
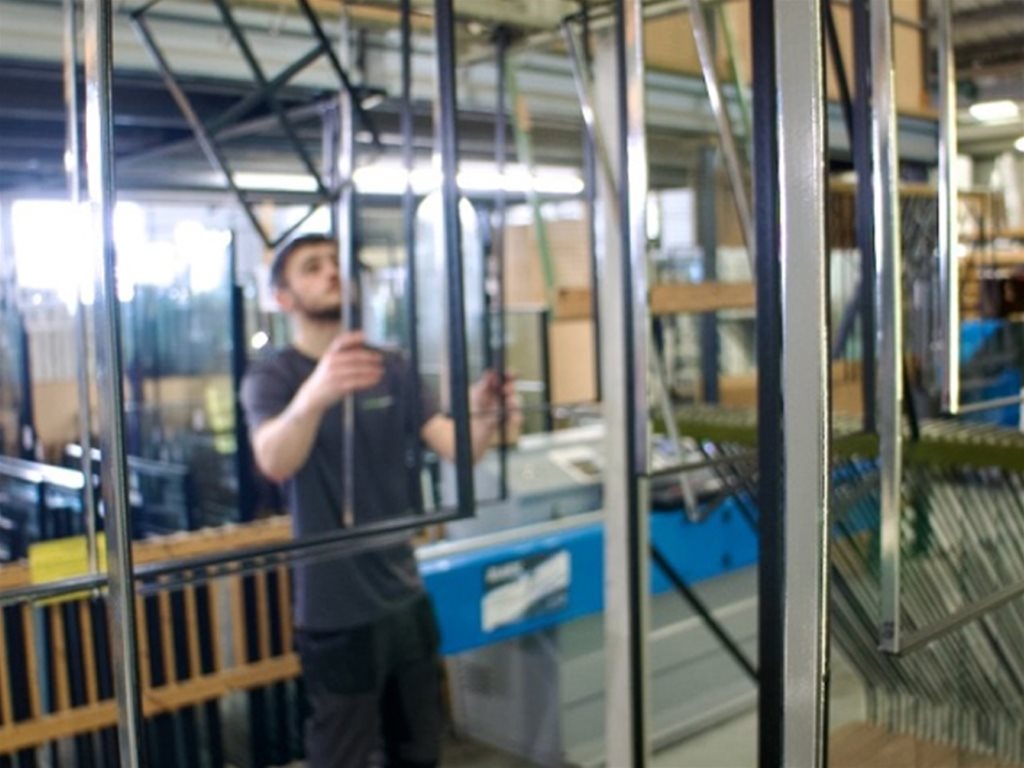
Partnering with the right component supplier can help you avoid common pitfalls, argues Thermoseal Group’s Sales Director Mark Hickox.
The almost wholesale shift from aluminium spacer bar to warm edge spacer bar was crucial to the industry’s success in improving the thermal performance of windows and doors over the last 20 years.
Significantly, warm edge spacer bars like Thermobar and Thermoflex from Thermoseal Group have helped windows and doors meet the requirements of Part L of the Building Regulations, which have required ever-lowering U-values.
Thermobar and Thermoflex warm edge spacers are both certified by the Passive House Institute (PHI). Thermobar is certified with a phA rating (phA+ with hot melt) and Thermoflex is certified phA+. The certificate indicates that these spacers fulfil high energy efficiency and hygiene requirements for an ‘Arctic Climate Region’ and all other climate regions with lower requirement.
Without the right training and support from your warm edge supplier, units are put at greater risk of failure, according to Thermoseal Group’s Sales Director Mark Hickox.
“With a move from aluminium spacer to warm edge spacer, we saw a new phenomenon occur where people underfill with desiccant,” he says.
“It’s not intentional. It’s just that the people in production think they should fill a long and a short side, but what they’re not taking into account is the fact that the internal dimensions of the spacer are different.
“The wall thickness is greater on the warm edge tube – and this goes for all warm edge spacers, not just Thermobar. To get the same lifespan as when you were filling a long and a short before, you need to fill two longs and a short side with most warm edge spacer bars to arrive at the same amount of desiccant that you would have put in an aluminium unit. The airspace is just the same.”
Mark points out that the moisture penetration through the edge sealant into the sealed unit is the same for Thermobar or aluminium spacer, which has been verified by Thermoseal’s in-house laboratory.
“We have extensive testing equipment at our production facility at Wigan,” Mark says, “which was set up so that we could not only understand the pressures on IGU component parts, but that we could fully guarantee our products in real world conditions.
“We tested our desiccant by putting it in our cycling cabinets. We have one set up to do EN1279 Part 2, and a second one dedicated to high humidity cycling. This saturates units day after day, so we know exactly what is required of our products.”
All of Thermoseal Group's desiccant is continually batch-tested and benchmarked against other market-leading molecular sieve desiccants, and every shipment is tested and delivered with a Certificate of Analysis.
The comprehensive testing checks: gas desorption (a premium desiccant will only adsorb moisture vapour and not inert gases in the sealed unit); Delta-T results (generally, but not conclusively, an active desiccant will generate heat upon contact with moisture); initial moisture content (should be less than 1.7%); total and available moisture adsorption capacity (tested to revised to EN1279-4 standard); dust content (to check consistent bead size); and bulk density (to check volume).
“Desiccant is actually one of the cheapest components of an IG unit and also one of the things you can make the biggest shortfall on,” Mark says. “You can have the best sealant in the world, but if you don’t put something in there to absorb the moisture that will pass through it over the unit’s lifetime, it’s going to fail and it’s really not worth cutting costs on it.
“We also test our desiccant in conjunction with the other components in a unit – such as Thermobar, sealant, corner keys and cloth tape – so if you buy the full system from Thermoseal Group, you can be assured that they are all compatible, without risk of failure.”
For more information on Did we say that we test all our products in house? talk to Thermoseal Group Ltd