
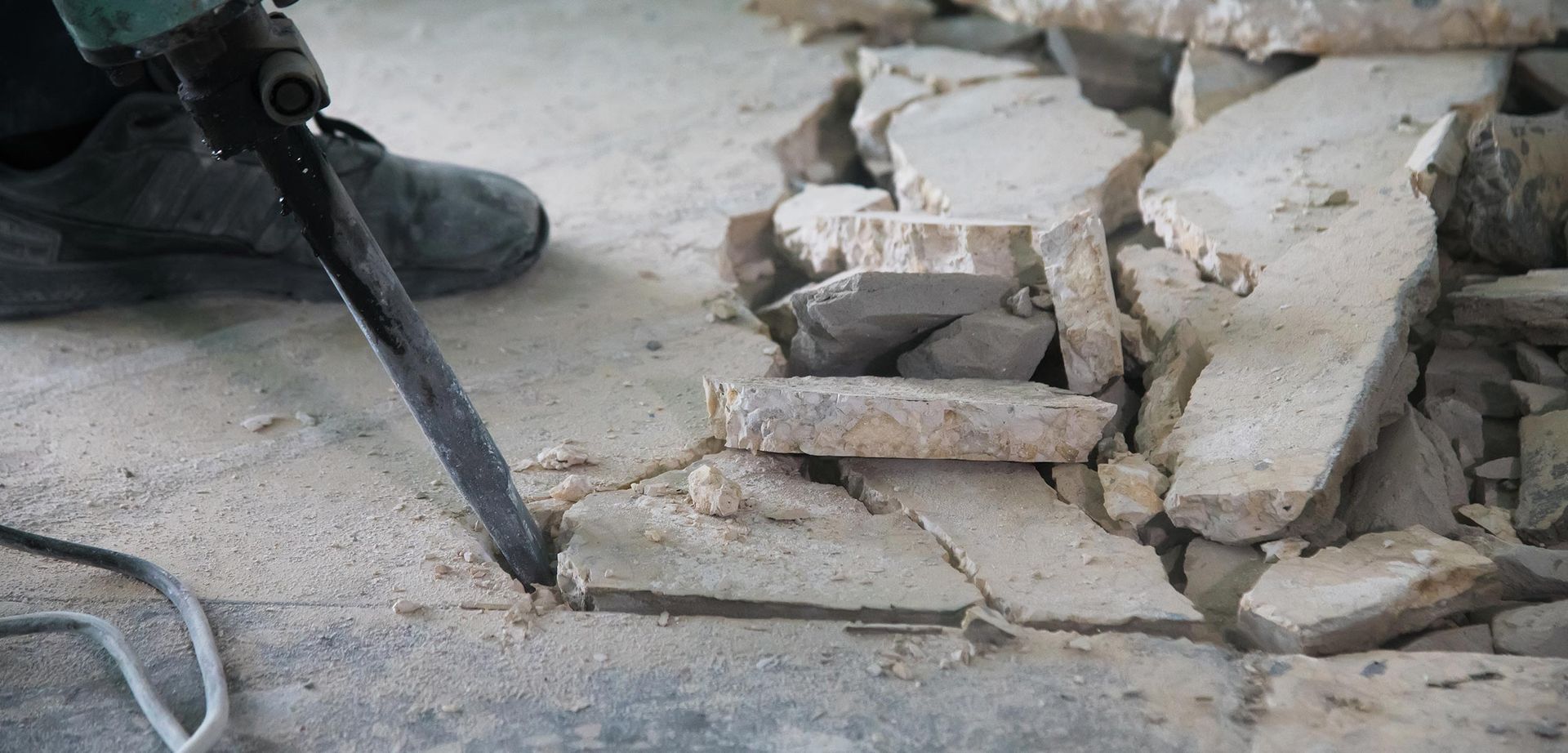
New build projects or renovations that involve the laying of new floors will usually require floor screed. A poor floor screed can cause significant problems for your build.
WHAT IS FLOOR SCREED?
Floor screed is the combination of cement, water and graded aggregates that is applied to the concrete base of a floor to create a level surface. Its purpose, as part of your build, is to provide a sturdy base onto which a final floor application such as boards, carpet, linoleum, tiles or vinyl flooring can be laid. The result should be a smooth, level floor that is stable and robust.
Clockwork Screed are experts in the supply and installation of cementitious liquid floor screeds. We supply builders, home owners and self-build contractors with our high quality liquid floor screed that can be applied to floors with or without underfloor heating.
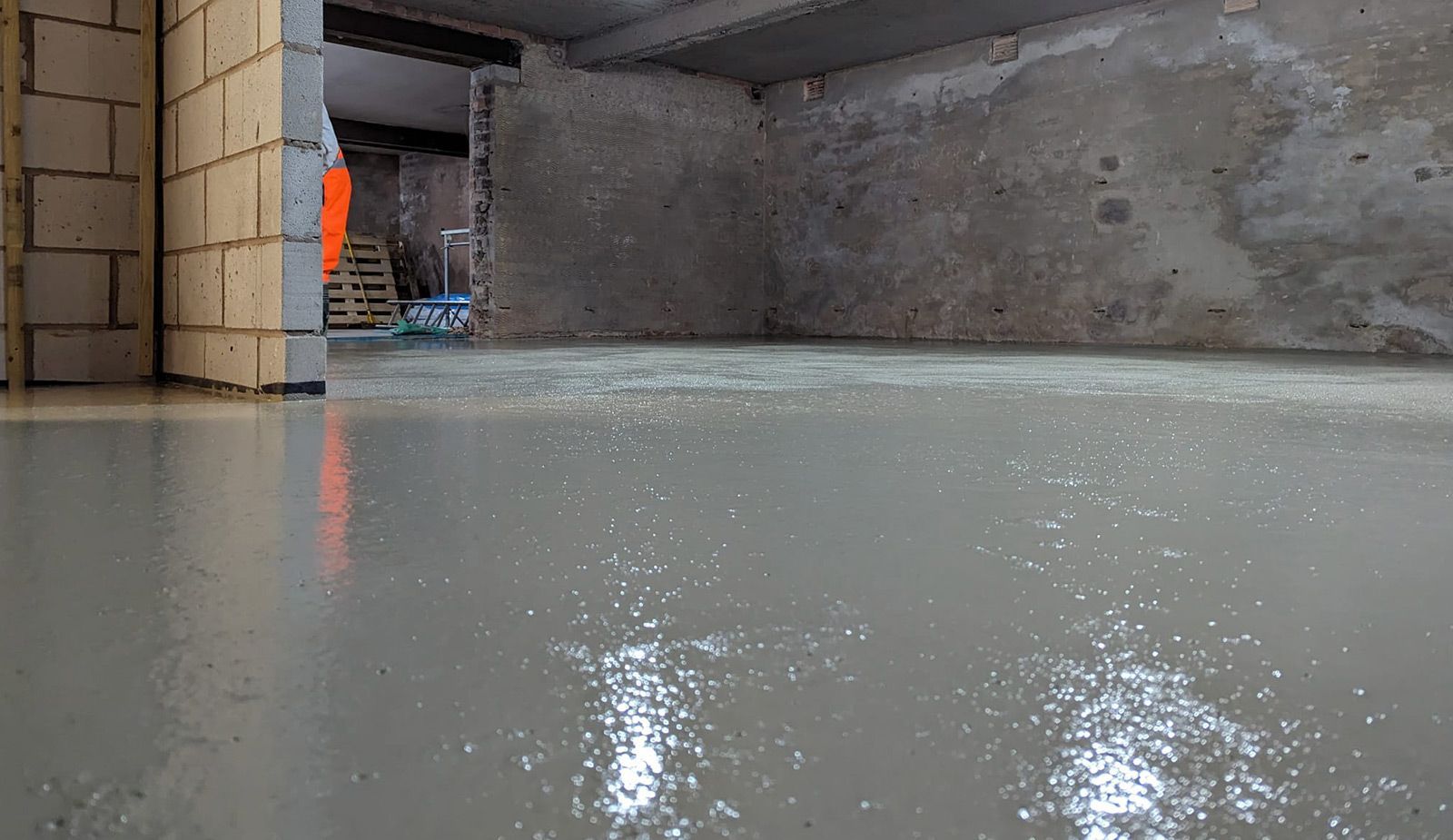
Here, we outline ways to avoid creating a poor screed when working on your project.
INCORRECT QUANTITIES AND POOR MIXING OF FLOOR SCREED
For small projects, hand-mixed screeds can be a good choice. However, you must pay attention to the mixing. If the cement, aggregates and water aren’t added in the correct quantities, or the screed isn’t mixed properly, the resulting screed may not have the strength needed to withstand the expected loads. This is because of the formation of small pockets of unmixed materials that prevent the screed from developing its required strength.
An alternative to hand-mixed screeds is to use a forced action mixer which is likely to produce a substrate that is strong and of high quality.

SCREED MUST BE GIVEN ENOUGH TIME TO ADEQUATELY DRY AND CURE
Installing a final floor covering onto a floor screed that hasn’t been given time to adequately dry and cure can result in buckling, musty smells, the growth of mould, swelling and blisters.
It is advisable to avoid using ventilation or heat to speed up the drying process as this often produces a low-quality floor screed that is likely to crack.
Traditional dry screeds laid at a depth of 75mm require 7 days to cure and around 110 days to dry. Cement based liquid screeds, like the screed supplied by Clockwork Screed, are ideal for projects with limited timescales because they only require 28 days for complete drying. Our fast-drying liquid floor screed can take as little as 7 days to dry.
MAINTAIN THE FLATNESS OF YOUR FLOOR SCREED TO AVOID DEVIATIONS
To achieve a flat floor, the screed on the sub-floor must have no bumps or dips, otherwise it is likely to crack under the pressure of footfall. An uneven sub-floor can also cause delays to your project and incur remedial costs that could have been avoided if the floor screed was sufficiently flat.
Deviations in the flatness of your floor screed can be measured using a feeler gauge.
ABSENCE OF TEMPORARY SPEED PROTECTION
Temporary speed protection should be applied to floor screed until the final finish is installed. The application of temporary speed protection such as plywood boards, will maintain the integrity of the screed.
A lack of temporary screed protection could result in damage to the surface of the screed, cracks, or failures within the slab thus affecting its performance and voiding any warranty agreements.
EXCESSIVE DEPARTURE FROM DATUM
Departure from datum refers to the deviation in height of the surface of all new floors in construction. Floor screed should only deviate within +/- 15mm of the mean floor level. Tighter tolerances may be required for small rooms.
Clockwork Screed use high quality laser levels and levelling devices to ensure an accurate measurement from datum. This, in turn, results in reduced tolerances and therefor, flatter floors.
For more information on HOW TO AVOID A POOR SCREED FOR YOUR BUILD PROJECT talk to Clockwork Screed Ltd