
Sign In
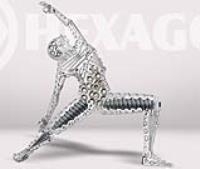
HEXAGON Orthopedics is a medical device manufacturing company in Itapira, São Paulo, Brazil. Founded in 1988 by three enterprising brothers, the company designs, manufactures, and sells orthopedic implant devices and related surgical tools. HEXAGON has an extensive catalog of available products such as screws, plates and nails for fracture repair, components for prosthetic hips, and the surgical instruments used to implant these devices. The wide range of products means HEXAGON works with an increasingly large number of different part geometries. These high-tech medical products are made from sophisticated, often difficult to machine materials. Many of the parts cut at HEXAGON end up in a person’s body and require a high degree of precision and surface finish quality.
In 2012, it became apparent to HEXAGON that they needed a faster, more accurate way to cut titanium, aluminum and stainless steel. Impressed with the precision and versatility that waterjet technology offered, the company decided to purchase an abrasive waterjet. After finalizing the purchase, HEXAGON had to wait a full six months for the new waterjet to be delivered and installed. In 2013, the waterjet was finally operational, but fell short of HEXAGON’s expectations. The waterjet was not accurate enough to meet HEXAGON’s high-precision cutting needs. It also cut too slowly and left a poor edge quality. All the parts cut with the waterjet needed to go through secondary finishing operations, which greatly slowed production time. Adding to the disappointment was the fact that the waterjet was constantly breaking down and demanded frequent maintenance.
Even through the frustration of this initial experience with the technology, HEXAGON saw value in waterjet cutting because of its amazing ability to cut practically any material and with no heat-affected zone. The company sought ways to reduce the waterjet’s downtime, including the purchase of an automatic Solids Removal System (SRS) so they wouldn’t have to take the waterjet offline to clean out the tank. The SRS was supplied and installed by Weld Vision. HEXAGON was impressed with the prompt and professional service provided by Weld Vision and a partnership of trust was formed between the two companies.
Weld Vision noticed the high demand for waterjet-cut parts the orthopedics manufacturer was experiencing and knew HEXAGON’s current waterjet wasn’t up to the job. Weld Vision also knew an OMAX 5555 abrasive waterjet with a Tilt-A-Jet cutting head could handle the demand and offered that exact solution. HEXAGON purchased the OMAX 5555 with the idea that it could handle the waterjet cutting jobs during the times the other waterjet was down. The OMAX waterjet met and exceeded that expectation.
This time, the new waterjet was delivered and installed within 30 days of finalizing the purchase and HEXAGON was delighted with the service provided by Weld Vision. The customer satisfaction didn’t stop there. HEXAGON found the OMAX Intelli-MAX software easy to use and started to cut production parts with the OMAX waterjet within a few days after installation. When they did, they experienced a dramatic increase in accuracy and edge quality in their waterjet work compared to the work done on the other machine. With the OMAX 5555, HEXAGON found they could cut 15-20mm thick stainless steel and maintain a precision of 0.020mm, with no need for secondary finishing. Not only was the OMAX more accurate, it was also faster. So much faster, in fact, that HEXAGON was able to significantly reduce production time and labor costs. The OMAX could complete in one shift all the waterjet work that required two shifts with the first waterjet. What’s more, the OMAX required far less maintenance than the other machine.
With OMAX waterjet technology, HEXAGON has been able to reduce its costs per part, helping the business thrive in the competitive medical device manufacturing market.
For more information on Orthopedic Device Manufacturer Upgrades to OMAX Abrasive Waterjet talk to Aquajet Machining Systems Ltd
Enquire Now
List your company on FindTheNeedle.