
Sign In
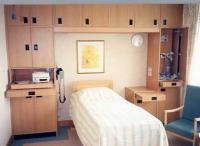
Dixon Timber Products, a major supplier and installer of made-to-measure storage furniture and reception counters to the National Health Service, is achieving improved manufacturing efficiency and cost-savings with its new Striebig Evolution vertical panel saw.
Benefits include an improved quality of cut with sustained accuracy, a cleaner working environment and sharply reduced saw resharpening costs.
The Doncaster business was set up 12 years ago by managing director John Dixon to serve the medical furniture market. It’s now one of the main players in the highly competitive sector.
Operating out of a 14,000 ft workshop, it manufactures and installs a wide range of panel-based products at hospitals and primary care centres throughout the UK. It has also supplied hospitals in Ireland, the Middle East and Africa.
Its wide product range includes specialist catheter and endoscope cupboards, reception counters and nurses’ work stations, wardrobes and bedside units, vanity units and toilet cubicles.
With around 80 per cent of its output going into the medical sector, the remainder is specified for schools, universities, hotels, retail outlets, factories and offices.
The company is founded upon a wealth of experience, answering the needs of hospitals, architects and contractors alike and offering high quality, high value-in-use products. Demonstrating this, its quality management system has been certified to ISO 9001:2000
Its Striebig Evolution 6224 replaced an elderly wall saw. It’s the largest in the Evolution series with a maximum cutting area of 5,300 mm x 2,240 mm and a maximum cutting depth of 80mm.
It represents the cutting edge in vertical panel saw technology. Features considered expensive optional extras in other saws are included as standard, such as a digital measuring system, accurate to 0.1 mm, and an adjustable precision display that can be set to an accuracy of 1.0, 0.5 or 0.1 mm, according to the thickness of the panels being sized.
Numerous automatic procedures carried out by the press of a button include locking and releasing the beam saw, setting the horizontal cutting height, plunging and swivelling the motor, locking the support rollers during sawing and fine saw blade adjustment.
The saw is used throughout the day to cut MFC, MDF, laminates and solid surfaces up to 20 mm thick, and up to 38 mm thick chipboard panels used for worktops.
It was supplied by Striebig’s exclusive UK agent, T.M. Machinery Sales, with an optional scoring use that delivers perfectly smooth cuts on MFC and melamine-faced MDF panels.
T.M. also provided an optional angle cutting unit, which is easily attached to the left or right of any vertical cutting point. Adjustable to 1/10th of a degree, it can be locked into place and is for use with panels up to 42 mm thick, producing angle cuts which are totally clean and accurate.
It also supplied an Alko Mobil Jet 140 H mobile dust extraction unit for use in conjunction with the Evolution’s highly effective built-in TRK extraction system.
After Dixon Timber Products decided to replace its oldest saw, John Dixon involved workshop supervisor Colin Crawshaw and operator Ricky Scott in the selection process and together they looked at several possible suppliers.
John Dixon said: “T.M. arranged for us to see a Striebig in use at a Stockton woodworking company and it was Colin’s and Ricky’s favourable reaction that ultimately influenced the decision to purchase. After all, they are the people who have to use it on a daily basis.
“We consider the Evolution an extremely high quality product with all the features we need, and it is by far the more robust and solid of all the saws we looked at. It’s not the cheapest on the market, but we are prepared to pay for quality to obtain the best and most long-lasting production equipment there is.
“The people at T.M. were extremely helpful. They suggested the most appropriate model for our specific needs and provided an excellent service from quotation stage through to installation and commissioning.”
Colin Crawshaw said: “The Evolution is a great saw that’s very easy to use. We particularly like the digital readout with its fine adjustment facility and the ease of loading panels due to the metal roller system.
“It gives terrific quality in terms of accuracy and smoothness of cut time after time. Before, we often had to make multiple cuts until we were satisfied with the results and were considering replacing our edge bander with one with a pre-milling facility. We can now put the cut panels straight on to the edge bander.”
The angle cutter is also proving a huge plus. T.M’s engineers modified the standard unit to meet Dixon Timbers’ requirements so that it can cut in two directions. Jigs were previously made up and put on a CNC machining centre for any angle cutting needed.
“The saw’s extraction is superb,” said Mr Crawshaw. “A combination of the dust and chip collection points within the saw and the Alko mobile extractor has resulted in a totally clean working area.”
Said Mr Dixon: “The Striebig has allowed us to make substantial efficiency gains, plus considerable savings on the cost of blade resharpening. It’s very labour saving because having a guaranteed quality cut every time means we now don’t have to do any repeat cutting, and there’s less material wastage.”
For further information contact Matt Pearce, Sales Director on 0116 271 7155 or email sales@tmservices.co.uk
Issued by Stephen Barry Publicity. Tel: 020 8341 6660. Email: stephenbarry@clara.co.uk
For more information on Furniture Maker - Striebig saw delivers healthy benefits to hospital furniture maker talk to TM Machinery Sales
Enquire Now
More related to Furniture Maker - Striebig saw delivers healthy benefits to hospital furniture maker
List your company on FindTheNeedle.