
Sign In
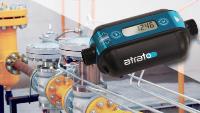
For over 40 years – Titan Enterprises has strived to make smaller and better flowmeters, ranging from miniature turbines and gear meters through to more recently ultrasonic devices. As with any product development when considering miniaturising a flow device there will be benefits as well as trade-offs to consider. In this article we look at the considerations for turbine, oval gear, ultrasonic and thermal flowmeters. A: Turbine Flowmeters Making a very low flow, high performance turbine meter is always going to be a challenge. There are a whole range of physical issues preventing you from producing small devices. Generally radial flow turbines are better for low flow applications than axial flow turbines. In no particular order, the main problems include: i. Friction. Stiction, which can be defined as the friction on two surfaces which prevent the parts being in motion is the first problem. This effect on any bearing will determine the point at which a turbine starts rotating. With a large turbine it is generally not a problem as you are likely to have a large driving torque relative to the stiction. On a miniature device the available driving torque compared to the stiction is greatly reduced. Just getting the bearing spinning freely can be a challenge. This is often overcome with sapphire bearings but again the contact area of these highly polished surfaces can still be relatively high. A point contact offers the lowest friction and is possible with ball or cone bearings. The problem then becomes bearing load. A single point contact equates to an infinitely high bearing load which reduces bearing life. Stiction itself will also depend on the mass of the turbine. ii. Weight. The mass of the turbine in the fluid not only effects the stiction it also has a consequence on the response time. The greater the mass the slower the response time. A turbine with minimal mass could be of a similar density to the fluid that is being metered so that it possesses neutral buoyancy. There is also a trade-off here between turbine diameter, blade width / thickness, materials of construction and detection method. The larger the moment on the turbine from offset of the incoming jet, the stronger the driving force. But if the mass and rotational resistance is higher then so is the drag on the other non-driven blades. Very fine blades can be hard to detect optically and the blade width is restricted to the diameter of the incoming jet plus some incoming jet “spreading” distance within the fluid. Too narrow, and much of the fluid will spill around the side, but too wide and unnecessary drag will occur. iii. Detection system. A no-drag system is essential and optical is ideal providing you have a fluid which transmits the light effectively. It can be reflective or more often some type of beam cutting arrangement. Adding magnetic material to the turbine for a zero drag inductive, magnetic or Hall Effect detector increases the mass but enables the flowmeter to handle opaque fluids such as emulsions. For such applications there is a trade-off between magnetic elements, their size and mass. iv. Fluidics. As flow rates become lower, the more liquids look and behave like treacle. Turbines become viscosity sensitive as they are primarily Reynolds number devices which are happier with turbulent flow. We try to negate some of these effects with fluidic tricks such as the induced secondary vortices which behave like “roller” bearing which reduce viscous drag and extend the linear flow range. v. General mechanics. This is a catch-all section and hard to quantify. There is a relationship between turbine diameter, jet offset and size as well as turbine and chamber thickness and clearances. It is a delicate compromise between these elements. B: Gear flowmeters. At Titan Enterprises we opted to incorporate the oval gear design into our gear meter products, as there is a much greater driving torque for a given differential pressure which is derived from fluidic asymmetry of the gears. There are fewer subtleties in the design options on oval gear flowmeters, in comparison to radial turbines, because of their basic operating principles. Oval gear flowmeters operate on the principle of positive displacement, by taking a parcel of fluid and transferring it from the inlet side to the outlet side without any leakage. This sounds very easy but there is a trade-off between gear clearance, leakage, friction and fluid viscosity. a. Clearance and Leakage. Make the clearances small and you can meter low viscosity fluids very accurately over a large flow range. Make them too large and the flowmeter will not work well until the liquid is highly viscous. As an oval gear flowmeter is made smaller, the leak path becomes proportionately larger. If we take one of our smaller oval gear flowmeters and straighten out the leak path it can be defined as a strip some 60mm long by the clearance between the gear and the chamber. We would normally run that clearance at 0.03mm which gives a potential leak area of 1.8mm2 This is equivalent to a round hole nearly 1.5mm diameter. If you halved the size of the gears in all directions the leak path would become essentially half so still nearly a 1mm hole for a square-law reduction in gear size and efficiency. Bigger oval gears are easier to manufacture as they are more efficient at, relatively speaking, lower flows. b. Friction. If there is stiction an oval gear flowmeter will not start. If there is running friction the linearity will not be good. Like mini-turbines, friction must be kept to a minimum. However, there are fewer options with oval gear flowmeters as the bearings loads can be quite high. This is because the load induced by the meter’s pressure drop (which is necessary to work the meter) becomes problematic at higher flows. c. Fluid Viscosity. The fluid viscosity is fundamental to the performance of oval gear flowmeters. Most are not very happy with non-lubricating low viscosity fluids such as water. However, we can minimise problems through selection of high-quality materials and precision manufacture. For example, hot water has a viscosity around 0.6 Centipoise which is very happy slipping through that theoretical clearance equivalent of a 1.5mm diameter hole without rotating the gears unless the mass of the gear is low, the friction minimal, and the clearances as tight as possible. A very small increase in viscosity (and usually lubrication) makes a vast difference to the efficiency of an oval gear flowmeters performance. C: Ultrasonic Flowmeters. We are targeting this area of technology as providing the best solution for our many of current low flow developments. For the two technologies outlined above the pure mechanics of these systems is the limiting factor. Some energy needs to be injected into the system to achieve lower flow rates. There are also some problems to solve when producing low flow ultrasonic devices due to the sheer physics of the technology. 1. Basic physics. Time of flight ultrasonic meters work because sound speeds up when it travels with the flow and is retarded when it travels against it. Effectively the phase shift between these two signal transit times is twice the velocity of the fluid in the pipe. The lower the flow rate the lower this phase shift or time of flight in each direction becomes. 2. Reduced bore sizes. Decreasing pipe diameter accelerates the velocity so increasing the phase shift between the upstream and downstream signals. Getting the ultrasonic signal into these smaller pipes is itself a problem. On our lowest flow Atrato ultrasonic flowmeter we inject and receive the ultrasound signal into a 6mm diameter bore but then reduce the pipe to a 1mm bore in the central section between the crystals to accelerate the liquid and increase the velocity. This comfortably permits us to meter flows down to 2ml/min. 3. Future developments. We are working on even lower flow devices by utilising one of the unique features of our patented technology. We can send ultrasound around corners. We have successfully prototyped a device which effectively is a 300mm long 1mm diameter tube but produced in a 30mm diameter coil. The basic physics of this unique design increases the pathlength which significantly increases the difference between the up and down signals. However, there are also trade-offs with this design. The signals are seriously attenuated in such a long tight bore so signal to background noise ratio increases accordingly. This effectively dictates our flow range and low end flow capability. There is currently a point at which we start to lose efficiency with greater increased length and do not see any decrease in low flow measurement. Currently 0.25ml/min is the lowest flow we have successfully measured in the laboratory but improved electronics, algorithms and ultrasound coupling is likely to lower this threshold further. D: Thermal Technology Flowmeters. These inherently mass flow devices are also becoming smaller with faster response times. By definition (unlike the flowmeter technologies outlined above) they can only handle specific fluids as the thermal transfer characteristics of each fluid changes the calibration of the device. Thus, a flowmeter set-up for one liquid would not accurately meter a second without a change in calibration factor. Currently for equivalent devices they do not perform with the same accuracy as our ultrasonic technology, but they do meter much lower flows. Conclusion: Fast paced developments in miniaturising flow sensors is opening the way to measurement of flow in applications such as medical devices that would have previously never been thought possible. To discuss development of a micro flow measurement device optimised for your application please contact us on +44-1935-812790 or sales@flowmeters.co.uk.
For more information on Flowmeter Miniaturisation – Benefits & Trade-Offs talk to Titan Enterprises
Enquire Now
More News
List your company on FindTheNeedle.