
Safety Measures for Warehouse Environments
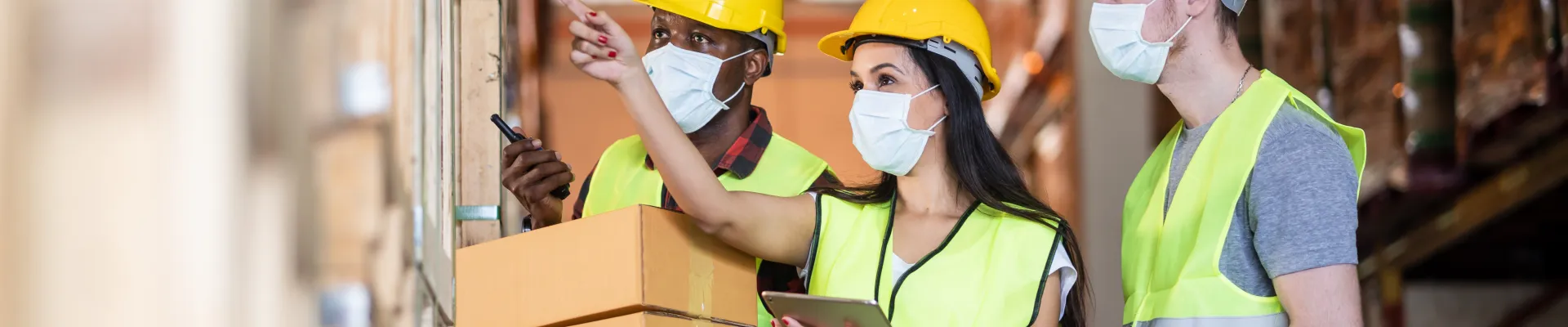
Workplace safety should be top of the list of priorities for every employer. The welfare of staff and visitors should be paramount and performing regular risk assessments is an invaluable way of understanding what potential hazards may be prominent in your work environment. We have highlighted some common accidents that occur, due to not having the correct safety measures in place, and how you can prevent them.
Manual Handling Injuries
Manual handling injuries are one of the most common complaints due to various factors but often, simple complacency. The nature of warehouse work is generally the storage and logistics of products and materials meaning warehouse workers spend a great deal of time moving stock from A to B. The task of lifting, carrying or even positioning heavy objects can cause great strain on the musculoskeletal system and even more so if not performed correctly. Repetitive actions and improper techniques can cause sprains and long-term injuries. Comprehensive training clarifying the importance of correct techniques and following procedures is vital. Mechanical assistance is also a huge safety measure for warehouse environments. A forklift, stacker or trolley, combined with a solid racking system, will aid staff in completing their work without having to put their body under unnecessary duress.
Falls
Falls are a natural occurrence but the preventable reasons why they occur or safety measures in place to reduce the impact in the workplace are key considerations. Many slips and trips that result in lawsuits come from a simple spillage or out of place obstacle. Risks that are easily removed by health and safety training should be undertaken by all staff. Immediate cleaning of spills, appropriate signage and storing objects in their correct place. It seems so simple, doesn’t it? Other causes of falls may be improper clothing or footwear, inadequate lighting or rushed actions, all avoidable through proper training and upkeep. The greater danger of a fall in a warehouse environment is from a height. This could turn an accident into a tragedy. If stock is stored on a mezzanine there must be handrails or barriers, and pallet gates in place to prevent any possibility of falling from an exposed edge or manual handling injuries. When handling larger or heavier products and materials on pallet racking systems, teams should use a forklift truck or other appropriate handling equipment to protect themselves from falling objects but to also safely manoeuvre items as and when required. When working at height for installations or maintenance and where there are exposed edges, fall protection such as harnesses is essential and potentially lifesaving.
Click to see our range of safety barriers. These are specifically designed to ensure protection from load falling and prevent any exposure to edges.
Fire Hazards
Warehouses are a place for storing vast quantities of stock. Some of which may be combustible or flammable. All COSHH information needs to be available for all items so all staff can be clear on how to handle them safely. Any flammable items must be stored safely in clearly marked safety cabinets and the appropriate conditions. Fire can spread rapidly in a warehouse environment leaving stock destroyed, repair costs devastating and worst of all putting human life at risk. Regularly testing all electrical infrastructure and fire equipment is a legal requirement and maintaining health and safety training with all staff will keep the risk to a minimum. Regular fire risk assessments are also a legal requirement and these can be easily arranged with independent registered companies.
Chemical Exposure
Along with potentially flammable products, many warehouses may also store hazardous substances that need to be handled carefully – such as pesticides, solvents, paints or cleaning chemicals. Exposure to these substances can occur through inhalation, ingestion or direct contact with the skin. The results of such contact can result in burns, scars or permanent health problems and, without the correct immediate aftercare, the risks greatly heighten. Appropriate safety measures for warehouse environments should include proper handling training for all staff tasked with any movement of hazardous substances and the supply of full personal protection equipment (PPE).
Machinery and Equipment Malfunctions
Various machinery and equipment may be used daily in a warehouse environment which brings with it more potential for accidents. With heavy machinery comes power and this power, if not handled appropriately can result in dangerous situations and even life-threatening injuries. However, with regular maintenance and inspections, this need not be a concern. As with all health and safety, comprehensive training for all operating personnel is the key to preventing accidents and minimising risks.
Protect your people
Regular, thorough training and risk assessments are the key safety measures for warehouse environments to protect their staff and prevent accidents. Though accidents will occur it is essential to minimise risk wherever possible and suitable storage and safety precautions are certainly a step in the right direction. Understanding the value of safe operation and the following of protocol is something we at Advantage value highly. With years of experience in supplying the right storage solutions for the needs of the customer and creating safety barriers that fit your work environment, we are the experts in keeping your staff safe.
Get in touch and let us help you keep your biggest assets safe.
For more information on Safety Measures for Warehouse Environments talk to Advantage Storage and Handling Ltd