
All You Need To Know About Pallet Racking
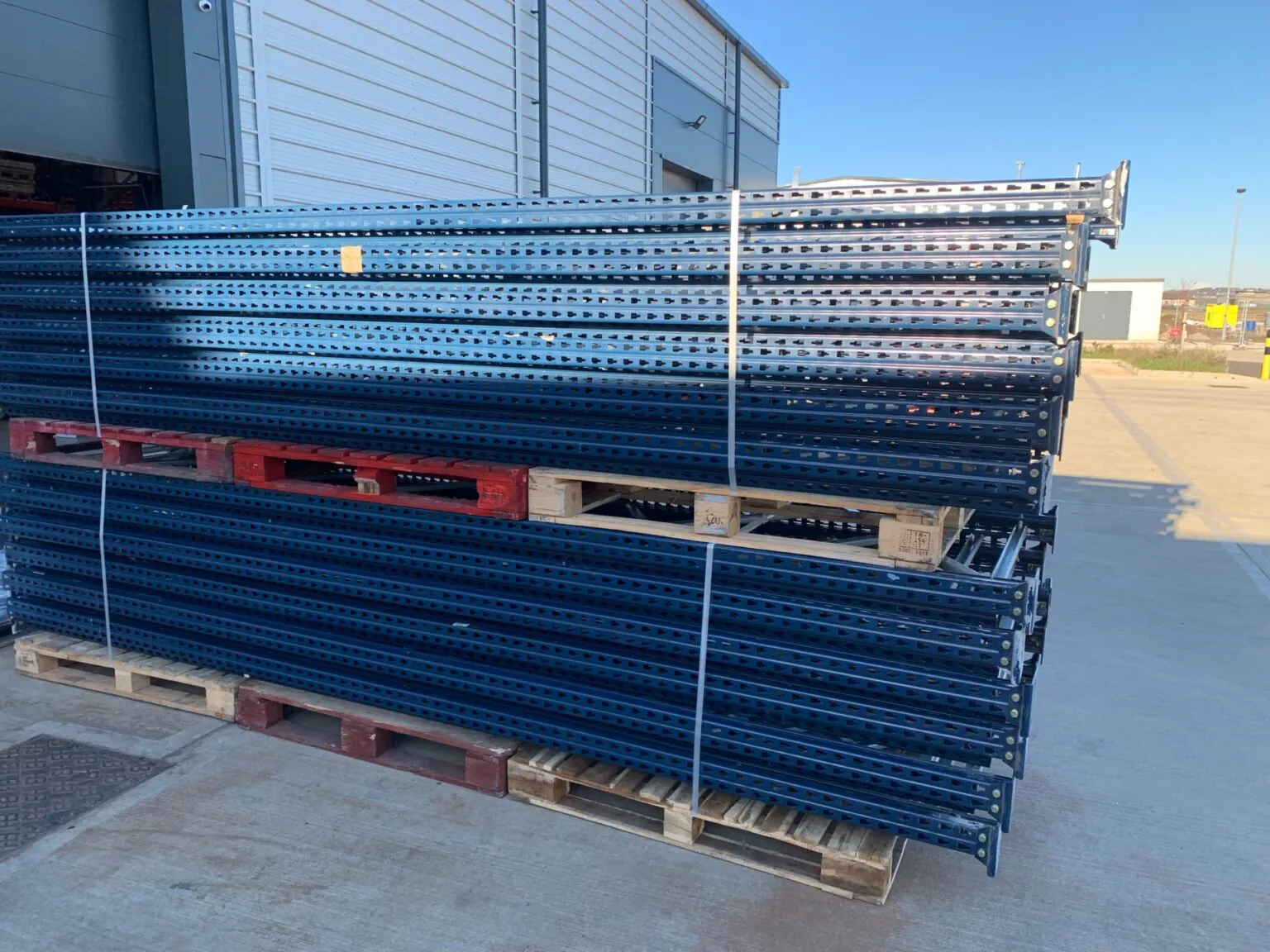
There are three critical components to modern logistics, and all three of which are so ubiquitous that they often do not receive the credit they deserve for shaping the warehouse as we know it today: the electric forklift, the standardised wooden pallet and pallet racking shelving.
Whilst all three components were developed largely independently in the first half of the 20th century, they would rapidly evolve in tandem with each other after the Second World War and the rapid logistical developments that were brought about as a consequence.
However, whilst pallets and forklifts allow for larger quantities of product to be transported more efficiently, pallet racking allows goods and materials to be stored far more efficiently and solves a fundamental problem with scaling up warehouse operations.
Here is everything you need to know about pallet racks, from their purpose, different types of racking, their advantages and the considerations needed to make the most of them.
What Is Pallet Racking For?
Pallet racking is a type of shelving system specifically designed to store goods on wooden pallets, almost invariably used in distribution centres and warehouses, although some big box retailers also use pallet racking systems to store and display products for consumers to buy.
It consists of a series of high-strength horizontal and vertical metal beams to create a support frame that pallets can be directly placed on and taken off of by forklifts to fit the logistical workflow of the warehouse, distribution or fulfilment centre.
What Types Of Pallet Racking Exist?
There are a lot of different forms of pallet racking out there, designed with the optimisation of space and the meeting of storage needs firmly in mind:
- Selective – The most common type, selective racking is made up of a series of adjustable frames and beams that allow a forklift to access every pallet and adjust for product sizes.
- Double-Deep – Similar in design to selective racking, the two-deep system reduces the number of aisles but requires extended-reach forklifts for access.
- Drive-In/Drive-Through – This type of racking allows forklifts to drive directly onto the racks themselves, maximising potential storage density, with the difference being that drive-through racking has an entrance at one side of a bay and an exit on the other.
- Push-Back – An efficient Last In, First Out (LIFO) system, push-back racking loads pallets onto carts that push existing pallets back.
- Flow – Flow racking is a First In, First Out system that loads pallets at one end and uses inclines and rollers to move them from one end of the warehouse to another (typically from loading to picking).
- Cantilever – A versatile system designed for bulkier and longer items, cantilever racks have additional arms extending outward from the columns.
What Are The Advantages?
The reason why pallet racking systems exist in the first place is that they allow for the most optimal and efficient storage of materials possible.
Thanks to the principle of “from the earth to the heavens” found in property law, the most affordable way to expand a warehouse’s capacity is to build as high as you can feasibly store materials, using forklifts to carry goods up and down the racks.
Pallet racks are also adaptable, being able to fit different scales of product and adapt rapidly to changes in the needs of the business, as well as providing a systemic, safer approach to inventory management.
For more information on All You Need To Know About Pallet Racking talk to UK Shelving Ltd