
Sign In
LOLER in easy steps
19-11-2019
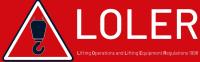
As a lifting equipment owner this guide will provide you with some basic information about the legal requirements of the Lifting Operations and Lifting Equipment Regulations 1998 (LOLER). It is important to note that this is a basic overview and it is important that you familiarise yourself with the Regulations and accompanying Approved Code of Practice.
What is LOLER?
LOLER aims to reduce the risks associated with the use of lifting equipment at work. In addition to meeting the requirements of LOLER, your lifting equipment is also subject to the Provision and the Use of Work Equipment Regulations 1998 (PUWER).
LOLER requires that your scissor lift at work is:
Strong & stable for the stated use
Positioned & installed to minimise risks
Used safely, work in planned, organised, & performed by competent people
Examined thoroughly & inspected by competent people on an on-going basis
What types of lifting equipment is covered by LOLER?
LOLER covers all types of equipment used at work used for lifting & lowering loads these
include:
Scissor lifts
Goods lifts
Mezzanine floor lifts
Loading Bay lifts
Work positioners
Cranes
Fork-lift trucks
Hoists
Mobile elevating work platforms
Vehicle inspection hoists
What is not covered by LOLER?
Not all types of lifting equipment used in the workplace is covered by LOLER, the following lifting equipment is covered by the more specific legislation – The Workplace (Health, Safety & Welfare Regulations 1992.
Escalators
Equipment that is used primarily by members of the public e.g. lifts in shopping centres
What are my legal requirements under LOLER?
Under the Lifting Operations and Lifting Equipment Regulations 1998 (LOLER) you are legally required to:
Ensure that the lifting equipment (Scissor Lift) is suitable for the proposed lifting task.
The lifting equipment (Scissor Lift) is installed and/or positioned so to prevent the risk of injury from the lifting or the load falling & striking someone.
The lifting equipment is sufficiently and visibly marked with any information required for safe use.
Any accessories needed in the use of the lifting equipment should be similarly marked.
That all lifting operations using lifting equipment covered by LOLER are planned and carried out by competent people.
If lifts are used for lifting people, as in the case of Mezzanine Floor Lifts, instructions for use are made clear and all precautions are taken to reduce risk.
What records does LOLER require?
As part of a thorough LOLER examination the inspection officers may ask to see the following records:
The manufactures handbook & any Declaration of Conformity
Records of any maintenance work or repairs carried out on the lifting equipment
Previous records of thorough examinations (2 years)
Staff Training records
Risk Assessment records
What is a LOLER thorough examination?
The regulation requires that all lifting equipment covered by LOLER including scissor lifts are regularly inspected by Health & Safety Inspectors. LOLER thorough examinations are also sometimes referred to as a Statutory Thorough Examination (STE).
Thorough examinations are carried out to assess the rate of deterioration of the scissor lift
and it also identifies any defects that may have occurred. The examination also certifies that the lifting equipment is safe for continued use until the next inspection.
It is important to note that NO maintenance or repair work is carried out during a
thorough examination.
LOLER requires that thorough examinations are carried out regularly. This is defined as at least every 6 months for lifting equipment or accessory for lifting persons such as Goods Lifts or Loading Bay Lifts and at least every 12 months for all other lifting equipment covered by LOLER.
If you do not carry out a LOLER thorough examination, you could be subject to legal action including fines in a court of law.
Should I get my scissor lift serviced regularly?
YES.
As thorough examinations only identify potential deterioration of your lifting equipment
and a fail would result in the lift being decommissioned, it is vital that you service your lifting equipment regularly to ensure a pass.
We recommend that you service your scissor lift tables annually, however if your lifting equipment is under heavy use or used to lift people it is important that you service
your lifts every 6 months.
IMPORTANT:
You are legally obliged to maintain your lifting equipment in a safe, good and workable condition. In addition, you need to be able to demonstrate this via records to the enforcement authorities.
Failure to do this could result in enforcement action including prosecution, even if no accident has occurred.
For more information on LOLER in easy steps talk to Translyft UK Ltd
Enquire Now
List your company on FindTheNeedle.