
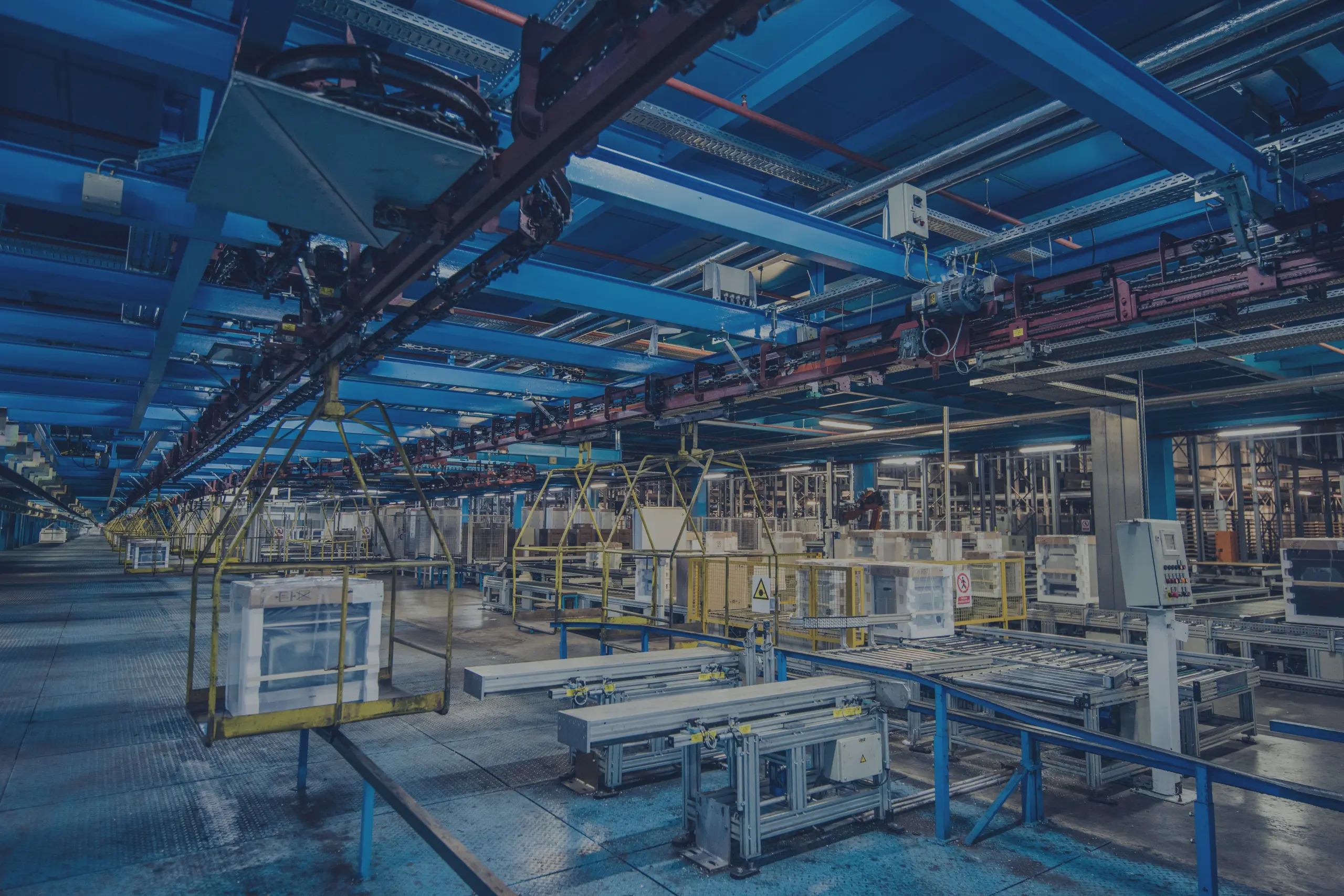
In manufacturing environments, dust control is a critical aspect of maintaining workplace safety,
ensuring product quality, and complying with environmental regulations.
The HSE emphasises a hierarchy of control measures in dust control, prioritising elimination and engineering controls over-reliance on PPE. Employers have a legal obligation to protect workers from dust-related health risks through effective risk assessments, control measures, and ongoing monitoring.
The presence of dust in manufacturing facilities poses serious risks, including health hazards to employees, fire and explosion hazards, and contamination of products.
Effective dust control strategies encompass a variety of measures, with dust monitoring playing a pivotal role in the detection and management of airborne particulate matter. This article delves into the importance of dust control in manufacturing, with a
focus on the role of dust monitoring.
The importance of
dust control
Dust in manufacturing settings can originate from various sources, depending on the industry. Common sources include cutting, grinding, and sanding materials like wood, metal, or concrete, as well as chemical processes that release fine particulates into the air. The dangers associated with dust are numerous and include:
- Health hazards: Inhalation of dust, particularly fine or respirable particles, can lead to respiratory issues, such as asthma, chronic obstructive pulmonary disease (COPD), and even lung cancer. Silica dust and asbestos are well-known for their long-term health risks.
- Combustion risks: Some types of dust, such as wood, sugar, or metal dust, are highly combustible. In certain conditions, airborne dust can lead to explosions, with devastating consequences. Industries such as food processing, pharmaceuticals, and metalworking are particularly at risk.
- Product contamination: In industries like pharmaceuticals, electronics, and food manufacturing, dust contamination can compromise product quality, leading to recalls, production downtime, and financial losses.
- Environmental impact: Dust emissions can affect the surrounding environment, leading to air pollution and potential harm to nearby communities. Regulatory bodies, such as the Environmental Protection Agency (EPA), have stringent guidelines on allowable dust emissions to protect public health and the environment.
Given these risks, controlling dust is not only a regulatory necessity but also a vital part of maintaining operational efficiency and ensuring worker safety.
The role of dust monitoring for dust control in manufacturing
Dust monitoring is a fundamental aspect of dust control, allowing manufacturers to detect, measure, and manage airborne particulate matter in real time. This proactive approach is essential for maintaining safe working conditions and ensuring compliance with regulatory standards. Dust monitoring can be implemented using a variety of technologies, depending on the specific needs of the facility and the type of dust present.
Key benefits of dust monitoring
- Real-time detection: Dust monitoring systems provide real-time dust levels, enabling immediate action if levels exceed safe thresholds. This can prevent dangerous accumulations of dust, reducing the risk of explosions or health issues.
- Regulatory compliance: Many industries are subject to strict regulations regarding permissible dust levels. Continuous dust monitoring ensures that a facility remains compliant with occupational safety and environmental standards, helping avoid costly fines and shutdowns.
- Worker safety: By continuously monitoring airborne dust, facilities can ensure that workers are not exposed to harmful concentrations of particulates. This contributes to a healthier work environment, reducing the risk of occupational illnesses and improving overall productivity.
- Process optimisation: Dust monitoring data can be used to optimise manufacturing processes. For example, if certain operations generate excessive dust, adjustments can be made to equipment or procedures to reduce dust production. This can lead to cost savings and improved efficiency.
Implementing a dust monitoring program
To effectively manage dust in a manufacturing environment, it is essential to implement a comprehensive dust monitoring program. The following steps outline the key components of such a program:
- Identify dust sources: Conduct a thorough assessment of the facility to identify all potential sources of dust. This includes not only the obvious areas, such as cutting or grinding stations, but also less apparent sources like material handling and ventilation systems.
- Determine dust levels: Establish baseline dust levels for different areas of the facility by conducting initial measurements. This will help in setting thresholds for acceptable dust levels and identifying areas that require more intensive dust control measures. See the below table for a comparison of the parameters that dust monitors measure.
- Select appropriate monitoring technology: Based on the type of dust and the specific requirements of the facility, choose the most suitable dust monitoring technology. Consider factors such as particle size, concentration, and the need for real-time data.
- Install and calibrate monitors: Install dust monitors in strategic locations throughout the facility, focusing on high-risk areas where dust levels are likely to be highest. Ensure that the monitors are properly calibrated and maintained to provide accurate data. By renting dust monitors, you can be assured that they have been recently calibrated and maintained.
- Set thresholds and alerts: Establish thresholds for dust levels based on regulatory requirements and industry standards. Configure the monitoring system to trigger alerts when dust levels approach or exceed these thresholds, allowing for immediate corrective action.
- Continuous monitoring and data analysis: Implement continuous dust monitoring to track dust levels over time. Regularly analyse the data to identify trends, optimise processes, and adjust dust control measures as needed.
- Training and safety procedures: Ensure that all employees are trained in dust control procedures and understand the importance of monitoring systems. Establish protocols for responding to high dust levels, including shutdown procedures, maintenance checks, and emergency actions.
Dust monitor comparison for dust control
TSI BlueSky 8143 | TSI BlueSky 8145 |
DustTrak 8533 |
|
Particulate size fractions | PM1, PM2.5, PM4 & PM10 | PM1, PM2.5, PM4 & PM10 , O3, CO, CO₂, NO2 and SO2 | PM – PM10 |
Also measures | Temperature and humidity | Temperature, humidity and barometric pressure |
Smoke, fumes and mists |
Indoor or outdoor monitoring | Indoors and outdoors | Indoors and outdoors | Indoors and outdoors |
It is important to note that dust pollution may be intermittent depending on activity on manufacturing sites, so continuous monitors can identify peaks and thereby assist in the attribution of sources.
Dust control in manufacturing summarised
Dust control is a vital component of maintaining a safe and efficient manufacturing environment. By integrating dust monitoring systems into their operations, manufacturers can proactively manage dust levels, protect their workers, ensure product quality, and remain compliant with regulatory standards.
Investing in advanced dust monitoring technologies not only enhances safety but also contributes to the overall sustainability and success of manufacturing operations.
With a variety of applications for dust monitoring, appropriate technology must be employed, therefore the Ashtead Technology equipment fleet has been developed to meet almost every need, and technical advice is available to help consultants and site managers ensure that dust hazards and effectively managed.
For more information on Dust control in manufacturing: a focus on dust monitoring talk to Ashtead Technology Ltd