
Sign In
FLOW MEASUREMENT IN THE LABORATORY
11-03-2020
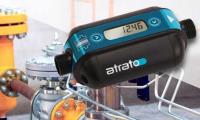
Flow measurement in a typical laboratory or pilot plant posses some unusual problems. Inevitably the pipes are small and the flow rates low and these factors introduce some unique problems. The low energy available from the fluid and the miniaturisation of flowmeter components are the most obvious but the fluidic considerations can also be daunting. For flow in a pipe or tube, the Reynolds number (Re – see Figure 1 below) is a dimensionless, mathematical term which takes into consideration density, viscosity, velocity, pressure and various other operating parameters. Apart from laminar flow meters, which rely on measuring fluids with low Reynolds numbers, most traditional turbine type flow meters require turbulent flow which equates to higher Reynolds numbers. Figure 1. The Reynolds number Low flows therefore usually equate to laminar flow and the relative characteristics of the fluid are more like treacle that water. Probably the earliest successful low flow metering technology was a vertically mounted ball in a clear tapered tube (see Figure 2 below). This works well at both high and low Reynolds numbers. In this type of meter a ball, or shaped float, is fitted to a tube with a bore which changes its cross sectional area up its length. The float rises up against a calibrated scale on the tube as the flow increases. Due to the low energy in the system gravity is used as the reactive force against the float along with the relative buoyancy of the float and the viscosity and density in the fluid being metered. Obviously if the viscosity or density of the liquid changes so the drag or lift on the float setting a limitation on the accuracy of this type of meter. For best performance these meters have to be calibrated and used in their actual operating conditions as tiny changes in the operating conditions give a disproportionate change in the flow reading. Typically these meters do not give an output for remote instrumentation or totalising. Some variable area meters use a spring as the reactive force and magnetic followers to an external indicator. These features permit the meters to be used in any attitude with opaque fluids and potentially high pressure lines. Figure 2. A vertically mounted ball in a clear tapered tube. Typical target applications: Low cost local indications of non-opaque fluids. Another early flow meter development was a differential pressure (?P) meter which used a laminar flow element. Most differential pressure flowmeters require fluids with a higher Reynolds number to work efficiently. At Reynolds numbers below around 2000 the flow is termed laminar. The easiest way to visualise this is to image a tap on your kitchen sink being opened. At low, laminar flows, the water is clear like an icicle. When the tap is opened further the water becomes turbulent and rough in appearance. When liquid is flowing in a conduit with turbulent flow the pressure drop along a length of pipe can be shown to be related to a square law i.e. the pressure drop quadruples for every doubling of flow rate. With low Reynolds numbers the pressure drop is linear with flow rate. Laminar flowmeters use this phenomenon by deliberately creating these linear elements with a pressure drop that can be easily measured and the differential pressure reading is directly related to the throughput. Positive displacement (PD) flowmeter technology exploit the high viscosity of fluids. Varieties of positive displacement flowmeters (see Figure 3 below) include gear, oval gear, nutating disc, screw, piston, oscillating piston or one of a new generation of wobbling diaphragm meters. A PD meter is a type of flowmeter that requires fluid to mechanically displace components in the meter in order for flow measurement. PD meters are best suited to measurement of more viscous lubricating fluids but some will operate with non-lubricating fluids providing there are no particles which can jam the meter. As the viscosity tends to be high the pressure drop often is high as well. These meters produce signals which can be used for remote outputs but operational resolution is usually relatively low as the smaller the meter the larger the relative leak path and the lower the operating efficiency so employing a positive displacement meter design often is a compromise. Figure 3. Oval Gear positive displacement meters. Target applications: high viscosity fluids. Conventional axial turbine flowmeters (propeller in a pipe) are often not suitable for low flows because they work best with turbulent flow. Small axial turbine flowmeters are also sensitive to changes in any part of the system particularly viscosity and bearing drag. By comparison – Radial flow turbines, often described erroneously as Pelton wheels, are much less affected by system changes and consequently can be designed to operate across the laminar/turbulent boundary. Radial flow turbine meter devices (see Figure 4 below) usually use a lightweight flat bladed turbine mounted on low friction bearings similar to the ones found in a large watch. They have a jet of liquid squirted at the plain face of the blade. This causes rotation of the turbine. Figure 4: Radial Turbine Flowmeter. Target applications: Low flow low viscosity liquids. Drawing upon the known limitations of the above metering technologies – engineers realised that the only way that very low flows could be measured accurately was to inject some energy into the system and not disturb the flow too much. This was achieved by the following technological developments. Thermal flowmeters (see Figure 5 below) were the first low flow meters, of which there are two main types. Thermal dispersion meters operate by measuring how liquid flow removes heat from an element proportional to the flow rate. Often this is not very accurate. The second thermal method uses two or even three elements. One element is used for reference temperature measurement. The second is a heat source and the third measures the heat dissipation and so the flow rate. These are mass flow devices and are capable of measuring very low flows although the thermal characteristics of the liquid must be known for precise measurement. Figure 5: Thermal flowmeter (multi element). Target applications: Micro flows and flow control. Coriolis meters were a second type of flow device that was developed for measuring low flows. Coriolis meters still use moving parts but only minutely and outside the flow tube. Coriolis flowmeters use the fact that fluid accelerated around a bend will cause a reaction at ninety degrees to the fluids movement. Such meters are very sensitive and will meter very low mass flows extremely accurately – however they typically are also relatively expensive limiting their use. Target applications: Micro flows and flow control. The most recently developed and broadly effective low flow measurement devices have been based upon ultrasonic technology (see Figure 6 below). Using ultrasonic meters – flows as low as 0.25 millilitres per minute have been measured in trials in Titan’s development lab. Ultrasound, which is injected with the direction of flow into the fluid by one transmitting sensor is received by a second sensor further down the tube. The second sensor then sends a ping back against the flow to the first sensor. As one pulse is accelerated by the velocity of the fluid and second retarded the difference in the flight time is twice the fluid velocity. As the flowmeter tubes dimensions are known the volumetric flow can be calculated. Figure 6: Ultrasonic flowmeter. Target applications: All liquids that require measurement but at competitive prices. Conclusion: As with many measurement technologies, no one technique is optimum for all laboratory applications. For a more in-depth review of low flow measurement techniques – Titan Enterprises has written an informative illustrated guide to help simplify the process of identifying and selecting the best type of small bore flowmeter (< 0.5-inch / 12.5mm) for a range of lab applications. For further information on flowmeter systems for use in laboratory applications please visit www.flowmeters.co.uk or contact Titan enterprises on +44-1935-812790 / trevor@flowmeters.co.uk. NOTE: This article was first published in Labmate UK & Ireland, Volume 39, Issue 9.
For more information on FLOW MEASUREMENT IN THE LABORATORY talk to Titan Enterprises
Enquire Now
More News
List your company on FindTheNeedle.