
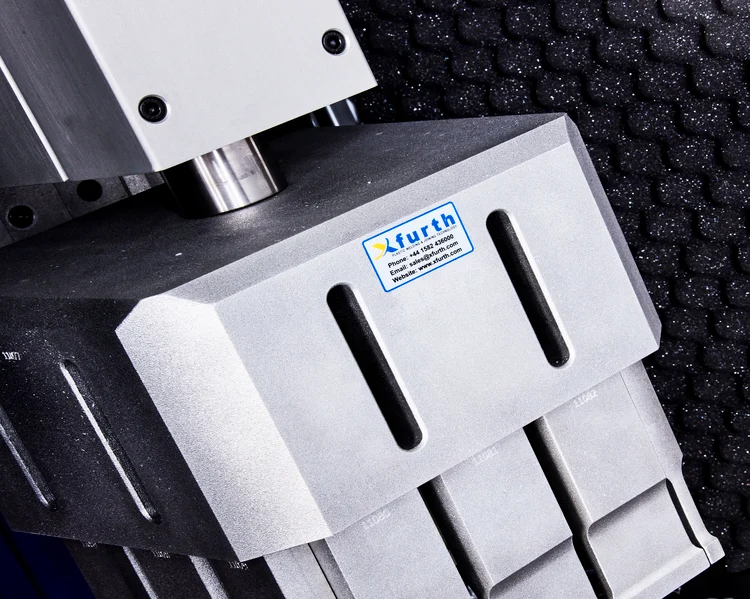
When it comes to plastic welding, selecting the appropriate welding method is crucial to ensure optimal joint strength and integrity. Two commonly used techniques are vibration welding and ultrasonic welding.
This article aims to compare and contrast these methods, providing design engineers with insights to make informed decisions about which method suits their specific application requirements.
By understanding the key differences and advantages of vibration welding and ultrasonic welding, you can choose the right welding method for your plastic welding needs.
Vibration Welding: The Basics
Vibration welding involves the frictional heating and melting of thermoplastic components through mechanical vibrations. This process generates heat at the interface, resulting in fusion and the creation of a strong joint. Key points about vibration welding include:
- Vibration welding is suitable for large, complex parts or parts with irregular shapes.
- It offers excellent bond strength, structural integrity, and resistance to environmental factors.
- Vibration welding is often used in industries such as automotive, appliance manufacturing, and packaging.
Ultrasonic Welding: Exploring the Advantages
Ultrasonic welding utilises high-frequency ultrasonic vibrations to create frictional heat, causing the plastic components to melt and form a weld. Consider the following advantages of ultrasonic welding:
- Ultrasonic welding provides precise control over weld parameters, making it ideal for delicate or small parts.
- It offers rapid cycle times, high productivity, and consistent weld quality.
Ultrasonic welding is commonly used in industries such as electronics, medical devices, and consumer goods.
Factors to Consider When Choosing the Right Method
When deciding between vibration welding and ultrasonic welding, several factors should be considered:
- Component Size and Complexity: Vibration welding is suitable for larger and more complex parts, while ultrasonic welding excels with smaller and more delicate components.
- Material Compatibility: Both methods are compatible with a wide range of thermoplastics, but certain materials may be better suited for one method over the other.
- Production Volume and Speed: Ultrasonic welding offers faster cycle times, making it ideal for high-volume production, while vibration welding may be more appropriate for lower-volume applications.
- Joint Strength and Aesthetics: Evaluate the required joint strength and desired appearance of the weld to determine which method can deliver the desired results
Choosing the right welding method, whether vibration welding or ultrasonic welding, is crucial for successful plastic welding applications.
By considering factors such as component size, material compatibility, production volume, and joint requirements, you can make an informed decision. Both vibration welding and ultrasonic welding have their advantages and are widely used in various industries.
To further enhance your knowledge and gain practical insights into vibration welding, we invite you to download our free guide, "The Vibration Welding Guide." This comprehensive guide provides valuable information on how to choose the right vibration welding machine and optimise your vibration welding processes. Download your free guide from today.
For more information on Choosing the Right Welding Method: Vibration Welding vs. Ultrasonic Welding talk to Xfurth Ltd