
Sign In
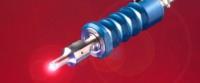
Ultrasonic welding is a relatively new bonding technique that is evolving all the time. Originally discovered in the 1940's, ultrasonic welding uses ultra-high frequency sound waves to bond materials. The fundamental principle is extremely simple; when an ultra-fast frequency soundwave is introduced to some materials, they melt.
This form of bonding technology is unique because of the control that it offers, and its ability to join dissimilar materials. It is used extensively in the aerospace, automotive, medical and plastic manufacturing industries, but in recent years ultrasonic welding has also been utilised in the manufacture of electronics as well. Because all of the heat is localised in the weld area, this method can be used to bond very fragile materials together.
When ultrasonic welding is employed, the throughput times are very short and it lends itself to automated processes. Almost every part of the bonding process is controllable to a level that sometimes isn't possible in other forms of welding. Many industries are looking into ways to take advantage of ultrasonic welding, especially with the rise of nearly fully automated production facilities.
The Ultrasonic Welding Process
At its most basic level, ultrasonic welding is very simple:
Two materials are held together with mechanical force in an ultrasonic press.
On contact a metal tool called a sonotrode (specifically designed for the application) introduces ultra-high frequency sound waves into the materials.
The press is made to direct that energy into the materials at a predetermined weld point.
The materials melt when the high frequency sound is applied, usually in a fraction of a second.
Once bonded, the materials are left to rest under the pressure, and the bond hardens.
For more information on Understanding The Ultrasonic Welding Basics - Where To Begin talk to Xfurth Ltd
Enquire Now
More News
List your company on FindTheNeedle.