
Sign In
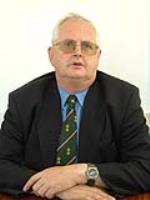
This past year it has been difficult to open an engineering magazine and not read about the Internet of Things (IoT), Industry 4.0 or Machine-to-Machine Communications (M2MC). But all the hype and predictions will come to naught if sensor manufacturers don’t rise to the challenges before them, says Tony Ingham of Sensor Technology Ltd in Oxfordshire.
The idea of Industry 4.0 first came to mass attention just a couple of years ago, when it was a theme of the massive Hanover Fair in Germany. Experts and ‘futurologists’ will tell you that Industry 4.0 is different from the IoT, and M2MC, but to those of us with a more down-to-earth understanding, they are effectively all the same – ways of significantly increasing the amount of data collected from production machinery and processing it in real time to produce better information, which in turn leads to increased productivity.
In fact, it is fairly obvious that the amount of data produced has been growing for many years and that this generally leads to better decision-making. However there is such a thing as information overload, when people cannot pick the important information from a sea of data, so are unable to make appropriate decisions. But this is a human condition and it can be treated by using a computer to automatically categorise all the data by importance and displaying it appropriately (including emergency alarms if necessary).
This real-time management of large quantities of data is a well-developed discipline and has become known as ‘big data’. This probably started in the control systems helping run petrochemical refineries, spread to other data-intense applications and has evolved from there. It is now widely used in many diverse industries from oil and gas recovery to retail management, from weather forecasting to geological surveys, from agriculture to infection control, from battlefield management to telecoms network operations.
Making data
Thus far, we have discussed using data, but in practice, before we can do that we have to produce the data. This is where sensors come in and we can quickly realise that they are in essence, the building blocks of Industry 4.0, etc. There are many types of sensor already in existence, from simple on/off switches and counters to sophisticated sensors like my company’s TorqSense, which continuously measures the torque generated by a rotating shaft.
It therefore seems inevitable that the technology of sensors is going to develop rapidly over the next several years. We already have sensors to measure just about every useful parameter, including temperature, speed, production rate, colour, viscosity, weight, pressure and torque, so new types of sensor are not required. The forthcoming developments will take us in new directions.
One obvious requirement is for ‘intelligent sensors’, sensors with on-board (or at least local) data processing capabilities. Instead of sending raw data off to the central control system for processing, these sensors do some or all of the processing in the field. They thereby produce refined information, which may be in a number of different formats, each suitable for a different type of user.
Sensor Technology pioneered this sort of distributed intelligence some years ago and has a long history of supplying intelligent sensors for many diverse applications. Currently, not all users want this capability, but those that do reap considerable practical benefits and are essentially setting up their own bespoke Intranet of Things.
It is probable that the demand for intelligent sensors will grow exponentially with the take-up of the IoT and similar concepts. With the groundwork and fundamental developments already put in place by technology-led companies, the trend is free to develop unhindered.
Islands of control
A logical development of the intelligent sensor is the sensor LAN (local area network) or sensor cluster. In this, a number of sensors feed either raw data or processed information into a nearby controller for further processing. This produces a highly distributed control systems architecture with attributes such as robustness, speed, agility and flexibility for change and development.
It is notable that a sensor LAN will be free to include different types of sensors, so could measure many diverse variables. It could also monitor say the temperature in multiple separate locations and/or the torque in a number of different drive shafts. Therefore, the level of information it could produce and forward to different users could be very highly developed.
Other trends we can expect to see in sensor development include cost reduction, miniaturisation and standardisation of communications’ protocols, plug-and-play, embedding capabilities and signal quality enhancements. Sensors may also need to develop the ability to bypass the central control system and supply information straight to the Cloud or a remote data archive. Perhaps, above all, sensors will have to be hugely flexible, easy to install and remove, easy to connect into a control network and easy to reconfigure for new duties.
Sensors used to be something of a Cinderella topic for control systems engineers, a bit of an after-thought and certainly not exciting. However, they are now rising to such importance that they could change the whole concept of control engineering.
For more information on Sensors will define the future of production and technology talk to Sensor Technology Ltd
Enquire Now
List your company on FindTheNeedle.