
Sign In
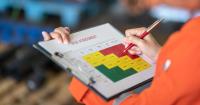
A manual handling risk assessment is a document that details all the different types of manual handling tasks and the risks of injury that they could cause to your employees. Not only is it a legal requirement to complete this risk assessment, but it is also a highly valuable way of preventing costly accidents and injuries to your team and ensuring their safety and productivity.
Did you know that in 2022, 7.3 million working days were lost in the United Kingdom due to musculoskeletal injuries? Annually, this type of injury accounts for more than a third of all injuries reported to the Health and Safety Executive (HSE). Most of these work-related musculoskeletal disorders affect the upper limb or neck (37%) or the back (42%), with the remaining 21% of cases affecting the lower limbs. Read more about the risks associated with manual handling and how to prevent them here.
What are your responsibilities as an employer?
Unfortunately, injuries can still occur through manual handling tasks, even when individuals know the correct lifting techniques and their physical limitations. This is where the Manual Handling Operations Regulations 1992 (MHOR) come in, to try and prevent as many injuries as possible.
As an employer, under the regulations, you are required to:
Avoid the need for manual handling as far as reasonably practicable
Assess the risk of injury from any manual handling that cannot be avoided
Reduce the risk of injury from manual handling as far as reasonably practicable
Failing to meet these responsibilities can incur heavy health and safety fines, especially if an accident or injury should occur. Once you’ve completed your risk assessment, you should also make sure that you provide everything that may be required to reduce risk, such as the following measures:
Find ways to avoid your employees carrying or lifting heavy loads whenever possible.
Ensure staff are provided with adequate equipment to reduce potential injuries from manual handling. This could range from protective personal equipment, such as protective footwear and gloves, to mechanical aids such as microlifts and trolley lifts that protect your team’s health and safety and allow them to work more efficiently.
Never allow the use of any work equipment without proper training, certification or authorisation.
Train your staff regularly to ensure they know how to prevent injuries and accidents, and what to do if they do occur.
How to get started with the risk assessment
So, if you are legally required to complete a manual handling risk assessment to mitigate the risks for everyone, where do you start, and how do you go about it?
Stannah has compiled a free to download Manual Handling Guide to provide useful information for employers regarding the Manual Handling Regulations and demonstrates how the installation of various types of lifts can help to mitigate the risks of manual handling.
In addition to detailed health and safety information about the risks of manual handling and correct handling practices, the guide also contains a free template to help you complete your manual handling risk assessment.
Material transport helps staff manage cargo, speed up productivity and helps to establish a safer working environment. Lifting aids are used in any sector manual handling work is required, such as retail shop floors, warehouses and factories, back of house locations, construction, distribution and disposal of any types of materials etc.
How to use the Guide
When preparing your manual handling risk assessment, the Manual Handling Guide will help you document each type of manual handling task your employees may have to carry out and how to identify high risk activities. You will need to consider the types of loads they will need to move, the environment they will need to move around while carrying out manual handling tasks, and each person’s individual carrying capabilities based on their gender, height, and any pre-existing health conditions or disabilities they may already have.
Example
Let’s look at the example of food and beverage employees working at a bar. They will often need to accept deliveries which may include bulky and heavy items such as kegs, crates or barrels. To complete the risk assessment, you will need to consider some of the following questions:
Do these items need to be picked up from the floor and hoisted to waist height?
Is there a repetitive strain on the body from carrying out this task?
Could any of the loads be hazardous such as hot beverages or foods on a tray, or cleaning chemicals?
Do the goods need to be carried across a potentially slippery surface?
Do the goods need to be moved up or down stairs?
Are any of your staff pregnant, have a known health condition or limited mobility?
How to resolve the issues identified
Now you’ve completed the assessment, the next step would be to identify the risks, and find suitable ways of mitigating the risks to your team. Risk mitigation methods might include:
Providing two or four wheel trolleys to staff for heavy loads
Installing a microlift or trolley lift to efficiently and safely move loads between floors
Secure placement of non-slip coverings on floors where slip or trip hazards have been identified
Using heat-proof, non-slip serving trays with raised sides to prevent spillage of hot items
Ensuring that any staff with existing health conditions are not expected to move loads above their medically recommended lifting capacity
Ensuring that regular training is provided on correct procedures for manual handling
Ensuring that safety procedures and related documentation are easily accessible to all staff, and that health and safety signage is put on display where needed
It is worth noting that employees also bear a responsibility to avoid potential injury. They must use the protective equipment and mechanical aids provided and follow all the procedures put in place to protect their health and safety.
If your team needs to move loads across different levels of a building, installing a service lift or goods lift can significantly help improve efficiency and productivity, most importantly, make the workplace safer.
For more information on How to complete your manual handling risk assessment talk to Stannah Lifts
Enquire Now
List your company on FindTheNeedle.