
Sign In
HYDRAULIC PRESS APPLICATIONS
02-10-2021
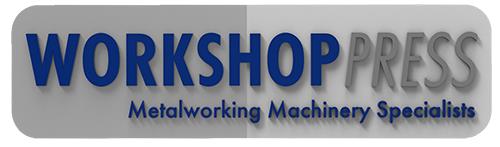
The Workshop Press Company UK offers high-quality standard and custom hydraulic presses, for every application and operation in a wide variety of industries. Every customer’s application consists of a different set of parameters and requirements. Therefore, we supply a wide variety of standard presses. As a result, we address a broad spectrum of pressing operations, for any industry with common pressing processes. In addition, we provide customisations to our presses, along with custom tooling, to meet our customer’s unique specifications.
Here is a list of some common press applications that our hydraulic presses can address.
Related: Hydraulic Punch Press Machines | A Quick Guide
COMMON PRESSING PROCESSES
Assembly
Forming
Punching
Compaction
Trimming
Deep Drawing
Coining
Embossing
Piercing
Stamping
Press Fitting
Crimping
Staking
PRESSING PROCESS EXPLANATIONS
ASSEMBLY
This is the process of using a press to fasten two or more components together. For example: Bearings, shafts, switches, pumps, rear axle assembly, hinges, gearboxes, and medical instrument assembly.
FORMING
This is when forces are exerted by the press onto a piece of metal. This causes the piece of metal to be transformed into a useful object. For example: Electrical housings, cases, brackets, panels, hinges.
PUNCHING
Punching can be carried out on a wide variety of press types. It is a common metal fabricating process that creates holes in metal sheets by using s a punch, and then a punching die. The shapes of the punch and dies can be almost any shape. Every time the punch passes through the punch die, a slug is removed from the sheet metal and passes through the die. The punching process is a very economical way of creating holes and can be incorporated with our pressing operations. For example: Vent holes, ventilation ribbing, screw holes, alignment holes, and bolt holes.
COMPACTION
Powered material is put under extreme stress by the hydraulic press forming an object. For example: Teflon powder for seals, battery compaction, munition fuse assembly, fuel cell compaction, battery compaction, clutch friction material bonding and powder make-up compacts.
TRIMMING
Cutting sheet material to size is typically done in a sheet metal guillotine. However, when there is a large quantity of blanks to cut a press with, installed cutting die may be used. Trimming is primarily done in hydraulic presses on components that were previously formed, drawn, or forged in a preliminary pressing process. The trimming process “trims” surplus and expanded material in order to achieve the desired component. For example: baskets, die-cast trimming, panels and plastic injected parts.
DEEP DRAW
This is a forming process which implements a combination of tensile and compressive conditions to form a pressed component. Deep draw differentiates from forming when the height of the component’s case is 2 times the height of the component’s diameter. Aluminium and stainless steel are two common materials used in this process. For example: Beverage cans, vessels such fire extinguishers, oil cans, aerosol cans, ducting, rifle shell casings, ferrules.
COINING
This is a cold process performed in typically a 2 piece closed die. In the pieces of the die set there are opposing forms, which have shapes and geometries machined into them. A black piece of metal is placed between the 2 die set components and extreme pressure is applied to the die set causing metal to flow into the areas of the machined geometries. Coining processes are typically carried out on hydraulic presses. For example: Coins, badges, resizing of powdered metal parts, high voltage power lugs.
EMBOSSING
The creation of imprinted designs on the surface, of a sheet metal object, without affecting the thickness of the material. This process can be integrated into other pressing processes for component serialisation purposes. For example: Lettering, logos, designs, serial numbers into surfaces of sheet metal components.
PIERCING
Piercing is similar to punching but a slug is not removed during the piercing process. For example: vents, louvers, dimpled holes in tubes, slots for connecting components.
STAMPING
This process takes a flat piece of material and using a die set and a hydraulic floor press, transforms the metal into a desired shape. For example: brackets, washers, rings, fittings, connectors, automobile door super-structures.
PRESS FITTING
This in when one component is pushed into another, by using the force of a hydraulic press creating an interference fit.
CRIMPING
An assembly technique that uses a custom assembly press and appropriate tool to fold and flatten material. Consequently, two pieces are securely fastened together by a pinching action. This technique is commonly used to join sheet metal parts.
STAKING
Is a process that permanently fastens two pieces or parts together by causing plastic deformation of the metal components in order to create a joint. For example: Rivets, Fasteners.
HYDRAULIC PRESS FOR EVERY APPLICATION | CALL US TODAY
We have a great range of high-quality hydraulic presses for sale. So whether it’s a 30-ton press you desire or a 200-ton press, Workshop Press UK can help.
If you have any questions about purchasing a Workshop press from us, we’d love to hear from you. Call us on +44 (0)1785 593 088 or get more information on our 30-ton hydraulic press by visiting our website today. Enjoyed this blog? Checkout our previous blog on Hydraulic Punch Press Machines | A Quick Guide.
For more information on HYDRAULIC PRESS APPLICATIONS talk to WorkshopPress.co.uk
Enquire Now
List your company on FindTheNeedle.