
Sign In
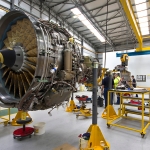
As Tooling Coordinator for Monarch Aircraft Engineering (MAEL), Barry Lee ensures that his company’s engineers are provided with the best available technologies for their aircraft test and inspection work. “We maintain a stock of the instruments that we use most frequently and this is regularly supplemented by rented equipment from Ashtead Technology during periods of high demand and when we need to evaluate a new technology,” he says.
Based at London Luton Airport, MAEL is a sister company to Monarch Airlines providing base maintenance, line maintenance, engineering and technical support, component and full material support, aircraft engine services and technical training.
MAEL’s services were recently recognised at the annual Airline Economics Aviation 100 Awards in Dublin, at which the company was named 'MRO of the Year 2013' (MRO = maintenance, repair & overhaul). The award followed an 11 month customer satisfaction survey in which MAEL achieved a rating of excellence from customers around the world.
The quality of MAEL’s services is underpinned by a highly effective test and inspection capability which utilises the latest technologies to comply with all regulatory requirements. For example: thermal cameras are employed to identify potential weaknesses, corrosion or poor electrical connections; ultrasonic instruments enable the detection of flaws or cracks that are not visible to the human eye, and borescopes enable the internal inspection of aircraft components that would otherwise be difficult or impossible to assess.
The original borescopes consisted of a rigid or flexible tube with an eyepiece at one end and an objective lens at the other. Optical fibres provided illumination for the remote object. A video borescope uses a miniature video camera at the end of the flexible tube and a display in the handle shows the camera view, and the viewing position can be changed with a joystick.
Video borescopes (also known as videoprobes or videoscopes) are now one of the most widely employed non-destructive testing (NDT) instruments. For example, borescopes can be used to inspect the inside of a reciprocating engine cylinder, by inserting the flexible probe into an open spark plug hole to detect damaged pistons, cylinder walls, or valves. Similarly, the hot section of a turbine engine can be assessed by inserting a probe through the hole of a removed igniter or via the access plugs which are designed into many engines, specifically to enable borescope inspections. However, Barry says “There are many other applications for borescopes because of their ability to provide access to parts of the aircraft that would otherwise be difficult to inspect.”
Commenting on the need to supplement MAEL’s fleet of borescopes with hired instruments, Barry says: “There are two main reasons for renting. Firstly, to increase our capability during periods of high demand; and secondly to enable us to try out new instruments or technologies, without having to commit to significant capital expense.
“We have dealt with Ashtead Technology for around ten years and it has been very useful to develop an effective working relationship – instruments can be delivered very quickly, and they are ready for immediate use, which helps ensure the speed and efficiency of our work.”
Ashtead Technology’s Jay Neermul believes that continual investment in the company’s rental fleet is a core strength of the business; “Our overall objective is to ensure that customers have access to the instruments that best meet their needs, but beyond that we are constantly investing in new technology so that our customers don’t need to.”
In common with many other technologies, the latest borescopes are smaller and easier to use than their predecessors; whilst producing better quality images and video. For example, the GE XL Go delivers sharp, clear digital images with a crystal-clear VGA LCD that gives inspectors the sharp, detailed images needed to ensure accurate inspections. Both still images and motion video can be recorded to the internal flash memory or a removable USB ThumbDrive. Unlike other video borescopes, the XL Go has no bulky base unit, no backpacks, no tethered scopes or power cords to get in the way.
One of the latest additions to Ashtead Technology’s fleet of NDT inspection instruments is the Olympus IPLEX UltraLite. Weighing just 700 grams, it incorporates a combined control and display unit that fits in the palm of one hand and frees the other hand to guide the probe insertion tube. Observed images can be stored on a memory card as high-quality JPEG images and MPEG-4 movies.
In addition to borescopes, Jay Neermul says: “A wide variety of other NDT and remote visual inspection instruments are employed within the aerospace sector. For example, high-speed cameras are used to study the action of components that move too fast for the human eye.
“In addition, portable XRF analysers are frequently employed to check the metallic components built into airframes and jet engines. Major alloy families used in aerospace applications include aluminium within the skins of aircraft, titanium and stainless steel within the frame and engine components, and nickel/cobalt high-performance alloys in jet engine components.”
Summarising, Barry Lee says: “The ability to hire instruments at very short notice is a major advantage because it reduces the capital cost that would be incurred by maintaining a tooling capability to meet maximum demand. For example, if non-routine inspections are required as a result of bird strikes or flight crew reports, the ability to rent means that our instrumentation capacity can be adjusted accordingly.”
For more information on Instrument hire boosts inspection efficiency at Monarch Aircraft Engineering talk to Ashtead Technology Ltd
Enquire Now
More News
List your company on FindTheNeedle.