
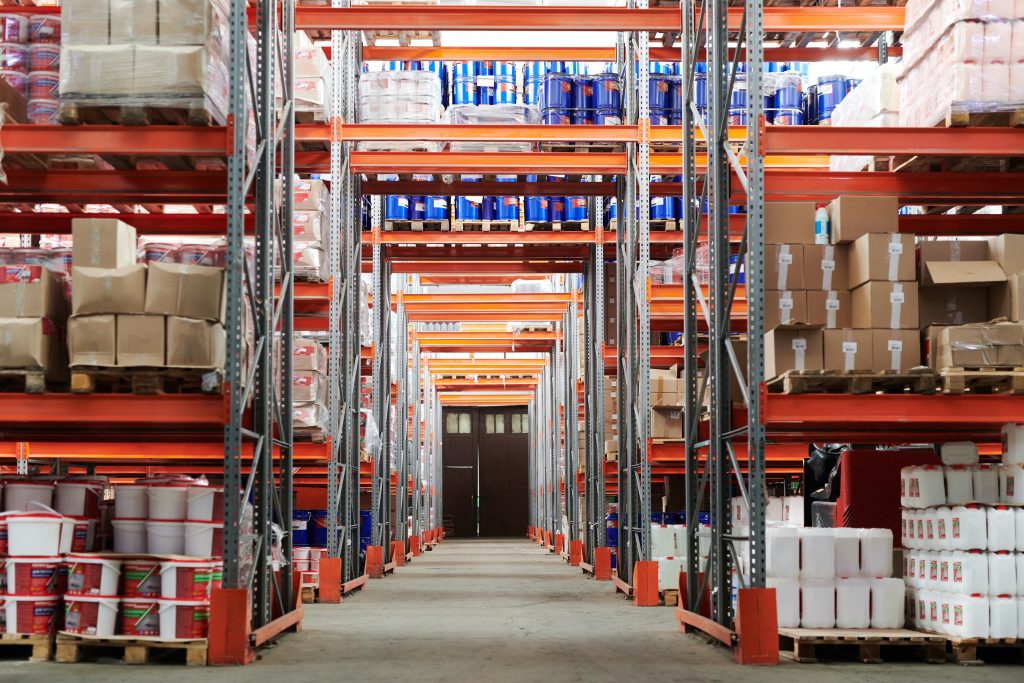
Warehouses can vary wildly in size, shape, scope and workflow, and these will have an effect on basically every element of its design from height to the arrangement of pallet racking and transport routes for forklifts.
Maximising efficiency is everything, as that can be the difference in many supply chains between meeting your daily, monthly or annual targets, or adding extra unnecessary expenses that could prove costly in the long run.
However, whilst in the pursuit of the perfect warehouse arrangement for your business, take care not to make these common errors.
Not Maximising Warehouse Height
Most warehouses are capable of storing far more pallets through effective racking and stacking than many businesses appreciate, and there are two errors that work in tandem to reduce the amount of space you have to work with.
The first is not taking advantage of height. With rack heights that can go up to 15 metres and forklifts that can take pallets that high, the most cost-effective way to set up warehouse systems is to build upwards.
Since it is typically cheaper to buy stronger, higher shelving and build upwards than to buy additional land to expand the storage volume, not taking advantage of every potential square inch of space is a waste.
This is not an immediately obvious mistake until a business looks to expand, and realises they have a lot of unused space that they have to disrupt their current operations in order to take full advantage of the space they already have.
It is better to invest in efficient high shelving now rather than having to start afresh or buy new warehouse space later.
Overly Wide Aisles
Similarly, with the rise of the narrow-aisle forklift in the 1950s, so much more inventory can be fit into the same space than ever before whilst still being readily accessible.
As such, having aisles that are too generously wide, whilst it means you can save money on the forklifts themselves, comes at the cost of losing precious storage space, especially given that it costs more to buy additional land than it does to buy more versatile forklifts.
In both cases, the mistake was not planning for the future, meaning that if you need to expand, your options are expensive relocation or starting from scratch.
Insufficient Loading And Unloading Space
The first and final steps of a warehouse workflow are the most important but also the most neglected processes when it comes to assigning and organising space, and this can prove to be a costly mistake.
The reason comes down to an “out of sight, out of mind” approach to warehouse design, but not allocating enough space for warehouse staff to unload inventory and load goods for delivery to the next stage of the supply chain leads to unnecessary bottlenecks, as well as potential health and safety implications.
Whilst there is no hard and fast rule surrounding warehouse space and shelving, you should try and assign at least a third of your overall inventory space to both loading and unloading, leaving two-thirds for storage, icking and packing to take place.
For more information on Mistakes To Avoid When Arranging Your Warehouse Shelving talk to UK Shelving Ltd