
Sign In
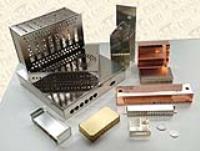
Compliance with the European EMC Directive is mandatory and that means keeping in and/or keeping out electronics assemblies radio and electro magnetic frequency interference. What are the options and where do you start? Peter Hendrick, Perancea’s MD, takes a grass roots look at just what is available and what can be achieved from a viable customised standard perspective.
Most specifiers are now aware of the standard types of board level screening that are available through stockists and distributors but how many know what alternative options are available to them. More importantly, are they aware of the true cost implications?
Attacking the problem of screening head on, what materials and finishes are available is the best starting point. Laying down ground rules, for mechanical and cosmetic/aesthetic reasons, rust and oxidation prevention is a must. RoHS compliance is a must too and obviously, available material processing needs careful consideration.
Mild steel, with its excellent screening properties below 100MHz, is available as thin as 0.20mm. It is also relatively low in cost, easily worked and it will accept most finishes thus easily solving the rust and RoHS problems. Nickel sheet, an alternative to mild steel is also excellent for screening. It requires no additional finishing but carries a comparatively high cost premium. However it does mark when spot welded.
For applications requiring better than 100MHz EMC screening, materials such as copper should be a consideration but again cost may be prohibitive as not only is the copper expensive, it must be more expensively brazed or soldered instead of welding. However, if humidity and/or temperature variations are not a consideration, electrolytic tinplate provides an inexpensive solution requiring no further finishing and thus saving costs. Electrolytic tinplate is ideal for prototyping applications. However, as the material is tinned prior to fabrication, bare steel edges are created in production and although these may be normally stable in good conditions, they are obviously liable to oxidation in adverse operating conditions or during ultrasonic cleaning.
After exhaustive evaluation, Perancea has found bright acid tin plating to be the best RoHS compliant alternative finish to tin/lead. It is available in commercial grades with nominally 10 microns thickness, 10 microns minimum thickness to BS1872 and for harsh environments, DEF 03-8 at 25 microns thickness. The material is easily soldered given that appropriate solders and fluxes are used.
It has been reported that some problems have been encountered when tin/lead solder has been used. Perancea has looked into the problem and found Cookson Electronics, www.alphametals.com, to be particularly helpful. Given the right materials, excellent results can be achieved: further advice should be sought from solder manufacturers, particularly for reflow soldering applications.
Paint and epoxy powder coatings, although outwardly solving oxidation and aesthetics problems, can act as an insulator. Masking selective areas can provide good electrical connection.
When it comes to screening, only final product testing provides a true evaluation. However, a starting point is essential and Perancea’s comparison of materials for screening applications may help, comparing material attenuation performance with cost ratios.
Choice of material should also be made in conjunction with its availability in thinner gauges and its plating options.
The first choice for outwardly cost-effective enclosures more than likely is for standard product but if a suitable size, shape or screening properties cannot be found, Perancea is expert at producing from 5mm high to very large enclosures using standard tooling and thus minimising costs and providing a viable solution.
With the continual march for ever smaller miniaturisation, so the need for screening has become more and more important, especially to avoid cross coupling in multi frequency circuits. The need to segregate circuit sectors from one another is easily resolved using separate enclosures around each sector. With this in mind, it is often significantly more effective in terms of space and cost to use internal dividers or labyrinths within the overall enclosure or housing. Dividers can also be fitted with PCB mounting pins that, like those on the wall of an enclosure, can be soldered in position for maximum shielding.
As part of its continuing commitment to providing economic and viable solutions for customers, Perancea standard options for enclosure features involve no additional tooling costs. Often standard enclosure location pin position and sizing do not fit the design constraints bill but, without affecting the cost of an enclosure, adding, removing and/or repositioning pins is an easy operation. This fact provides the opportunity to consider alternative circuit board location pin features including locking pins that hold an enclosure in place prior to soldering, often a pre-requisite for reflow soldering. Perancea developed its locking pin feature as a standard option in conjunction with Motorola to obviate the problems of even the slightest board curvature causing problems on the production line.
Alternative tapered pin options make enclosure assembly on a PCB quick and easy, and shouldered or solder relief pins prevent solder wicking. A further way to prevent unwanted solder wicking, developed by Perancea in conjunction with Siemens, is by scoring an anti-solder migration barrier into the sides of an enclosure, thus providing a physical barrier against solder creepage.
Additional earthing connections on a frame or shielding can often be required by designers. With Perancea’s capability, adding a 0.25in fast-on tab, welded to the enclosure or, alternatively, fitting a threaded stud or bush easily achieves the requirement. And, if required, an earthing symbol is easily stamped alongside the connection. Stamping, screen printing, indelibly marking and labelling are all easily and viably catered for, effective means of achieving other component marking, for component identification or aesthetics.
Holes, cut outs and apertures can all be provided in standard enclosures at minimal cost, usually without tooling costs as Perancea, for example, has an extensive tooling library that includes most common D connectors and holes with anti-rotational flats or pips. Where circuit board tracking needs to pass under the wall of an enclosure, small cut outs or mouse holes can readily be produced. Even ventilation features can be an option without affecting screening properties. Perancea, in conjunction with leading RFI/EMI consultancy Cherry Clough Consultants, has produced an advisory leaflet on shielding at board level and providing a formula for calculating permissible hole sizes.
Where lidded cans provide a good solution to board level screening, additional lid retention can easily be added for extra security or anti-vibration features. The simplest and most cost-effective way to achieve this is by incorporating pins or tabs on the edge of an enclosure. These then mate with respective holes or slots in the enclosure lid and once product assembly and testing is complete, these can be folded over to lock the lid in place. For additional retention whilst maintaining easy access inside the enclosure after manufacturing, dimples in the frame or on the side of the can align and mate with holes provided on the fingers of can lids which remain removable without difficulty.
For ultimate security and accessibility on can solutions, a range of options for screw retention is available including Perancea’s unique method of lancing enclosure corners. Lancings or indentations in the wall of an enclosure provide an excellent, low cost means of locating PCBs horizontally or vertically. Retention of the board is then completed by soldering the earth track to the side of the enclosure. Alternatively, small brackets with threaded bushes or studs can be spot welded internally to provide support. Similarly brackets, threaded studs and bushes provide even more ways of mounting a complete enclosure.
In essence, standard solutions need not be a constraint to an ideal screening solution. The options that can be easily and cost-effectively accommodated on standard enclosures are virtually endless. At Perancea, many so called special features are already covered by standard tooling, even for low volume production where a modest additional cost of having exactly what a design calls for. The cost of modifying a standard and incorporating required features can be recovered many times over through product manufacturing and assembly savings.
As was expressed by Bernard Hancock, Chief Electronics Technician at the University of York on delivery of a customised standard instrument casing, “The revised casing designed by Perancea, not only has marked repeatable fabrication performance but manufacturing costs have dramatically reduced. The improved appearance is producing a very popular response from our customers”. That means job done, cost-effectively!
For more information on Perancea: Making Electronics Enclosure Screening Make Sense talk to Perancea Ltd
Enquire Now
List your company on FindTheNeedle.