nearly always performed at very high speed, so that production targets are met. A major advantage of TorqSense is that it does not need to physically contact either the bottle caps or shaft of the torque head it is monitoring, instead using a radio frequency link. This means initial set-up and change over to new product runs is fast and efficient while operational reliability is not dependent on delicate slip rings.
"All you have to do is set up a TorqSense transducer in the capping machine and turn it on." explains Mark Ingham of Sensor Technology.
Significantly, the new SGR530/540 sensors are designed to be drop-in replacements for the older RWT430/440 units they are replacing. They are the same size and shape as their corresponding older model, with the same mounting holes, cables in the same position etc.
"All we have had to do to the capping machines is a straightforward swap-out of new for old. It only takes a few minutes,” explains Mark. “Our new SGR TorqSense units are getting a realistic long-term work out on the capping machines, working for long hours at high speed, where they are required to be 100% reliable and consistently accurate."
Fast and accurate torque measurement is becoming more and more important as all sectors of manufacturing automate their physical processes while also needing to improve the recording of production performance data. TorqSense is used in many industries from automotive to materials handling, test and measurement, FMCG (fast moving consumer goods) production, power generation etc. Sensor Technology is working with user-partners in many sectors to assess the new SGR units in a range of working environment.
For more information on New technology caps pharma bottling process talk to Sensor Technology Ltd
Enquire Now
List your company on FindTheNeedle.