
Sign In
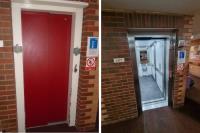
For many older people, moving into a retirement community can be an essential lifeline to retaining their sense of independence. Recent research shows that almost two thirds of people in the UK move into retirement housing primarily to downsize their living area, making life more manageable[1].
Retirement living offers over-55’s a number of benefits, including increased security and safety, an opportunity to socialise regularly, and a higher likelihood of remaining active and healthy. But for people with limited mobility, retirement offers another important advantage: the reassurance that they will have step-free access to their home.
The challenge
As retirement housing properties get older, lifts also age with them, meaning they can fall into disrepair due to wear and tear or the obsolescence of parts. This means residents can face serious disruptions to their independence from lifts that have been taken out of service to await essential part replacements or repairs.
For residents in a retirement community, the existing 4-stop hydraulic passenger lift, originally installed in 1989, was in need of complete refurbishment due to worsening reliability issues and obsolescence of the lift’s components.
To bring the lift back up to “state of the art”, it would need to undergo a major refurbishment to replace some of the functional components, as well as the ageing car doors and interior.
The client
Owned by a housing provider, the retirement flats, originally built in 1989, include mobility and wheelchair-standard one and two-bedroom flats, offering residents their own privacy and living space while still providing them with all the reassurances and benefits of community living, accessibility, safety and security.
The client called on Stannah’s expertise to advise them on the best course of action to ensure the lift would be an accessible, reliable and safe form of vertical transport for its residents for many more years to come.
The result
The West Midlands and Mid Wales service branch undertook the electrical and builders work, along with full lift test and commissioning. The team of three engineers and one project manager undertook the following refurbishment tasks:
Performance upgrades, including a new hydroware system, rupture valve, hoses, ram seals and suspension ropes.
Car door and interior upgrades, including new car door entrances and door operators, stainless steel landing entrances and the refurbishment of the entire car interior.
Essential communication upgrades, including a new full autodialer emergency communication system with a new GSM, managed through the Stannah Managed SIM service offering.
Engineer safety upgrades, including improved car top protection, shaft lighting and pit protection.
The lift car had been given a complete facelift, with new vinyl skin plate floors, stainless steel skirting, car operating panel and handrail, white vinyl skin plate walls and new modern lighting to give the car a fresh, modern feel. This also included a folding tip-up seat to make travel easier for lift users with limited mobility, which was an ideal addition as the folding seat does not occupy valuable lift floor space or add much additional weight to the lift.
The Stannah family have been making lifts of all types for over 150 years, and as part of our Stannah promise, we work hard to ensure the safety of our passengers at all times. We believe in making life easier and helping people to get on with their lives.
References
[1] Savills, “Spotlight: UK Senior Living”, 21 February 2022
For more information on Case Study: Ensuring independent living with a refurbished lift talk to Stannah Lifts
Enquire Now
List your company on FindTheNeedle.