
Sign In
The tool steels that make the tools…
09-05-2014
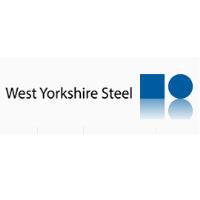
There is definitely a joy in finding something that works well; a simple pleasure in discovering a product that does exactly what it says on the tin. Similarly, it can be equally infuriating when something simply doesn’t work or is unfit for purpose.
However, what happens when the machines that make the machines fail?
Tools and dies are inherently expensive to produce and failures can be doubly so. Not only does it cost to machine replacements, but lost productivity prevents money from coming into the business.
There are many reasons why failures occur but some of the most common have obvious causes.
Potential failures from poor manufacturing can be avoided by taking sufficient care. Always follow the rules of good die design, use the right steel for the job and relieve corners with generous fillets. Machine all surfaces to remove decarburisation and any defects which could impair the final product and take care with all machining and grinding processes.
Cracking on heat treatment can be due to simple over-heating or holding for too long at too high a temperature for the grade or thickness of the steel. Patchy or uneven heating has the same effect. The steel requires careful heating to the correct temperature for the grade before being quenched immediately. Failures in the heating process, quenching at too low a temperature or not tempering immediately after quenching can drastically reduce the lifespan of a tool and leave it vulnerable to cracking.
Similarly, attempting to harden from low heat, quenching too slowly or too high a tempering temperature can leave a steel too soft. Insufficient hardness means the tools are likely to deform under pressure and fail much faster than a correctly treated steel. The same problems will be seen if the decarburised skin is not removed in machining or rough grinding.
Heating should be done with precision and never to temperatures higher than those recommended for the grade or held too long, taking into account the size and shape of the tool. Once the heating is complete, quench to the prescribed heat using an appropriate medium and temper immediately. The higher the tempering temperature, the softer the steel and vice versa, so make sure the hardness is right for the application required and avoid over stressing when aligning in presses.
‘Soft’ materials cause problems and it can be more serious when the problem is localised to a soft spot. These are commonly due to a contaminated quenching medium, a medium which is too warm or when the medium isn’t properly circulated to all the parts which need to be hardened. A hardening furnace that suffers from scale that then causes local decarburisation can have the same effect.
Tools which fracture can not only be costly but dangerous. Fracturing is inherently random and can’t be predicted in either timing or direction. Breakages in this manner usually occur in brittle materials with a coarse crystalline fracture – itself caused by overheating in hardening. Steel which has been hardened correctly but was improperly tempered or became misaligned in the press are at a higher risk of fracturing. Also using too low a grade of steel for the service required causes fatigue, as does accidental overloading and can cause the steel to fail suddenly and spectacularly.
Taking due care and following best practice will avoid many issues and quickly place steel among those items which are a joy to use because they work just as they should.
For more information on The tool steels that make the tools… talk to West Yorkshire Steel Co Ltd
Enquire Now
List your company on FindTheNeedle.