
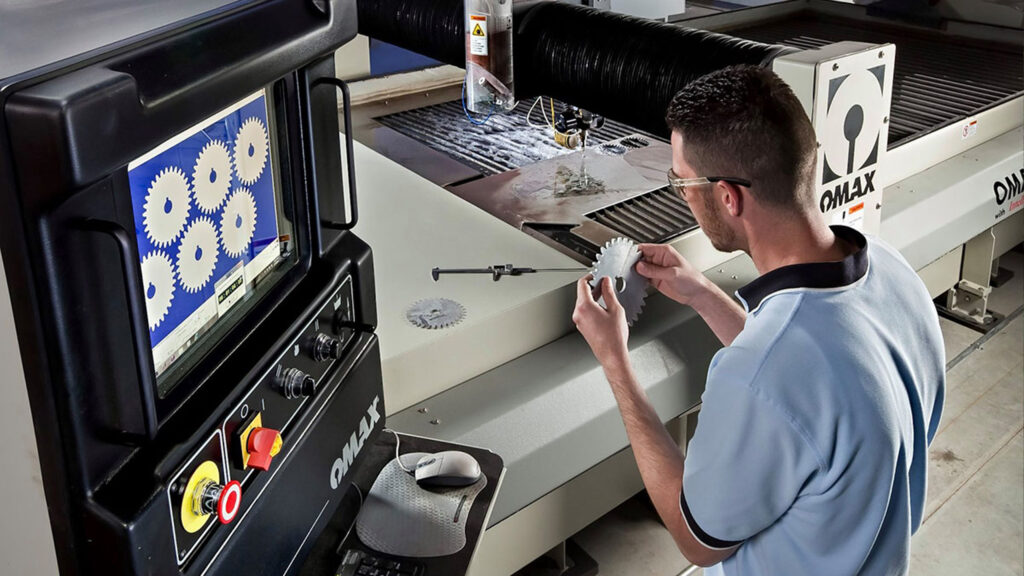
In the realm of aerospace engineering, where precision is paramount, titanium reigns supreme. From nose-to-tail aircraft components to spacecraft and defence systems, titanium’s exceptional strength-to-weight ratio, corrosion resistance, and ability to withstand extreme conditions make it the metal of choice. Yet, the very properties that make titanium indispensable in flight also pose challenges in fabrication.
The perfect complement to titanium’s demands, abrasive waterjet cutting.
Maintain Cool Composure
Unlike conventional methods, abrasive waterjet cutting operates without generating excessive heat. This is crucial for titanium, which exhibits low thermal conductivity. Heat can warp the material, compromise its structural integrity, and diminish its corrosion resistance. By employing a cold-cutting approach, abrasive waterjet preserves titanium’s properties intact.
Embrace Versatility and Simplicity
Free from the constraints of heat, abrasive waterjet cutting offers unparalleled flexibility with titanium. It effortlessly handles a spectrum of thicknesses, from thin sheets to dense blocks, making it ideal for both intricate components and near-net parts. Brands like OMAX’s OptiMAX elevate this flexibility, enabling the creation of complex, tight-tolerance parts with minimal reliance on highly skilled operators.
Furthermore, abrasive waterjet cutting’s compatibility extends beyond titanium, opening avenues for diversification in product offerings. Whether it’s aluminium, nickel alloys, composites, laminates, or plastics, this technology seamlessly transitions between materials, catering to various industry segments.
Bid Farewell to Tooling Woes
The bridge of abrasive waterjet and titanium eliminates the headaches associated with conventional cutting methods. Titanium’s hardness can swiftly wear down traditional tools, but with waterjet, the abrasive does the heavy lifting without direct contact, rendering tool wear a non-issue. Complex setups and frequent tool changes become relics of the past, streamlining operations and reducing downtime. Moreover, abrasive waterjet’s minimal dust and debris output ensure a cleaner working environment.
In essence, the symbiotic relationship between abrasive waterjet cutting and titanium not only preserves the intrinsic qualities of this metal but also unlocks new possibilities across industries. From aerospace applications to broader manufacturing realms, this combination proves itself as the epitome of efficiency and innovation.
For more information on Titanium and Abrasive Waterjet: The Perfect Match talk to Aquajet Machining Systems Ltd