
Sign In
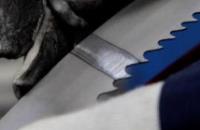
Dynashape – the UK’s most experienced saw blade servicing and remanufacturing specialist – has been awarded a service contract for the maintenance of the bandsaws used in Jaguar Land Rover’s Lode Lane teardown cells.
The contract follows Dynashape’s recent supply of a new high-speed bandsaw for use in the teardown area, and the assistance it has given to Jaguar Land Rover in the development of its teardown cutting technologies.
Up to 4,000 joints per inspection
While vehicle teardown is a far from new concept in quality control, the shift towards lightweight aluminium body components has brought a significant change in the way the teardown process is completed. Whereas spot-welded steel joints would previously have been cut for examination, today’s use of rivets demands that each riveted joint is examined individually for integrity. For a typical vehicle randomly selected for teardown at the Lode Lane facility, this could mean that as many as 4,000 joints have to be prepared for inspection.
World-leader in aluminium body structures
As a result of Jaguar Land Rover’s increasing use of aluminium body structures – the manufacturer is a world-leader in the area of aluminium body construction – the teardown facility at Lode Lane has benefited from considerable investment as manufacturing has switched to aluminium, and has doubled in capability over the last few years.
“Including the DoAll Zephyr high-speed vertical bandsaw supplied by Dynashape, we have a total of four bandsaws in the teardown area,” comments Jaguar Land Rover Group Leader, John Mackenzie. “Token-size jointed pieces of typically 2cm square are cut using bandsaws, after which each rivet is cut down the centre using a diamond cutting disc machine, ready for microscopic analysis.”
Most suitable blade technology
With vehicle construction almost totally switching to aluminium, Jaguar Land Rover’s challenge was to find the most appropriate blade technology that would be suitable for use with today’s lightweight aluminium vehicle bodies, but could also be used for cutting steel when the requirement arose. 90% of material cut is aluminium; the remainder is steel.
Extensive cutting trials
“Dynashape has been incredibly helpful and supportive as our teardown capability has expanded and made the transition to cutting aluminium,” continued John MacKenzie. “Committed to helping us find the best bandsaw blade types for our machines, the Dynashape team carried out extensive cutting trials and provided us with a range of different blade types to try. This enabled us to identify the specific tooth configurations that best suited our cutting requirements, including occasional work with steel. I am delighted that following all their hard work in meeting our saw blade requirements, Dynashape will also maintain our bandsaws.”
Improved cut quality and blade life
“We were delighted to be invited to bring our cutting expertise to Jaguar Land Rover’s teardown cells,” adds Dynashape’s Managing Director, Chris Parkes. “Not only have we improved cut quality and blade life, but also, through carefully structured training sessions, we have given the teardown cell operators a much greater understanding of – and confidence in – the capabilities of the blade types they are now using.
“Although the new DoAll bandsaw machine we supplied to Jaguar Land Rover is equipped to provide high-speed friction sawing if required,” says Chris Parkes, “our approach was to identify bandsaw blades that would run at the conventional speeds the teardown team is used to cutting at, all while providing the best results.”
Dynashape is an approved supplier to Jaguar Land Rover. The blades supplied include Dynashape’s ‘Silencer’ product (1” x 6/10 TPI) and ‘Intenss Pro’ product (1/2” x 8/12 TPI). Both products provide smoother cutting action on aluminium as well as on occasional steel test pieces.
For more information on DYNASHAPE WINS JAGUAR LAND ROVER SERVICE CONTRACT talk to Addison Saws Ltd
Enquire Now
List your company on FindTheNeedle.