
Sign In
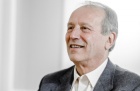
BMW production problems highlight need for OEMs to become better risk managers, says Vendigital’s Richard Gane
Following news that BMW halted production at a number of global manufacturing plants this week, OEMS are being warned to take a more structured and planned approach to managing supply chain risk.
The German car maker was unable to complete the production of new luxury vehicles at plants in Leipzig and Munich due to the under supply of a small but critical component used to make electrical-assisted steering systems. Plants in South Africa and China were also affected by the supply shortage.
Whilst disruption caused by a break in supply is not uncommon in the automotive industry, due to the focus on short supply chains and lean production methods, it is surprising that a high-volume supplier such as Bosch seems not to have adequate dual supply relationships in place. The industry’s reliance on just-in-time deliveries means that the effect of a break in supply can travel up the supply chain extremely quickly; causing substantial losses for OEMs. In this case, a sub-supplier in Italy, which produces casings for the steering component produced by Bosch is thought to be the cause of the problem.
Producing over 17,500 units per week of its 1-, 2-, 3- and 4- Series cars, BMW should expect to suffer losses in excess of €400m as a direct result of the disruption. However, depending on how quickly supplies can be restored, some of these losses could be recouped in just a few months by increasing overtime at its plants.
From a supply chain perspective, most OEMs prefer to establish single supply partnerships for key components such as steering systems and engines, particularly where there is open innovation and shared intellectual property involved. At this end of the supply chain, margins are more likely to have been ring-fenced and supply relationships tend to be more robust and enduring.
Tier one and two suppliers, on the other hand, are used to operating on lower margins where there is little slack in the system to cope with breaks in supply. Suppliers lower down the chain are less likely to have invested in skills and increasing production capacity; adding to the risk of disruption.
Tier one and two suppliers could mitigate the risk of disruption by doing more to change the balance of power in their supply chain relationships. They should be working more closely with suppliers further down the chain to understand the issues they are facing and to ensure they are capable of meeting demands and fulfilling quality standards. As an extra layer of protection, they could also consider dual sourcing where appropriate, so there is extra capacity to utilise if needed.
BMW is one of a series of vehicle manufacturers to have been affected by supply chain disruptions recently. Last year, VW faced disruption due to a dispute over payments with one of its suppliers, Prevent Group. Around the same time, Aston Martin was forced to recall over 6,000 vehicles in the US due to technical problems with its door locking systems.
At a time of geopolitical uncertainty in Europe and the rest of the world, it is increasingly important that OEMs and suppliers collaborate and aim to strike long-term partnerships that are rooted in a deep understanding of the challenges posed by the marketplace. In a world of heightened risk, where levels of demand can’t be relied upon from one month to the next, it no longer makes sense to negotiate hard on price without taking into account the pressure this places on suppliers further down the chain and value needs to be shared more evenly.
If BMW heeds the warning and encourages tier one suppliers to take a more holistic approach to supply chain management, this week’s disruption could be a one off.
For more information on BMW’s production problems highlight importance of closer collaboration talk to Whiteland Engineering Ltd
Enquire Now
More News
List your company on FindTheNeedle.