
Sign In
GETTING TO GRIPS WITH RUBBER PAD FORMING
06-04-2022
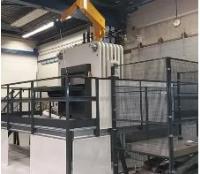
GETTING TO GRIPS WITH RUBBER PAD FORMING
The Workshop Press Company is proud to be one of the country’s leading suppliers of metalworking machinery. We supply a wealth of metal fabrication equipment, including a rubber pad forming press. Moreover, we can accommodate a range of set ups – whether you’re working in a warehouse, a manufacturing factory or something smaller like a workshop. With plenty of experience and expertise under our belts, we’ve created a product selection that aims to support many different manufacturing processes. Read on to find out more about the rubber pad forming process and benefits.
Related: Metalworking Machinery: Motorised Press Or Hydraulic Press
WHAT IS RUBBER PAD FORMING?
So what s rubber pad forming? Contrary to the name, it isn’t to do with producing rubber pads. Actually, rubber pad forming is a type of metal working process. Companies use the technique to produce metal products using rubber pads. Sheets of metal are manipulated into different shapes using the compressive forces of the rubber pads – hence the name.
THE PROCESS
HOW DOES RUBBER PAD FORMING WORK?
Rubber pad forming can be carried out on a wide variety of presses. Such as C-Frame Presses, Workshop Presses, Four Column Presses, Deep Draw Presses, and Production Presses to name a few. Rubber pad forming works by compressing the sheet metal between a die and the rubber cushion pads. The rubber pads are positioned on top of the metal, and the die is located underneath.
Once the stroke cycle is initiated, the press machine compresses the rubber pad onto the sheet metal downward and onto and over the die. As the metal bends, it takes the shape of the die is underneath it. Once the pressure is removed, the elastically deformed rubber springs back to the original shape, leaving the sheet metal formed in the desired product shape.
BENEFITS OF RUBBER PAD FORMING
Rubber pad forming allows manufacturers to safely manipulate the shape of finished or polished sheet metal. Some metalworking processes can damage finished sheet metal. However, rubber pad forming does not due to the fact that the pads are made of a softer material. The metalworking process also supports most types of sheet metal – from stainless steel through to aluminium.
FORMING DIES FOR RUBBER PAD FORMING PROCESSES
One other benefit of rubber pad forming is that the forming dies can be produced quickly and from a variety of materials, and the product shapes that can be achieved are endless. The dies can be easily CNC machined or even 3D Printed which makes rubber pad forming perfect for short runs or prototyping with short lead times. Rubber pad forming is also suitable for mid-quantity production runs. During the process, the rubber deforms the plate over or into the product-specific die.
CONTACT US
The Workshop Press Company has a vast range of knowledge and expertise to support a wide range of requirements. Whether you are a business that knows exactly what they need to invest in, or a sole trader starting out, we can provide you with all the information you need to invest in the right machinery. We support businesses and fabricators up and down the country with our high quality metal fabrication equipment. With plenty to choose from, you’ll be sure to find what you need with us.
If you would like to find out more about rubber pad forming presses then head to our website today. Alternatively, you can call +44 01926 562011 to speak to a member of our helpful and friendly team.
If you have found this blog helpful, you may wish to read a previous blog: Looking For A Hydraulic Press For Sale? Workshop Press Can Help
For more information on GETTING TO GRIPS WITH RUBBER PAD FORMING talk to WorkshopPress.co.uk
Enquire Now
List your company on FindTheNeedle.