
Sign In
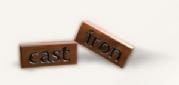
UK Deliveries. Contact our well informed sales team. Cast iron usually refers to grey cast iron, but identifies a large group of ferrous alloys, which solidify with a eutectic. Iron accounts for more than 95%, while the main alloying elements are carbon and silicon. The amount of carbon in cast irons is 2.1 - 4%, while ferrous alloys with less carbon are denoted as carbon steel by definition. Cast irons contain appreciable amounts of silicon, normally 1 - 3%, and consequently these alloys should be considered ternary Fe-C-Si alloys.Despite this, the principles of cast iron solidification are understood from the binary iron-carbon phase diagram, where the eutectic point lies at 1154 ?C and 4.3 wt% carbon. Since cast iron has nearly this composition, its melting temperature of 1150 to 1200 ?C is about 300 degrees lower than the melting point of pure iron. Cast iron tends to be brittle, unless the name of the particular alloy suggests otherwise. The color of a fracture surface can be used to identify an alloy: carbide impurities allow cracks to pass straight through, resulting in a smooth, "white" surface, while graphite flakes deflect a passing crack and initiate countless new cracks as the material breaks, resulting in a rough surface that appears grey.With its low melting point, good fluidity, castability, excellent machinability and wear resistance, cast irons have become an engineering material with a wide range of applications, including pipes, machine and car parts.Cast iron is made by remelting pig iron, often along with substantial quantities of scrap iron and scrap steel, and taking various steps to remove undesirable contaminants such as phosphorus and sulfur. Depending on the application, carbon and silicon content are reduced to the desired levels, which may be anywhere from 2% to 3.5% and 1% to 3% respectively . Other elements are then added to the melt before the final form is produced by casting.Iron is most commonly melted in a small blast furnace known as a cupola (see blast furnace for more details). After melting is complete, the molten iron is removed or ladled from the forehearth of the blast furnace. This process was devised by the the Chinese, whose innovative ideas revolutionized the field of metallurgy. Previously, iron was melted in an air furnace, which is a type of reverberatory furnace. Varieties of cast ironGrey cast ironMain article: Grey ironSilicon is essential to making of grey cast iron as opposed to white cast iron. Silicon causes the carbon to rapidly come out of solution as graphite, leaving a matrix of relatively pure, soft iron. Weak bonding between planes of graphite lead to a high activation energy for growth in that direction, resulting in thin, round flakes. This structure has several useful properties.The metal expands slightly on solidifying as the graphite precipitates, resulting in sharp castings. The graphite content also offers good corrosion resistance.Graphite acts as a lubricant, improving wear resistance. The exceptionally high speed of sound in graphite gives cast iron a much higher thermal conductivity. Since ferrite is so different in this respect (having heavier atoms, bonded much less tightly) phonons tend to scatter at the interface between the two materials. In practical terms, this means that cast iron tends to ?damp? mechanical vibrations (including sound), which can help machinery to run more smoothly.All of the properties listed in the paragraph above ease the machining of grey cast iron. The sharp edges of graphite flakes also tend to concentrate stress, allowing cracks to form much more easily, so that material can be removed much more efficiently.Easier initiation of cracks can be a drawback once an item is finished, however: grey cast iron has less tensile strength and shock resistance than steel. It is also difficult to weld.Grey cast iron's hi
For more information on Cast Iron talk to West Yorkshire Steel Co Ltd
Enquire Now
More products
List your company on FindTheNeedle.